Effi axi t generation rom Eaton
Page 20
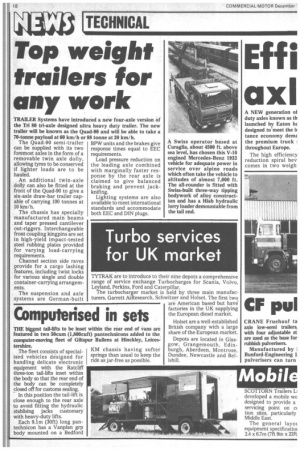
Page 21
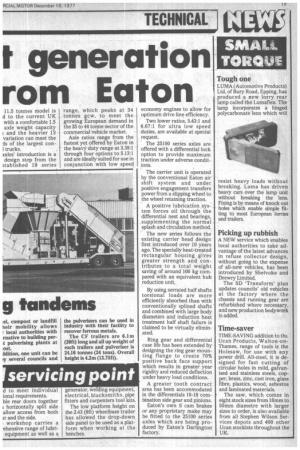
If you've noticed an error in this article please click here to report it so we can fix it.
A NEW generation of duty axles known as th launched by Eaton III designed tosmeet the l( tance economy demE the premium truck I throughout Europe.
The high efficiency reduction spiral bev comes in two weigh 11.5 tonnes model is d to the current UK, with a comfortable 1.5 axle weight capacity L and the heavier 13 variation can meet the ls of the largest conI_ trucks.
axles' introduction is a design step from the 3tablished 19 series range, which peaks at 34 tonnes gcw, to meet the growing European demand in the 35 to 44 tonne sector of the commercial vehicle market.
Axle ratios range from the fastest yet offered by Eaton in the heavy duty range at 3.38:1 through four options to 5.13:1 and are ideally suited for use in conjunction with low speed economy engines to allow for optimum drive line efficiency.
Two lower ratios, 5.43:1 and 6.67:1 for ultra low speed duties, are available at special request.
The 25100 series axles are offered with a differential lock option to provide maximum traction under adverse conditions.
The carrier unit is operated by the conventional Eaton air• shift system and under, positive engagement transfers power from a slipping wheel to the wheel retaining traction.
A positive lubrication sys. tern forces oil through the differential nest and bearings, .supplementing the normal splash and circulation method.
The new series follows the existing carrier head design first introduced over 10 years ago. The specially heat-treated rectangular housing gives greater strength and contributes to a total weight saving of around 100 kg compared with an equivalent hub reduction unit.
By using serrated half shafts torsional loads are more efficiently absorbed than with conventionally splined shafts and combined with large body diameters and induction heat treatment half shaft failure is claimed to be virtually eliminated.
Ring gear and differential case life has been extended by designing the ring gear mounting flange to create 70% positive back face support which results in greater year rigidity and reduced deflection under heavy load conditions.
A greater tooth contract area has been accommodated in the differentials 10-18 combination side gear and pinions.
Eaton's own S cam brakes or any proprietary make may be fitted to the 25100 series axles which are being produced by Eaton's Darlington factory.