road and workshop
Page 41
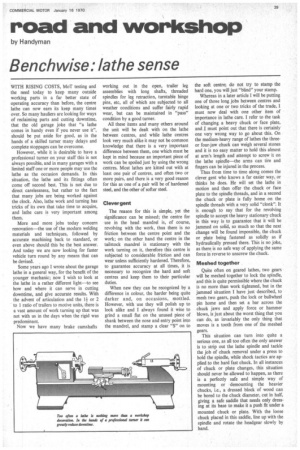
If you've noticed an error in this article please click here to report it so we can fix it.
by Handyman
Benchwise: lathe sense
WITH RISING COSTS, MoT testing and the need today to keep many outside working parts in a far better state of operating accuracy than before, the centre lathe can now earn its keep many times over. So many hauliers are looking for ways of reclaiming parts and cutting downtime, that the old garage joke that "a lathe comes in handy even if you never use it", should be put aside for good, as in the hands of a skilled turner many delays and complete stoppages can be overcome.
However, while it is desirable to have a professional turner on your staff this is not always possible, and in many garages with a limited staff one or more people may use the lathe as the occasion demands. In this situation, the lathe and its fittings often come off second best. This is not due to direct carelessness, but rather to the fact that many jobs are being worked against the clock. Also, lathe work and turning has tricks of its own that take time to acquire, and lathe care is very important among them.
More and more jobs today concern renovation—the use of the modern welding materials and techniques, followed by accurate machining back to standard, or even above should this be the best answer.
And today we are now looking for faster vehicle turn round by any means that can be devised.
Some years ago I wrote about the garage lathe in a general way, for the benefit of the younger mechanic; now I wish to look at the lathe in a rather different light—to see how and where it can serve in cutting downtime, and give accurate results. With the advent of articulation and the 1+ or 2 to 1 ratio of trailers to motive units, there is a vast amount of work turning up that was not with us in the days when the rigid was predominant.
Now we have many brake camshafts working out in the open, trailer leg assemblies with long shafts, threaded spindles for leg retraction, turntable hinge pins, etc, all of which are subjected to all weather conditions and suffer fairly rapid wear, but can be maintained in "pass" condition by a good turner.
All these items and many others around the unit will be dealt with on the lathe between centres, and while lathe centres look very much alike it may not be common knowledge that there is a very important difference between them, one which must be kept in mind because an important piece of work can be spoiled just by using the wrong centres. Most lathes are kitted out with at least one pair of centres. and often two or more pairs, and there is a very good reason for this as one of a pair will be of hardened steel, and the other of softer steel.
Clever gent The reason for this is simple, yet the significance can be missed; the centre for use in the head mandrel is, of course, revolving with the work, thus there is no friction between the centre point and the work; on the other hand the centre in the tailstock mandrel is stationary with the work turning on it, therefore this centre is subjected to considerable friction and can wear unless sufficiently hardened. Therefore, to guarantee accuracy at all times, it is necessary to recognize the hard and soft centres and keep them to their particular duties.
When new they can be recognized by a difference in colour, the harder being quite darker and, on occasions, mottled. However, with use they will polish up to look alike and I always found it wise to grind a small flat on the unused piece of shank between the nose and entry point into the mandrel, and stamp a clear "S" on to the soft centre; do not try to stamp the hard one, you will just "blind" your stamp.
Whereas in a later article I will be putting one of those long jobs between centres and looking at one or two tricks of the trade, I must now deal with one other item of importance in lathe care. I refer to the task of changing a heavy chuck or face plate, and I must point out that there is certainly one very wrong way to go about this. On the medium-heavy range of lathes the threeor four-jaw chuck can weigh several stones and it is no easy matter to hold this almost at arm's length and attempt to screw it on the lathe spindle—the arms can tire and fingers can be injured in the process.
Thus from time to time along comes the clever gent who knows a far easier way, or thinks he does. He will set the lathe in motion and then offer the chuck or face plate to the spindle threads, and in a second the chuck or plate is fully home on the spindle threads with a very solid "clonk". It is enough to say that for the revolving spindle to accept the heavy stationary chuck in this way is to guarantee that it will be jammed on solid, so much so that the next change will be found impossible, the chuck or plate being fastened as solidly as if hydraulically pressed there. This is no joke, as there is no safe way of applying the same force in reverse to unscrew the chuck.
Meshed together Quite often on geared lathes, two gears will be meshed together to lock the spindle, and this is quite permissible where the chuck is no more than work tightened, but in the jammed situation I have just described, to mesh two gears, push the lock or bullwheel pin home and then set a bar across the chuck jaws and apply force or hammer blows, is just about the worst thing that you can do, as invariably the only thing that moves is a tooth from one of the meshed gears.
This situation can turn into quite a serious one, as all too often the only answer is to strip out the lathe spindle and tackle the job of chuck removal under a press to hold the spindle, while shock tactics are applied to the hard fast chuck. In all instances of chuck or plate changes, this situation should never be allowed to happen, as there is a perfectly safe and simple way of mounting or demounting the heavier chucks, i.e.. a dressed block of wood can be bored to the chuck diameter. cut in half, giving a safe saddle that needs only dressing at its base to make it a push fit under a mounted chuck or plate. With the loose chuck placed in this saddle, line up with the spindle and rotate the headgear slowly by hand.