TOUG
Page 40
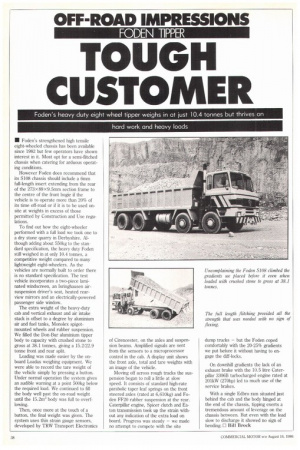
If you've noticed an error in this article please click here to report it so we can fix it.
CUSTOMER Foden's heavy duty eight wheel tipper weighs in at just 10.4 tonnes but thrives on hard work and heavy loads
• Foden's strengthened high tensile eight-wheeled chassis has been available since 1982 but few operators have shown interest in it. Most opt for a semi-flitched chassis when catering for arduous operating conditions.
However Foden does recommend that its S108 chassis should include a 6rnm full-length insert extending from the rear of the 273x89x9.5mm section frame to the centre of the front bogie if the vehicle is to operate more than 20% of its time off-road or if it is to be used onsite at weights in excess of those permitted by Construction and Use regulations.
To find out how the eight-wheeler performed with a full load we took one to a dry stone quarry in Derbyshire. Although adding about 550kg to the standard specification, the heavy duty Foden still weighed in at only 10.4 tonnes, a competitive weight compared to many lightweight eight-wheelers. As the vehicles are normally built to order there is no standard specification. The test vehicle incorporates a two-piece laminated windscreen, an Isringhausen airsuspension driver's seat, heated rearview mirrors and an electrically-powered passenger side window.
The extra weight of the heavy-duty cab and vertical exhaust and air intake stack is offset to a degree by aluminium air and fuel tanks, Monolex spigotmounted wheels and rubber suspension. We filled the Don-Bur aluminium tipper body to capacity with crushed stone to gross at 38.1 tonnes, giving a 15.2/22.9 tonne front and rear split.
Loading was made easier by the onboard Loadax weighing equipment. We were able to record the tare weight of the vehicle simply by pressing a button. Under normal operation the system gives an audible warning at a point 500kg below the required load. We continued to fill the body well past the on-road weight until the 15.2m3 body was full to overflowing.
Then, once more at the touch of a button, the final weight was given. The system uses thin strain gauge sensors, developed by TRW Transport Electronics of Cirencester, on the axles and suspension beams. Amplified signals are sent from the sensors to a microprocessor control in the cab. A display unit shows the front axle, total and tare weights with an image of the vehicle.
Moving off across rough tracks the suspension began to roll a little at slow speed. It consists of standard high-rate parabolic taper leaf springs on the front steered axles (rated at 6,610kg) and Foden FF20 rubber suspension at the rear. Caterpillar engine, Spicer clutch and Eaton transmission took up the strain without any indication of the extra load on board. Progress was steady — we made no attempt to compete with the site dump trucks — but the Foden coped comfortably with the 20-25% gradients we put before it without having to engage the diff-locks.
On downhill gradients the lack of an exhaust brake with the 10.5 litre Caterpillar 3306B turbocharged engine rated at 201kW (270hp) led to much use of the service brakes.
With a single Edbro ram situated just behind the cab and the body hinged at the end of the chassis, tipping exerts a tremendous amount of leverage on the chassis between. But even with the load slow to discharge it showed no sign of bending. 0 Bill Brock