Engineering News
Page 18
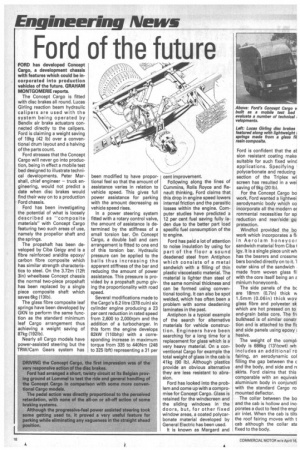
If you've noticed an error in this article please click here to report it so we can fix it.
Ford of the future
FORD has developed Concept Cargo, a development chassis with features which could be incorporated into production vehicles of the future. GRAHAM MONTGOMERIE reports.
The Concept Cargo is fitted with disc brakes all round. Lucas Girling reaction beam hydraulic calipers are used with the system being operated by Bendix air brake actuators connected directly to the calipers. Ford is claiming a weight saving of 19kg (42 lb) over a conventional drum layout and a halving of the parts count.
Ford stresses that the Concept Cargo will never go into production, being in effect a mobile test bed designed to illustrate technical developments. Peter Marshall, chief engineer — truck engineering, would not predict a date when disc brakes would find their way on to a production Ford chassis.
Ford has been investigating the potential of what is loosely described as "composite materials" with Concept Cargo featuring two such areas of use, namely the propellor shaft and the springs.
The propshaft has been developed by Ciba Geigy and is a fibre reinforced araldite epoxy/ carbon fibre composite which has similar strength characteristics to steel. On the 3.72m (12ft 3in) wheelbase Concept chassis the normal two-piece propshaft has been replaced by a single piece composite shaft which saves 6kg (131b).
The glass fibre composite leaf springs have been developed by GKN to perform the same function as the standard minimum leaf Cargo arrangement thus achieving a weight saving of 87kg (1921b).
Nearly all Cargo models have power-assisted steering but the TRW/Cam Gears system has
been modified to have proportional feel so that the amount of assistance varies in relation to vehicle speed. This gives full power assistance for parking with the amount decreasing as vehicle speed rises.
In a power steering system fitted with a rotary control valve, the amount of assistance is determined by the stiffness of a small torsion bar. On Concept Cargo, a double ball and cam arrangement is fitted to one end of this torsion bar. Hydraulic pressure can be applied to the balls thus increasing the apparent stiffness of the bar and reducing the amount of power assistance. This pressure is provided by a propshaft pump giving the proportionality with road speed.
Several modifications made to the Cargo's 6.2 litre (378 cuin) six cylinder engine producing a 23 per cent reduction in rated speed from 2,600 to 2,000rpm and the addition of a turbocharger. In this form the engine develops 82kW (110bhp) with a corresponding increase in maximum torque from 335 to 440Nrn (248 to 325 lbft) representing a 31 per _ cent improvement.
Following along the lines of Cummins, Rolls Royce and Renault thinking, Ford claims that this drop in engine speed lowers internal friction and the parasitic losses within the engine. Computer studies have predicted a 12 per cent fuel saving fully laden due to the better part load specific fuel consumption of the tc engine.
Ford has paid a lot of attention to noise insulation by using for part of the floor a sound deadened steel from Antiphon which consists of a metal sandwich with a filling of thin plastic viscoelastic material. The material is lighter than steel of the same nominal thickness and can be formed using conventional tooling. It can also be spot welded, which has often been a problem with some deadening laminates in the past.
Antiphon is a typical example of the search for alternative materials for vehicle construction. Engineers have been searching for a long time for a replacement for glass which is a very heavy material. On a conventional Cargo for example the total weight of glass in the cab is 41kg (90 lb). Although plastics provide an obvious alternative they are less resistant to abrasion.
Ford has looked into the problem and come up with a compromise for Concept Cargo. Glass is retained for the windscreen and the sliding windows in the doors, but, for other fixed window areas, a coated polycarbonate material developed by General Electric has been used.
It is known as Margard and Ford is confident that the at sion resistant coating make suitable for such fixed wind applications. Specifying polycarbonate and reducing section of the Triplex wi screen has resulted in a wei saving of 9kg (20 lb).
For the Concept Cargo bo work. Ford wanted a lightwei aerodynamic body which co incorporate all the modern er ronmental necessities for sp reduction and rear/side gu protection.
Windfoil provided the bo work which incorporates a fl in Aerolam honeycor sandwich material from Ciba I igy. It is a single piece unit wh has the bearers and crossme bers bonded directly on to it. 1 outer skins of the sandwich made from woven glass fil with the core itself being an t• minium honeycomb.
The side panels of the bc are 18mm (0.7in) thick vi 1.5mm (0.06in) thick way glass fibre and polyester sk which are hot pressed on to end-grain balsa core. The fn bulkhead is of similar constr tion and is attached to the fir and side panels using epoxy hesive.
The weight of the compll body is 686kg (131/2cwt) wh includes an additional ro fairing, an aerodynamic col filling the gap between the e and the body, and side and 1'1 skirts. Ford claims that this comparable with an equival( aluminium body in conjuncti with the standard Cargo ro mounted deflector.
The collar between the bo and the cab is hollow and inc porates a duct to feed the engi air inlet. When the cab is tilt
the roof fairing moves with t cab although the collar sta fixed to the body.