Choosing lubricant oils for diesel engines
Page 46
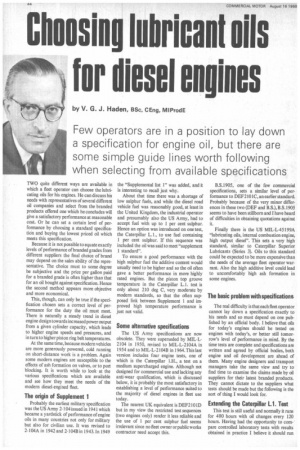
Page 47
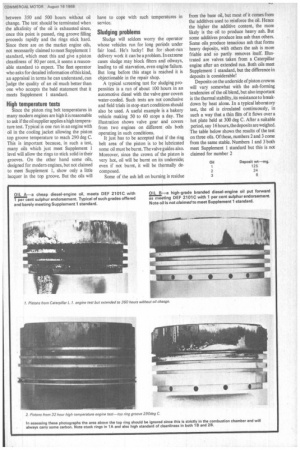
Page 48
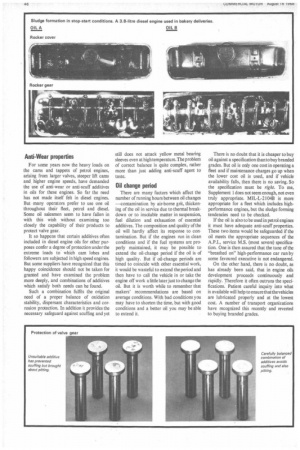
Page 49
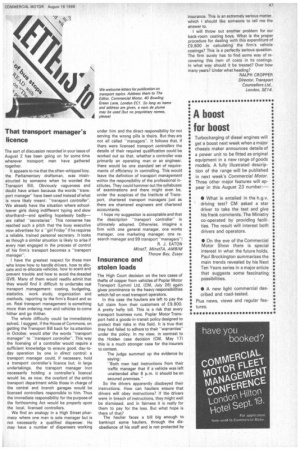
If you've noticed an error in this article please click here to report it so we can fix it.
by V. G. J. Haden, BSc, CEng, MIProdE
Few operators are in a position to lay down a specification for engine oil, but there are some simple guide lines worth following when selecting from available specifications
TWO quite different ways are available in which a fleet operator can choose the lubricating oils for his engines. He can discuss his needs with representatives of several different oil companies and select from the branded products offered one which he concludes will give a satisfactory performance at reasonable cost. Or he can set a certain level of performance by choosing a standard specification and buying the lowest priced oil which meets this specification.
Because it is not possible to equate exactly levels of performance of branded grades from different suppliers the final choice of brand may depend on the sales ability of the representative. The choice must to some degree be subjective and the price per gallon paid for a branded grade is often higher than that for an oil bought against specification. Hence the second method appears more objective and more economical.
This, though, can only be true if the specification chosen sets a correct level of performance for the duty the oil must meet. There is naturally a steady trend in diesel engine design towards increased power output from a given cylinder capacity, which leads to higher engine speeds and pressures, and in turn to higher piston ring belt temperatures.
At the same time, because modern vehicles are more generously powered, cold running on short-distance work is a problem. Again some modern engines are susceptible to the effects of ash formation on valves, or to port blocking. It is worth while to look at the various specifications which are available and see how they meet the needs of the modern diesel-engined fleet.
The origin of Supplement 1
Probably the earliest military specification was the US Army 2-104 issued in 1941 which became a yardstick of performance of engine oils in many countries not only for military but also for civilian use. It was revised to 2-104A in 1942 and 2-104B in 1943. In 1949 the "Supplemental list 1" was added, and it is interesting to recall just why.
About that time there was a shortage of low sulphur fuels, and while the diesel road vehicle fuel was reasonably good, at least in the United Kingdom, the industrial operator and presumably also the US Army, had to accept fuel with up to 1 per cent sulphur. Hence an option was introduced on one test, the Caterpillar L.1., to use fuel containing 1 per cent sulphur. If this sequence was included the oil was said to meet "supplement 1 standard".
