road and
Page 54
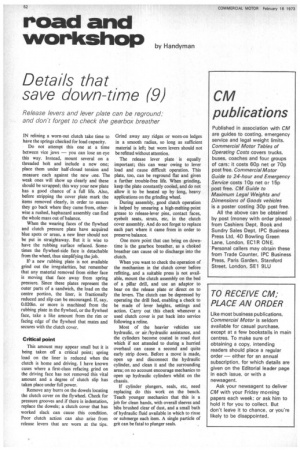
If you've noticed an error in this article please click here to report it so we can fix it.
workshop by Handyman
Details that save down-time (9)
Release levers and lever plate can be reground: and don't forget to check the gearbox breather
IN relining a worn-out clutch take time to have the springs checked for load capacity.
Do not attempt this one at a time between vice jaws — you can lose an eye this way. Instead, mount several on a threaded bolt and include a new one; place them under half-closed tension and measure each against the new one. The weak ones will show up clearly and these should be scrapped; this way your new plate has a good chance of a full life. Also, before stripping the cover plate mark the items removed clearly, in order to ensure they go back where they came from, otherwise a rushed, haphazard assembly can find the whole mass out of balance.
When the wearing faces of the flywheel and clutch pressure plate have acquired blue spots or areas, a new liner should not be put in straightaway. But it is wise to have the rubbing surface refaced. Sometimes the flywheel-side face is detachable from the wheel, thus simplifying the job.
If a new rubbing plate is not available grind out the irregularities, but remember that any material removed from either face is moving that face away from spring pressure. Since these plates represent the outer parts of a sandwich, the load on the centre portion, the liner, is fractionally reduced and slip can be encouraged. If, say, 0.020in. or more is machined from the rubbing plate in the flywheel, or the flywheel face, take a like amount from the rim or facing edge of the flywheel that mates and secures with the clutch cover.
Critical point This amount may appear small but it is being taken off a critical point; spring load on the liner is reduced when the clutch is home and driving. I have known cases where a first-class refacing grind on the driving face has not removed this vital amount and a degree of clutch slip has taken place under full power.
Remove any burrs on the dowels locating the clutch cover on the flywheel. Check for pressure grooves and if there is indentation, replace the dowels; a clutch cover that has worked slack can cause this condition. Poor clutch action can also arise from release levers that are worn at the tips.
Grind away any ridges or worn-on ledges in a smooth radius, so long as sufficient material is left; but worn levers should not be refitted without attention.
The release lever plate is equally important; this can wear owing to lever load and cause difficult operation. This plate, too, can be reground flat and given a further trouble-free life. When grinding, keep the plate constantly cooled, and do not allow it to be heated up by long, heavy applications on the grinding wheel.
During assembly, good clutch operation is helped by smearing a high-melting-point grease to release-lever pins, contact faces, eyebolt seats, struts, etc, in the clutch cover assembly. And do not forget to replace each part where it came from in order to preserve balance.
One more point that can bring on downtime is the gearbox breather, as a choked breather can cause oil to discharge into the clutch.
When you want to check the operation of the mechanism in the clutch cover before refitting, and a suitable press is not available, mount the clutch assembly on the bed of a pillar drill, and use an adaptor to bear on the release plate or direct on to the levers. The clutch can be depressed by operating the drill feed, enabling a check to be made of lever heights, settings and action. Carry out this check whenever a used clutch cover is put back into service following a reline.
Most of the heavier vehicles use hydraulic, or air /hydraulic assistance, and the cylinders become coated in road dust which if not attended to during a hurried overhaul can cause a second and quite early strip down. Before a move is made, open up and disconnect the hydraulic cylinder, and clean it and the surrounding area; on no account encourage mechanics to open up hydraulic cylinders whilst on the chassis.
If cylinder plungers, seals, etc, need replacing do this work on the bench. Teach younger mechanics that this is a job for clean hands, with overall sleeves and bibs brushed clear of dust, and a small bath of hydraulic fluid available in which to rinse or submerge each item. A single particle of grit can be fatal to plunger seals.