Pressure for dry powders, road and rail
Page 64
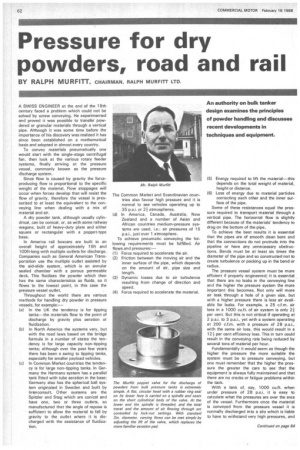
Page 66
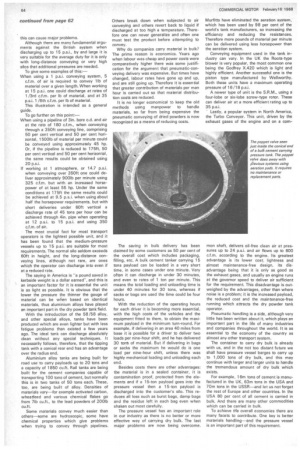
If you've noticed an error in this article please click here to report it so we can fix it.
BY RALPH MURFITT, CHAIRMAN. RALPH MURFITT LTD.
A SWISS ENGINEER at the end of the 19th century faced a problem which could not be solved by screw conveying. He experimented and proved it was possible to transfer powdered or granular materials through a vertical pipe. Although it was some time before the importance of his discovery was realized it has since been established on a mathematical basis and adopted in almost every country.
To convey materials pneumatically one would start with the single-stage centrifugal fan, then look at the various rotary feeder systems, finally arriving at the pressure vessel, commonly known as the pressure discharge system.
Since flow is caused by gravity the forceproducing flow is proportional to the specific weight of the material. Flow stoppages will occur when forces develop that will resist the flow of gravity, therefore the vessel is pressurized to at least the equivalent to the conveying line when dealing with a mix of material and air.
A dry powder tank, although usually cylindrical, can be conical, or, as with some railway wagons, built of heavy-duty plate and either square or rectangular with a poppet-type base.
In America rail boxcars are built to an. overall height of approximately 15ft and 100ft-long with multiple outlets for discharge. Companies such as General American Transportation use the multiple outlet assisted by the aid-slide system, which is an annular sealed chamber with a porous permeable deck. This fluidizes the powder which then has the same characteristics as fluids, so it flows to the lowest point, in this case the pressure vessel outlet.
Throughout the world there are various methods for handling dry powder in pressure vessels, for example:—
(a) In the UK the tendency is for tipping tanks—the materials flow to the point of discharge by gravity plus aeration or fluidization.
(b) In North America the systems vary, but with the road laws based on the bridge formula in a number of states the tendency is for large capacity non-tipping tanks; although over the past few years there has been a swing to tipping tanks, especially for smaller payload vehicles.
(c) In Common Market countries the tendency is for large non-tipping tanks. In Germany the Hermans system has a parallel tank fitted with tube aeration in the base; Germany also has the spherical ball system originated in Sweden and built by Interconsult. Other systems are the Spitzler and Stag which are conical and have one, two or three outlets, so manufactured that the angle of repose is sufficient to allow the material to fall by gravity to the outlet where it is discharged with the assistance of fluidization. The Common Market and Scandinavian countries also favour high pressure and it is normal to see vehicles operating up to 35 psi. or 2+ atmospheres.
(d) In America, Canada, Australia, New Zealand and a number of Asian and African countries medium-pressure systems are used, i.e.: air pressures of 15 psi., just over 1 atmosphere.
To achieve pneumatic conveying the following requirements must be fulfilled. Air flows.and pressures: (11 Force required to accelerate the air.
(2) Friction between the moving air and the inner surface of the pipe, which depends on the amount of air, pipe size and length.
(3) Dynamic losses due to air turbulence resulting from change of direction and speed.
(4) Force required to accelerate the material.
The Murfitt poppet valve for the discharge of powders from bulk pressure tanks is extremely simple. A flat, circular head with a rubber ring seal on its lower face is carried on a spindle and seats on the short cylindrical body of the valve. At the lower end the spindle is threaded, and the total travel and the amount of air flowing through are controlled by lock-nut settings. With standard 3M. diameter, varying flows can be met simply by adjusting the lift of the valve, which replaces the more familiar aeration pad {5) Energy required to lift the material—this depends on the total weight of material, height or distance.