To ensure a good performance with the high sulphur fuel the additive content would usually need to be higher and so the oil often gave a better performance in more highly rated engines. But the piston top groove temperature in the Caterpillar L.1. test is only about 210 deg C, very moderate by modern standards, so that the often supposed link between Supplement 1 and improved high temperature performance is just not valid.
Some alternative specifications
The US Army specifications are now obsolete. They were superseded by MIL-L2104 in 1950, revised to MIL-L-2104A in 1954 and to MIL-L-2104B in 1964. This last version includes four engine tests, one of which is the Caterpillar 1.H., a test on a medium supercharged engine. Although not designed for commercial use and lacking any anti-wear qualification, which is discussed below, it is probably the most satisfactory in establishing a level of performance suited to the majority of diesel engines in fleet use today.
The nearest UK equivalent is DEF2101D but in my view the restricted test sequences (two engines only) render it less reliable and the use of 1 per cent sulphur fuel seems irrelevant since no fleet owner or public works contractor need accept this. B.S.1905, one of the few commercial specifications, sets a similar level of performance to DEF 2101C, an earlier standard. Probably because of the very minor differences in these two (DEF and B.S.), B.S.1905 seems to have been stillborn and I have heard of difficulties in obtaining quotations against it.
Finally there is the US MIL-L-45199A "lubricating oils, internal combustion engine, high output diesel". This sets a very high standard, similar to Caterpillar Superior Lubricants (Series 3). Oils to this standard could be expected to be more expensive than the needs of the average fleet operator warrant. Also the high additive level could lead to uncomfortably high ash formation in some engines.
The basic problem with specifications
The real difficulty is that each fleet operator cannot lay down a specification exactly to his needs and so must depend on one published by an official body. I believe that oils for today's engines should be tested on engines with today's, or better still tomorrow's level of performance in mind. By the time tests are complete and specifications are written and agreed by official bodies, both engine and oil development are ahead of them. Many engine designers and transport managers take the same view and try to find time to examine the claims made by oil suppliers for their latest branded products. They cannot dictate to the suppliers what tests should be made but the following is the sort of thing I would look for.
Extending the Caterpillar L.1. Test
This test is still useful and normally it runs for 480 hours with oil changes every 120 hours. Having had the opportunity to corn• pare controlled laboratory tests with results obtained in practice I believe it should run between 350 and 500 hours without oil change. The test should be terminated when the alkalinity of the oil is exhausted since, once this point is passed, ring groove filling proceeds rapidly and the rings stick hard. Since there are on the market engine oils, not necessarily claimed to meet Supplement I standard, which meet this and give a piston cleanliness of 80 per cent, it seems a reasonable standard to expect. The fleet operator who asks for detailed information ofthis kind, an appraisal in terms he can understand, can judge the quality of an oil much better than one who accepts the bald statement that it meets Supplement I standard.
High temperature tests
Since the piston ring belt temperatures in many modern engines are high it is reasonable to ask if the oil supplier applies a high temperature test. Typical is one run in an engine with oil in the cooling jacket allowing the piston top groove temperature to reach 290 deg C. This is important because, in such a test, many oils which just meet Supplement I level will allow the rings to stick solid in their grooves. On the other hand some oils, designed for modern engines, but not claimed to meet Supplement 1, show only a little lacquer in the top groove. But the oils will have to cope with such temperatures in service.
Sludging problems
Sludge will seldom worry the operator whose vehicles run for long periods under fair load. He's lucky! But for short-run delivery work it can be a problem. In extreme cases sludge may block filters and oilways, leading to oil starvation, even engine failure. But long before this stage is reached it is objectionable in the repair shop.
A typical screening test for sludging propensities is a run of about 100 hours in an automotive diesel with the valve gear covers water-cooled. Such tests are not conclusive and field trials in stop-start conditions should also be used. A useful example is a bakery vehicle making 50 to 60 stops a day. The illustration shows valve gear and covers from two engines on different oils both operating in such conditions.
