B EHIND the export drive of Vauxhall Motors. Ltd., lies a
Page 34
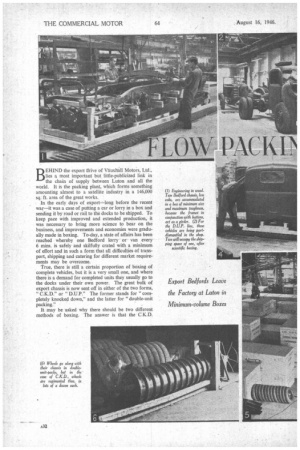
Page 35
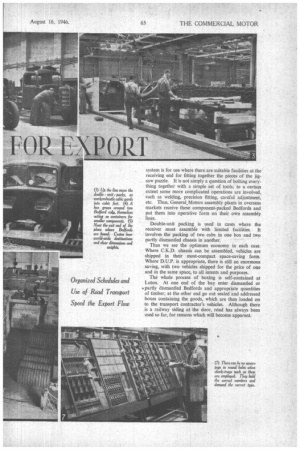
Page 36
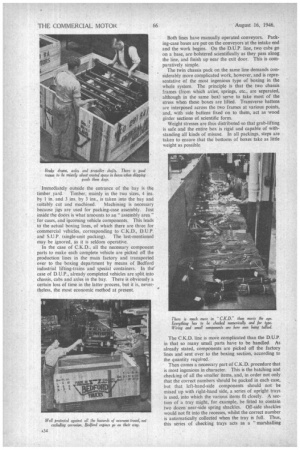
Page 39
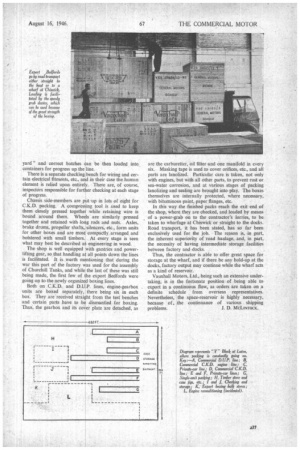
If you've noticed an error in this article please click here to report it so we can fix it.
most important but little-publicized link in the chain of supply between Luton and all the world. It is the packing plant, which forms something amounting almost to a satellite industry in a 146,000 sq ft. area of the great works.
In the early days of export—long before the recent war—it was a case of putting a car or lorry in a box and sending it by road or rail to the docks to be shipped. To keep pace with improved and extended production, it was necessary to bring more science to bear on the business, and improvements and economies were gradually made in boxing. To-day, a state of affairs has been reached whereby one Bedford lorry or van every 6 mins. is safely and skilfully crated with a minimum of effort and in such a form that all difficulties of transport, shipping and catering for different market requirements may be overcome.
True, there is still a certain proportion of boxing of complete vehicles, but it is a very small one, and where there is a demand for completed units they usually go to the docks under their own power. The great bulk of export chassis is now sent off in either of the two forms, or " D.U.P." The former stands for "completely knocked down," and the latter for "double-unit packing."
It may be asked why there should be two different methods of boxing. The answer is that the C.K.D. system is for use where there are suitable facilities at the receiving end for fitting together the pieces of the jigsaw puzzle. It is not simply a question of bolting everything together with a simple set of tools; to a certain extent some more complicated operations are involved, such as welding, precision fitting, careful adjustment, etc. Thus, General, Motors assembly plants in overseas markets receive these component-packed Bedfords and put them into operative form on their own assembly lines.
Double-unit packing is used in cases where the receiver must assemble with limited facilities. It involves the packing of two cabs in one box and two partly dismantled chassis in another.
Thus we see the optimum economy in each case. Where C.K.D. chassis can be assembled, vehicles are shipped in their most-compact space-saving form. Where D.U.P. is appropriate, there is still an enormous saving, with two vehicles shipped for the price of one and in the same space, to all intents and purposes.
The whole process of boxhig is self-contained at Luton. At one end of the bay enter dismantled or • partly dismantled Bedfords and appropriate quantities of timber; at the other end go out sealed and addressed boxes containing the goods, which are then loaded on to the transport contractor's vehicles. Although there is a railway siding at the door, road has always been used so far, for reasons which will become apparent. Immediately outside the entrance of the bay is the timber yard. Timber, mainly in the two sizes, 4 ins. by 1 in. and 3 ins. by 3 ins., is taken into the bay and suitably cut and machined. Machining is necessary because jigs are used for packing-case assembly. Just inside the doors is what amounts to an "assembly area" for cases, and incoming vehicle components. This leads to the actual boxing lines, of which there are three for commercial vehicles, corresponding to C.K.D., D.U.P.
and S.U.P. (single-unit packing). The last-mentioned may be ignored, as it is seldom operative.
