Standard kits increase turn over
Page 36
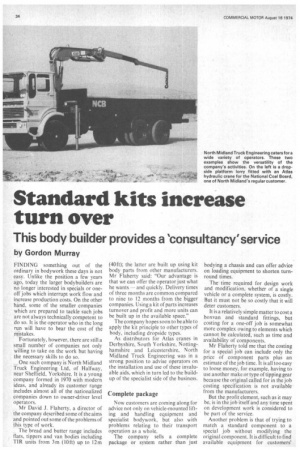
Page 37
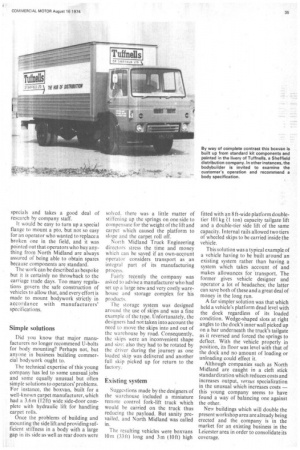
If you've noticed an error in this article please click here to report it so we can fix it.
This body builder provides a 'consultancy' service
by Gordon Murray
FINDING something out of the ordinary in bodywork these days is not easy. Unlike the position a few years ago, today the larger bodybuilders are no longer interested in specials or oneoff jobs which interrupt work flow and increase production costs. On the other hand, some of the smaller companies which are prepared to tackle such jobs are not always technically competent to do so. It is the operator who in the long run will have to bear the cost of the mistakes.
Fortunately, however, there are still a small number of companies not only willing to take on the work but having the necessary skills to do so.
One such company is North Midland Truck Engineering Ltd, of Halfway, near Sheffield, Yorkshire. It is a young company formed in 1970 with modern ideas, and already its customer range includes almost all of the nationalized companies down to owner-driver level operators.
Mr David J. Flaherty, a director of the company described some of the aims and pointed out some of the problems of this type of work.
The bread and butter range includes flats, tippers and van bodies including TIR units from 3m (10ft) up to 12m (40 ft); the latter are built up using kit body parts from other manufacturers. M r Flaherty said: "Our advantage is that we can offer the operator just what he wants — and quickly. Delivery times of three months are common compared to nine to 12 months from the bigger companies. Using a kit of parts increases turnover and profit and more units can be built up in the available space."
The company hopes soon to be able to apply the kit principle to other types of body, including dropside types. As distributors for Atlas cranes in Derbyshire, South Yorkshire, Nottinghamshire and Leicestershire, North Midland Truck Engineering was in a strong position to advise operators on the installation and use of these invaluable aids, which in turn led to the buildup of the specialist side of the business.
Complete package
Now customers are coming along for advice not only on vehicle-mounted lifting and handling equipment and specialist bodywork, but also with problems relating to their transport operation as a whole..
The company sells a complete package or system rather than just bodying a chassis and can offer advice on loading equipment to shorten turnround times.
The time required for design work and modification, whether of a single vehicle or a complete system, is costly. But it must not be so costly that it will deter customers, It is a relatively simple matter to cost a boxvan and standard fittings, but costing for a one-off job is somewhat more complex owing to elements which cannot be calculated, such as time and availability of components.
Mr Flaherty told me that the costing for a special job can include only the price of component parts plus an estimate of the job time. It is all too easy to loose money, for example, having to use another make or type of tipping gear because the original called for in the job costing specification is not available from the manufacturers.
But the profit element, such as it may be, is in the job itself and any time spent on development work is considered to be part of the service.
Another problem is that of trying to match a standard component to a special job without modifying the original component. It is difficult to find available equipment for customers' specials and takes a good deal of research by company staff.
It would be easy to turn up a special flange to mount a pto, but not so easy for an operator who wanted to replace a broken one in the field, and it was pointed out that operators who buy anything from North Midland are always assured of being able to obtain spares because components are standard.
The work can be described as bespoke but it is certainly no throwback to the carriage trade days. Too many regulations govern the safe construction of vehicles to allow that, and every effort is made to mount bodywork strictly in accordancewith manufacturers' specifications.
Simple solutions
Did you know that major manufacturers no longer recommend U-bolts for body mounting? Perhaps not, hut anyone in business building commercial bodywork ought to.
The technical expertise of this young company has led to some unusual jobs and some equally unusual but often simple solutions to operators' problems. For instance, the boxvan, built for a well-known carpet manufacturer, which had a 3.6m (12 ft) wide side-door complete with hydraulic lift for handling carpet rolls.
Once the problems of building and mounting the side lift and providing sufficient stiffness in a body with a large gap in its side as well as rear doors were
solved, there was a little matter of stiffening up the springs on one side to compensate for the-weight of the lift and carpet which caused the platform to slope and the carpet roll off.
North Midland Truck Engineering directors stress the time and money which can be saved if an own-account operator considers transport as an integral part of its manufacturing process.
Fairly recently the company was asked to advise a manufacturer who had set up a large new and very costly warehouse and storage complex for his products.
The storage system was designed around the use of skips and was a fine example of the type. Unfortunately, the designers had not taken into account the need to move the skips into and out of the warehouse by road. Consequently, the skips were an inconvenient shape and sin: also they had to be rotated by the driver during the journey as one loaded skip was delivered and another full skip picked up for return to the factory.
Existing system
Suggestions made by the designers of the warehouse included a miniature remote control fork-lift truck which would be carried on the truck thus reducing the payload. But sanity prevailed. and North Midland was called in.
The resulting vehicles were boxvans 10m (33ft) long and 3m (10 ft) high fitted with an 8 ft-wide-platform doubletier 101 kg (1 ton) capacity tailgate lift and a double-tier side lift of the same capacity. Internal rails allowed two tiers of wheeled skips to be carried inside the vehicle.
This solution was a typical example of a vehicle having to be built around an existing system rather than having a system which takes account of and makes allowances for 'transport. The former gives vehicle designer and operator a lot of headaches; the latter can save both of these and a great deal of money in the long run.
A far simpler solution was that which held a vehicle's platform dead level with the dock regardless of its loaded condition. Wedge-shaped slots at right angles to the dock's inner wall picked up on a bar underneath the truck's tailgate as it reversed and forced the springs to deflect. With the vehicle properly in position, its floor was level with that of the dock and no amount of loading or unloading could effect it.
Although companies such as North Midland are caught in a cleft stick standardization which reduces costs and increases output, versus specialization in the unusual which increases costs — this young company seems to have found a way of balancing one against the other.
New buildings which will double the present workshop area are already being erected and the company is in the market for an existing business in the Leicester area in order to consolidate its coverage.