Don't overlook overhead costs
Page 69
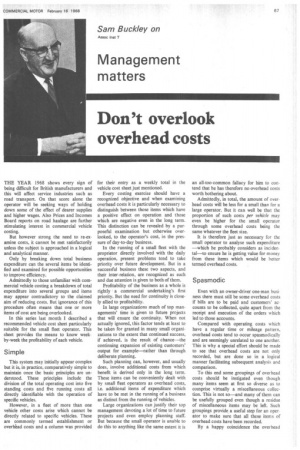
Page 70
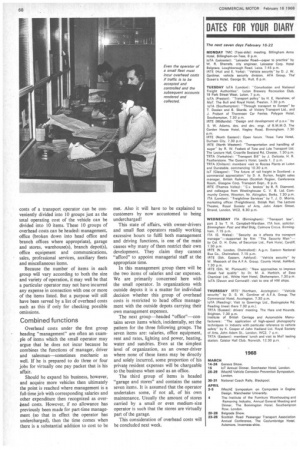
If you've noticed an error in this article please click here to report it so we can fix it.
THE YEAR 1968 shows every sign of being difficult for British manufacturers and this will affect service industries such as road transport. On that score alone the operator will be seeking ways of holding down some of the effect of dearer supplies and higher wages. Also Prices and Incomes Board reports on road haulage are further stimulating interest in commercial vehicle costing.
But however strong the need to re-examine costs, it cannot be met satisfactorily unless the subject is approached in a logical and analytical manner.
Only by breaking down total business expenditure can the several items be identified and examined for possible opportunities to improve efficiency.
Admittedly to those unfamiliar with commercial vehicle costing a breakdown of total expenditure into several groups and items may appear contradictory to the claimed aim of reducing costs. But ignorance of this procedure often means that one or more items of cost are being overlooked.
In this series last month I described a recommended vehicle cost sheet particularly suitable for the small fleet operator. This sheet provides the means to know weekby-week the profitability of each vehicle.
Simple
This system may initially appear complex but it is, in practice, comparatively simple to maintain once the basic principles are understood. These principles include the division of the total operating cost into five standing costs and five running costs all directly identifiable with the operation of specific vehicles.
However, in a fleet of more than one vehicle other costs arise which cannot be directly related to specific vehicles. These are commonly termed establishment or overhead costs and a column was provided for their entry as a weekly total in the vehicle cost sheet just mentioned.
Every costing exercise should have a recognized objective and when examining overhead costs it is particularly necessary to distinguish between those items which have a positive effect on operation and those which are negative even in the long term. This distinction can be revealed by a purposeful examination but otherwise overlooked, to the operator's cost, in the pressure of day-to-day business.
In the running of a small fleet with the proprietor directly involved with the daily operation, present problems tend to take priority over future development. But in a successful business these two aspects, and their inter-relation, are recognized as such and due attention is given to both of them.
Profitability of the business as a whole is rightly a commercial undertaking's first priority. But the need for continuity is closely allied to profitability.
In large organizations much of top managements' time is given to future projects that will ensure the continuity. When not actually ignored, this factor tends at least to be taken for granted in many small organizations to the extent that continued success, if achieved, is the result of chance—the continuing expansion of existing customers' output for example—rather than through deliberate planning.
Such planning can, however, and usually does, involve additional costs from which benefit is derived only in the long term. These items can be conveniently dealt with by small fleet operators as overhead costs, i.e. additional items of expenditure which have to be met in the running of a business as distinct from the running of vehicles.
Large organizations can justify their top management devoting a lot of time to future projects and even employ planning staff. But because the small operator is unable to do this to anything like the same extent it is an all-too-common fallacy for him to contend that he has therefore no overhead costs worth bothering about.
Admittedly, in total, the amount of overhead costs will be less for a small than for a large operator. But it can well be that the proportion of such costs per vehicle may even be higher for the small operator through some overhead costs being the same whatever the fleet size.
It is therefore just as necessary for the small operator to analyse such expenditure which he probably considers as inciden tal—to ensure he is getting value for money from these items which would be better termed overhead costs.
Spasmodic
Even with an owner-driver one-man business there must still be some overhead costs if bills are to be paid and customers' accounts to be collected, quite apart from the receipt and execution of the orders which led to those accounts.
Compared with operating costs which have a regular time or mileage pattern, overhead costs tend to occur spasmodically and are seemingly unrelated to one another. This is why a special effort should be made to see that overhead costs are not only recorded, but are done so in a logical manner facilitating subsequent analysis and comparison.
To this end some .groupings of overhead costs should be instigated even though many items seem at first so diverse as to comprise virtually a miscellaneous collection. This is not so—and many of them can be usefully grouped even though a residue of miscellaneous items may be left. Such groupings provide. a useful step for an operator to make sure that all these items of overhead costs have been recorded.
By a happy coincidence the overhead costs of a transport operator can be conveniently divided into 10 groups just as the total operating cost of the vehicle can be divided into 10 items. These 10 groups of overhead costs can be headed: management, office (broken down into head office and branch offices where appropriate), garage and stores, warehouse(s), branch depot(s), office equipment and communications, sales, professional services, auxiliary fleets and miscellaneous items.
Because the number of items in each group will vary according to both the size and variety of operation, it may well be that a particular operator may not have incurred any expense in connection with one or more of the items listed. But a purpose will still have been served by a list of overhead costs such as this if only for checking possible omissions.
Combined functions
Overhead costs under the first group heading "management" are often an example of items which the small operator may argue that he does not incur because he combines the functions of manager, driver and salesman—sometimes mechanic as well. If he is prepared to do three or four jobs for virtually one pay packet that is his affair.
Should he expand his business, however, and acquire more vehicles then ultimately the point is reached where management is a full-time job with corresponding salaries and other expenditure then recognized as over.tiead costs. However, if no allowance has previously been made for part-time management (so that in effect the operator has undercharged), then the time comes when there is a substantial addition to cost to be met. Also it will have to be explained to customers by now accustomed to being undercharged!
This state of affairs, with owner-drivers and small fleet operators readily working excessive hours to fulfil both management and driving functions, is one of the main causes why many of them restrict their own development. They claim they cannot "afford" to appoint managerial staff at the appropriate time.
In this management group there will be the two items of salaries and car expenses. We are primarily concerned here with the small operator. In organizations with outside depots it is a matter for individual .decision whether this group of overhead costs is restricted to head office management with the outside depots carrying their own management expenses.
The next group—headed "office"—contains seven items which, incidentally, set the pattern for the three following groups. The seven items are: salaries, office equipment, rent and rates, lighting and power, heating, water and sundries. Even at the simplest level of organization, as an owner-driver where none of these items may be directly and solely incurred, some proportion of his privaq resident expenses will be chargeable to the business when used as an office.
The third group of items is headed "garage and stores" and contains the same seven items. It is assumed that the operator undertakes some, if not all, of his own maintenance. Usually the amount of stores carried by a small or even medium-size operator is such that the stores are virtually part of the garage.
This consideration of overhead costs will be concluded next week.