(6) Loss of energy due to material particles contacting each other and the inner surface of the pipe.
Some of these resistances equal the pressure required to transport material through a vertical pipe. The horizontal flow is slightly different because of the materials' tendency to drag on the bottom of the pipe.
To achieve the best results it is essential that the pipes are of smooth clean bore and that the connections do not protrude into the pipeline or have any unnecessary obstructions. Bends must be at least six times the diameter of the pipe and so constructed not to create turbulence or packing up in the bend or radius.
The pressure vessel system must be more efficient if properly engineered; it is essential that /here are no leaks in the conveying line and the higher the pressure system the more important this becomes. Not only will more air leak through a hole of a given size, but with a higher pressure there is less air available for leaks. For example, a 25 c.f.rn. air loss in a 1000 cuit. of air system is only 21 per cent. But this is not critical if operating at 2 psi. to 3 ps.i., yet with a system operating at 200 c.f.m. with a pressure of 28 p.s.i., with the same air loss, this would result in a 121 per cent efficiency loss. This in turn could result in the conveying rate being reduced by several tons of material per hour.
Fundamentally it would seem as though the higher the pressure the more suitable the system must be to pressure conveying, but one must remember that the higher the pressure the greater the care to seeP that the equipment is always fully maintained arid that there are no cracks or fatigue problems within the tank.
With a tank of, say, 1000 cuft. when under pressure of 28 p.s.i. it is easy to calculate what the pressures are over the area of the vessel. Furthermore once the material is conveyed from the pressure vessel it is normally discharged into a silo which is liable to have to withstand very high pressures, and this can cause major problems.
AJthough there are many fundamental arguments against the British system when discharging up to 15 p.s.i., by and large it is very suitable for the average duty for it is only with long-distance conveying or very high silos that additional pressures are needed.
To give some examples of this:—
When using a 1 p.s.i. conveying system, 5 c.f.m. of air is required to convey 1 lb of material over a given length. When working at 15 p.s.i. one could discharge at rates of 1 /3rd c.f.m. per lb of material, and at 35 ps.i.1 /6th c.f.m. per lb of material.
This illustration is intended as a general guide.
To go further on this point:—
When using a pipeline of 3in. bore o.d. and air at the rate of 180 c.f.m., when conveying through a 350ft conveying tine, comprising 50 per cent vertical and 50 per cent horizontal, 1500lb of material per minute could be conveyed using approximately 45 hp. Or, if the pipeline is reduced to 175ft, 50 per cent vertical and 50 per cent horizontal, the same results could be obtained using 20 p.s.i.
If working at 1 atmosphere, or 14.7 psi. when conveying over 350ft one could deliver approximately 900113 per minute using 325 c.f.m. but with an increased horsepower of at least 55 hp. Under the same conditions at 175ft the same results could be achieved at 9.5 p.s.i. when using about half the horsepower requirements, but with short deliveries under 60ft vertical a discharge rate of 45 tons per hour can be achieved through 4in pipe when operating at 12 p.s.i. to 15 p.s.i. and using 350 c.f.m. of air.
The most crucial fact for most transport operators is the lightest possible unit, and it has been found that the medium-pressure vessels up to 15 psi. are suitable for most requirements. The normal silo seldom exceeds 60ft in height, and the long-distance conveying lines, although not rare, are ones which the operator can discharge into even if at a reduced rate.
The saying in America is "a pound saved in kerbside weight is a dollar earned", and this is an important factor for it is essential the unit is as light as possible. It is obvious that the lower the pressure the thinner the gauge of material can be when based on identical materials, thus aluminium alloys have played an important part in the dry powder tank field.
With the introduction of the 58/58 alloy, and other special alloys, tanks have been produced which are even lighter but with less fatigue problems than existed a few years ago. The ideal tank can discharge absolutely clean without any special techniques. It necessarily follows, therefore, that the tipping tank with a conical rear end has an advantage over the radius end.