It just has to be accepted that if the ring belt area of the piston is to be lubricated some oil must be burnt. The valve guides also. Moreover, since the crown of the piston is very hot, oil will be burnt on its underside; even if not burnt, it will be thermally decomposed.
Some of the ash left on burning is residue from the base oil, but most of it comes from the additives used to reinforce the oil. Hence the higher the additive content, the more likely is the oil to produce heavy ash. But some additives produce less ash than others. Some oils produce tenacious ash that forms heavy deposits, with others the ash is more friable and so partly removes itself. Illustrated are valves taken from a Caterpillar engine after an extended run. Both oils meet Supplement 1 standard, but the difference in deposits is considerable!
Deposits on the underside of piston crowns will vary somewhat with the ash-forming tendencies of the oil blend, but also important is the thermal stability, its resistance to breakdown by heat alone. In a typical laboratory test, the oil is circulated continuously, in such a way that a thin film of it flows over a hot plate held at 300 deg C. After a suitable period, say 16 hours, the deposits are weighed. The table below shows the results of the test on three oils. Of these, numbers 2 and 3 come from the same stable. Numbers I and 3 both meet Supplement 1 standard but this is not claimed for number 2
Anti-Wear properties
For some years now the heavy loads on the cams and tappets of petrol engines, arising from larger valves, steeper lift cams and higher engine speeds, have demanded the use of anti-wear or anti-scuff additives in oils for these engines. So far the need has not made itself felt in diesel engines. But • many operators prefer to use one oil throughout their fleet, petrol and diesel. Some oil salesmen seem to have fallen in with this wish without examining too closely the capability of their products to protect valve gear.
It so happens that certain additives often included in diesel engine oils for other purposes confer a degree of protection under the extreme loads to which cam lobes and followers are subjected in high speed engines. But some suppliers have recognized that this happy coincidence should not be taken for granted and have examined the problem more deeply, and combinations of additives which satisfy both needs can be found.
Such a combination fulfils the original need of a proper balance of oxidation stability, dispersant characteristics and corrosion protection. In addition it provides the necessary safeguard against scuffing and yet still does not attack yellow metal bearing sleeves even at high temperature. The problem of correct balance is quite complex, rather more than just adding anti-scuff agent to taste.
Oil change period
There are many factors which affect the number of running hours between oil changes —contamination by air-borne grit, thickening of the oil in service due to thermal breakdown or to insoluble matter in suspension, fuel dilution and exhaustion of essential additives. The composition and quality of the oil will hardly affect its response to contamination. But if the engines run in clean conditions and if the fuel systems are properly maintained, it may be possible to extend the oil-change period if the oil is of high quality. But if oil-change periods are timed to coincide with other essential work, it would be wasteful to extend the period and then have to call the vehicle in or take the engine off work a little later just to change the oil. But it is worth while to remember that makers' recommendations are based on average conditions. With bad conditions you may have to shorten the time, but with good conditions and a better oil you may be able to extend it.
There is no doubt that it is cheaper to buy oil against a specification than to buy branded grades. But oil is only one cost in operating a fleet and if maintenance charges go up when the lower cost oil is used, and if vehicle availability falls, then there is no saving. So the specification must be right. To me, Supplement 1 does not seem enough, not even truly appropriate. MIL-L-2104B is more appropriate for a fleet which includes highperformance engines, but the sludge forming tendencies need to be checked.
If the oil is also to be used in petrol engines it must have adequate anti-scuff properties. These two items would be safeguarded if the oil meets the appropriate sequences of the A.P.I., service M.S. (most severe) specification. One is then assured that the tune of the "breathed on" high-performance car run by some favoured executive is not endangered.
On the other hand, there is no doubt, as has already been said, that in engine oils development proceeds continuously and rapidly. Therefore it often outruns the specifications. Patient careful inquiry into what is available will help to ensurethat thevehicles are lubricated properly and at the lowest cost. A number of transport organizations have recognized this recently and reverted to buying branded grades.
The sort of discussion recorded in your issue of August 2 has been going on for some time wherever transport men have gathered together.
