New Leyland Steel-framed Goods Body
Page 32
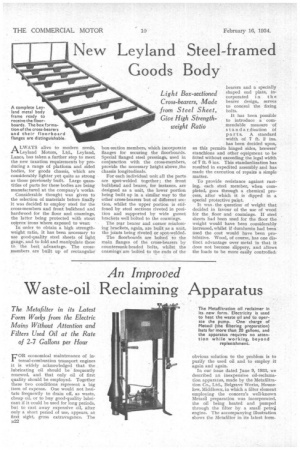
If you've noticed an error in this article please click here to report it so we can fix it.
ALWAYS alive to modern needs, Leyland Motors, Ltd., Leyland, Lanes, has taken a further step to meet the new taxation requirements by producing a range of platform and sided bodies, for goods chassis, which are considerably lighter yet quite as strong as those previously built. Large quantities of parts for these bodies are being manufactured at the company's works,
Considerable thought was given to the selection of materials before finally it was decided to employ steel for the cross-members and front bulkhead and hardwood for the floor and coamings, the latter being protected with stout convex irons where exposed to Wear;
In order to obtain a high strengthweight ratio, it has been necessary to use good-quality steel sheets of light gauge, and to fold and manipulate these to, the best advantage. The crossmembers are built up of rectangular.
box-section members, which incorporate flanges for securing the floorboards. Special flanged steel pressings, used in conjunction with the cross-members, provide the necessary height above the chassis longitudinals.
For each individual unit all the parts. are spot-welded together ; the front bulkhead and bearer, for instance, are designed as a unit, the lower portion being built up in a similar way to the other cross-bearers but of different section, whilst the upper portion is stiffened by steel sections riveted in position and supported by wide gusset brackets well bolted to the coarnings.
The rear bearer and corner reinforcing brackets, again, are built as a unit, the joints being riveted or spot-welded.
The floorboards are bolted to the main flanges of the cross-bearers by countersunk-headed bolts, whilst the coamings are bolted to the ends of the bearers and a specially shaped end plate, incorporated in the bearer design, serves to conceal the fixing bolts.
it has been possible to introduce a • commendable measure of standardization of part s. A standard width of 7 ft. 2 ins.
has been decided upon, as this permits hinged sides, brewers' stanchions and other equipment to be fitted without exceeding the legal width of 7 ft. 6 ins. This standardization has resulted in expedited assembly and has made the execution of repairs a simple matter.
To provide resistance against rusting, each steel member, when completed, goes through a chemical process, after which it is dipped in a special protective paint.
It was. the question of weight that decided in favour of the use of wood fOr the floor and coarnings. If steel sheets had been used for the floor the weight would have been considerably increased, whilst if duralumin had been lised the cost would have been prohibitive. Wood, of course, has one distinct advantage over metal in that it does not become slippery, and allows the loads to be more easily controlled.