Aluminium alloy tanks are being built for road use to carry payloads up to 20 tons and a capacity of 1850 cu.ft. Rail tanks are being built for the cement companies capable of transporting 100 tons of cement, but normally this is in two tanks of 50 tons each. These, too, are being built of alloy. Densities of materials vary—for example activated carbon, wheatfeed and various chemical flakes go from 7Ib cu.ft., to the lead powders of 200lb cu.ft.
Some materials convey much easier than others—some are hydroscopic, some have chemical properties which give problems when trying to convey through pipelines. Others break down when subjected to air conveying and others revert back to liquid if discharged at too high a temperature. Therefore one can never generalize and often one must test the product before attempting to convey.
Why do companies carry material in bulk? The prime reason is economics. Years ago when labour was cheap and power costs were comparatively higher there was some justification for the argument that pneumatic-conveying delivery was expensive. But times have changed, labour rates have gone up and up, and are still going up. Therefore it is essential that greater contribution of materials per man hour is carried out so that material distribution costs are reduced.
It is no longer economical to keep the old methods using manpower to handle materials, so far from being expensive the pneumatic conveying of dried powders is now recognized as a means of reducing costs.
The saving in bulk delivery has been claimed by some customers as 50 per cent of the overall cost which includes packaging, filling, etc. A bulk cement tanker carrying 15 tons payload can be loaded in a very short time, in some cases under one minute. Very often it can discharge in under 30 minutes, and even to rates of 1 ton per minute. This means the total loading and unloading time is under 40 minutes for 30 tons, whereas if sacks or bags are used the time could be four hours.
With the reduction of the operating hours for each driver it is becoming more essential, with the high costs of the vehicles and the equipment fitted to them, to obtain the maximum payload in the minimum turn-round. For example, if delivering in an area 40 miles from base it is possible for a driver to deliver two loads per nine-hour shift, and he has delivered 30 tons of material. But if delivering in bags or sacks the maximum he would do is one load per nine-hour shift, unless there was highly mechanical loading and unloading each end.
Besides costs there are other advantages: the material is in a sealed container, it is contamination proof, protected from the elements and if a 15-ton payload goes into the pressure vessel then a 15-ton payload is discharged into the customer's silo. This reduces all loss such as burst bags, damp bags and the residue left in each bag even when shaken out most carefully.
The pressure vessel has an important role in our industry as there is no better or more effective way of carrying dry bulk. The last major problems are now being overcome. IVIurfitts have eliminated the aeration system, which has been used by 98 per cent of the world's tank manufacturers, so increasing the efficiency and reducing the resistances. Therefore more pounds of material per minute can be delivered using less horsepower than the aeration system.
Conveying equipment used in the tank industry can vary. In the UK the Roots-type blower is very popular, the most common one being the Godfrey X.420 which is light and highly efficient. Another successful one is the piston type manufactured by Wellworthy. Both these units have a maximum operating pressure of 16 /18 p.s.i.
A newer type of unit is the S.R.M., using a four-lobe or six-lobe screw-type rotor. These can deliver air at a more efficient rating up to 35 psi. • Lastly, a popular system in North America, the Turbo Conveyor. This unit, driven by the exhaust gases of the engine and on a corn mon shaft, delivers oil-free clean air at pressures up to 24 p.s.i. and air flows up to 600 a.m. according to the engine. Its greatest advantage is its lower cost, lightness and almost maintenance-free design, its disadvantage being that it is only as good as the exhaust gases, and usually an engine runs at the governor speed to deliver air sufficient for the requirement. This disadvantage is outweighed by the advantages, other than where noise is a problem; it is the increased payload, the reduced cost and the maintenance-free running which attracts the dry powder tank operator.
Pneumatic handling is a side, although very little has been written about it, which plays an important part in the life of many industries and companies throughout the world. It is as essential to the economy of the country as almost any other transport system.
The container to carry dry bulk is already with us, and in the not too distant future we shall have pressure vessel barges to carry up , to 1,000 tons of dry bulk, and this may continue with larger and larger units to handle the tremendous amount of dry bulk which exists.
For example, 18m tons of cement is manufactured in the UK, 63m tons in the USA and 70rn tons in the USSR—and let us not forget the rest of Europe and other countries. In the USA 80 per cent of all cement is carried in bulk. And there are many other commodities which can be carried in bulk.
To achieve tHe overall economies there are many facets to contribute. One key is better materials handling—and the pressure vessel is an important part of this requirement.