It appears to me that the often-whipped boy, the Parliamentary draftsman, was misinstructed by someone when he worded the Transport Bill. Obviously vagueness and doubt have arisen because the words "transport manager" have been used instead of what is more likely meant: "transport controller". We already have the situation where schoolleaver girls doing indifferent typing and slow shorthand—and spelling hopelessly badly— are called "secretaries". This nonsense has reached such a pitch that the busy executive now advertises for a "girl Friday" if he requires a reliable, trained personal secretary, It looks as though a similar situation is likely to arise if every man engaged in the process of control of his firm's transport becomes a "transport manager-.
I have the greatest respect for these men who know how to handle drivers, how to allocate and re-allocate vehicles, how to scent and prevent trouble and how to avoid the dreaded GV9. Many of them would readily admit that they would find it difficult to undertake real transport management: costing, budgeting, statistics, work study, organization and methods, reporting to the firm's Board and so on. Real transport management is something more than ordering men and vehicles to come hither and go thither.
The whole difficulty could be immediately solved, I suggest, if the House of Commons, on getting the Transport Bill back for its attention in October. would alter the words "transport manager" to "transport controller". This way the licensing of a controller would require a sufficient knowledge to ensure good, day-today operation by one in direct control: a transport manager could, if necessary, hold a transport controller's licence but, in large undertakings. the transport manager (not necessarily holding a controller's licence) would be, as now, the overlord of the entire transport department while those in charge of the central and branch garages would be licensed controllers responsible to him. Thus the immediate responsibility for the purpose of the forthcoming Act would be properly upon the local, licensed controllers.
We find an analogy in a High Street pharmacy where one man is sole manager but is not necessarily a qualified dispenser. He may have a number of dispensers working under him and the direct responsibility for not serving the wrong pills is theirs. But they are not all called "managers". It follows that, if there were licensed transport controllers the details of their required qualification could be worked out so that, whether a controller was primarily an operating man or an engineer, there would be one standard set of requirements of efficiency in controlling. This would leave the definition of transport management within the responsibility of the professional institutes, They could hammer out the syllabuses of examinations and there might even be, under the auspices of the Institute of Transport, chartered transport managers just as there are chartered engineers and chartered accountants.
I hope my suggestion is acceptable and that the description "transport controller" is ultimately adopted. Otherwise, imagine a firm with one general manager, one works manager, one marketing manager. one research manager and 99 transport "managers"! R. J. EATON MInstT, MInstrA, AMB1M Thorpe Bay, Essex
Insurance and stolen loads
The High Court decision on the two cases of thefts of copper from vehicles of Poplar Motor Transport (Lymm) Ltd. (CM, July 261 again gives prominence to the heavy responsibilities which fall on road transport operators.
In this case the hauliers are left to pay the full claim from their customers of £9,800. A pretty hefty bill. This is a risk that every transport business runs. Poplar Motor Transport held a goods-in-transit policy designed to protect their risks in this field. It is true that they had failed to adhere to their 'warranties" under the policy. In my view, in contrast to the Holden case decision (CM, May 17) this is a much stronger case for the insurers to contest.
The judge summed up the evidence by saying: "Both men had instructions from their traffic manager that if a vehicle was left unattended after 6 p.m. it should be on secured premises."
So the drivers apparently disobeyed their instructions. How can hauliers ensure that drivers will obey instructions? If the drivers were in breach of instructions, they might well be dismissed, and in fairness it is really for them to pay for the loss. But what hope is there of that?
The haulier faces a bill big enough to bankrupt some hauliers, through the disobedience of his staff and is not protected by insurance. This is an extremely serious matter, which I should like someone to tell me the answer to.
I will throw out another problem for our back-room costing boys. What is the proper procedure for dealing with this expenditure of £9,800 in calculating the firm's vehicle costings? This is a perfectly serious question. The firm surely has to find some way of recovering this item of costs in its costings. In what way should it be treated? Over how many years? Under what heading?
RALPH CROPPER Director, Transport Counsellors Ltd., London, SE14.