In the case of C.K.D.. all the necessary component parts to make each complete vehicle are picked off the production lines in the main factory and transported over to the boxing department by means of Bedford industrial lifting-trains and special containers. In the case of D.U.P., already completed vehicles are split into chassis, cabs and axles in the bay. There is obviously a certain loss of time in the latter process, but it is, nevertheless, the most economic method at present.
Both lines have manually operated conveyors. Packing-case bases are put on the conveyors at the intake end and the work begins. On the D.U.P. line, two cabs go on a base, are bolstered scientifically as they pass along the line, and finish up near the exit door. This is comparatively simple.
The twin chassis pack on the same line demands considerably more complicated work, however, and is representative of the most ingenious type of boxing in the whole system. The principle is that the two chassis frames (from which axles, springs, etc., are separated, although in the same box) serve to take most of the stress when these boxes are lifted. Transverse battens are interposed across the two frames at various points, and, with side battens fixed on to them, act as wood girder sections of scientific form.
Weight stresses are thus distributed so that grab-lifting is safe and the entire box is rigid and capable of withstanding all kinds of misuse. In all packings, steps are taken to ensure that the bottoms of boxes take as little weight as possible.
The C.K.D. line is more complicated than the D.U.P. in that so many small parts have to be handled. As already stated, components are picked off the factory lines and sent over to the boxing section, according to the quantity required.
' Then comes a necessary part of C.K.D. procedure that is most ingenious in character. This is the batching and checking of all the smaller items, and, in order not only that the correct numbers should be packed in each case, but that left-hand-side components should not be mixed up with right-hand side, a series of upright trays is used, into which the various items fit closely. A section of a tray might, for example, be fitted to contain two dozen near-side spring shackles. Off-side shackles would not fit into the recesses, whilst the correct number is automatically collected when the tray is full. Thus, this series of checking trays acts as a "marshalling
yard" and correct batches an be then loaded into containers for progress up the line. There is a separate checkingibench for wiring and certain electrical fitments, etc., and in their case the human element is relied upon entirely. There are, of course, inspectors responsible for further checking at each stage of progress.
Chassis side-members are put 'up in lots of eight for C.K.D. packing. A compressing tool is used to keep them closely pressed together while retaining wire is bound around them. Wheels are similarly pressed together and retained with long rods and nuts. Axles, brake drums, propeller shafts, silencers, etc., form units for other boxes and are most compactly arranged and bolstered with small timbers. At every stage is seen what may best be described at engineering in wood.
The shop is well equipped with gantries and powerlifting gear, so that handling at all points down the lines is facilitated. It is worth mentioning that during the war this part of the factory was used for the assembly of Churchill Tanks, and while the last of these was still being made, the first few of the export Bedfords were going on to the newly organized boxing lines.
Both on C.K.D. and D.U.P. lines, engine-gearbox units are boxed separately, there being six in each box. They are received straight from the test benches and certain parts have to be dismantled for boxing. Thus, the gearbox and its cover plate are detached, as
are the carburetter, oil filter and one manifold in every six. Masking tape is used to cover orifices, etc., and all parts are lanolized. Particular care is taken, not only with engines, but with all other parts, to prevent rust or sea-water corrosion, and at various stages of packing lanolizing and sealing are brought into play. The boxes themselves are internally protected, where necessary, with bituminous paint, paper flanges, etc.
In this way the finished packs reach the exit end of the shop, where they are checked, and loaded by means of a power-grab on to the contractor's lorries, to be taken to wharfage at Chiswick or straight to the docks. Road transport, it has been stated, has so far been exclusively used for the job. The reason is, in part, the inherent superiority of road haulage, and, in part. the necessity of having intermediate storage facilities between factory and docks.
Thus, the contractor is able to offer great space for storage at the wharf, and if there be any hold-up at the docks, factory output may continue while the wharf acts as a kind of reservoir.
Vauxhall Motors, Ltd., being such an extensive undertaking, is in the fortunate position of being able to export in a continuous flow, as orders are taken on a definite schedule from overseas representatives. Nevertheless, the space-reservoir is highly necessary, because of. the continuance of various shipping
problems. J. D. MCLINTOCK.