Cool customers are not
Page 29
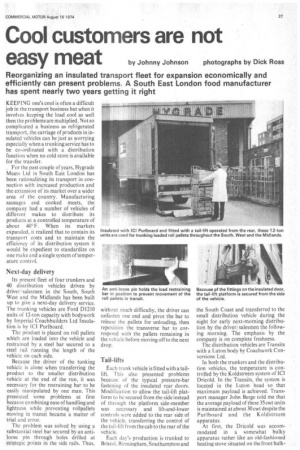
Page 30
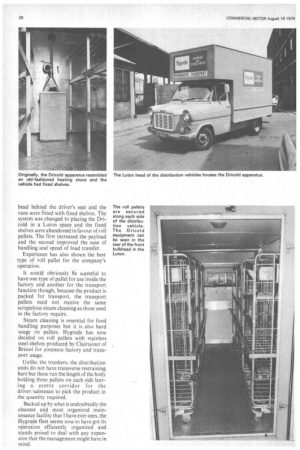
If you've noticed an error in this article please click here to report it so we can fix it.
easy meat by Johnny Johnson photographs by Dick Ross KEEPING one's cool is often a difficult job in the transport business but when it involves keeping the load cool as well then the problems are multiplied. Not so complicated a business as refrigerated transport, the carriage of products in insulated vehicles can be just as worrying especially when a trunking service has to be co-ordinated with a distribution function when no cold store is available for the transfer.
, For the past couple of years, Hygrade Meats Ltd in South East London has been rationalizing its transport in connection with increased production and the extension of its market over a wider area of the country. Manufacturing sausages and cooked meats, the company had a number of vehicles of different makes to distribute its products at a controlled temperature of about 40°F. When its markets expanded, it realized that to contain its transport costs and to maintain the efficiency of its distribution system it would be expedient to standardize on one make and a single system of temperature control.
Next-day delivery Its present fleet of four trunkers and 40 distribution vehicles driven by driver' salesmen in the South, South West and the Midlands has been built up to give a next-day delivery service. The trunking vehicles are Ford DI 210 units of 12-ton capacity with bodywork by Imperial Coachbuilders Ltd Insulation is by ICI Purlboard.
The product is placed on roll pallets which are loaded into the vehicle and restrained by a steel bar secured to a steel rail running the length of the vehicle on each side.
Because the driver of the tunking vehicle is alone when transferring the product to the smaller distribution vehicle at the end of the run, it was necessary for the restraining bar to be easily manipulated by one man. This presented some problems at first because combining ease of handling and lightness while preventing rollpallets moving in transit became a matter of trial and error.
The problem was solved by using a substantial steel bar secured by an antiloose pin through holes drilled at strategic points in the side rails. Thus, without much difficulty, the driver can unfasten one end and pivot the bar to release the pallets for unloading, then reposition the transverse bar to correspond with the pallets remaining in the vehicle before moving off to the next drop.
Tail-lifts Each trunk vehicle is fitted with a taillift. This also presented problems because of the typical pressure-bar fastening of the insulated rear doors. Modification to allow the tail-lift platform to be secured from the side instead of through the platform side-member was necessary and lift-and-lower controls were added to the rear side of the vehicle, transferring the control of the tail-lift from the cab to the rear of the vehicle.
Each day's production is trunked to Bristol. Birmingham, Southampton and the South Coast and transferred to the small distribution vehicle during the night for early next-morning distribution by the driver/salesmen the following morning. The emphasis by the company is on complete freshness.
The distribution vehicles are Transits with a Luton body by Coachwork Conversions Ltd.
In both the trunkers and the distribution vehicles, the temperature is controlled by the Koldstreem system of ICI Dficold. In the Transits, the system is located in the Luton head so that maximum payload is achieved. Transport manager John Berge told me that the average payload of these 35 cwt units is maintained at about 30 cwt despite the Purlboard and the Koldstreem apparatus.
At first, the Dricold was accommodated in a somewhat bulky apparatus rather like an old-fashioned heating stove situated on the front bulk head behind the driver's seat and the vans were fitted with fixed shelves. The system was changed to placing the Dri cold in a Luton space and the fixed shelves were abandoned in favour of roll pallets. The first increased the payload and the second improved the ease of handling and speed of load transfer.
Experience has also shown the best type of roll pallet for the company's Operation.
It would obviously le wasteful to have one type of pallet for use inside the factory and another for the transport function though, because the product is packed for transport, the transport pallets need not receive the same scrupulous steam cleaning as those used in the factory require.
Steam cleaning is essential for food handling purposes but it is also hard usage on pallets. Hygrade has now decided on roll pallets with stainless steel shelves produced by Clairtainer of Bristol for common factory and transport usage.
Unlike the trunkers, the distribution units do not have transverse restraining bars but these run the length of the body holding three pallets on each side leaving a centre corridor for the driver/ salesman to pick the product in the quantity required.
Backed up by what is undoubtedly the cleanest and most organized maintenance facility that I have ever seen, the Hygrade fleet seems now to have got its operation efficiently organized and stands poised to deal with any expansion that the management might have in mind.