Cory match bodyswap to new tail-lift
Page 40
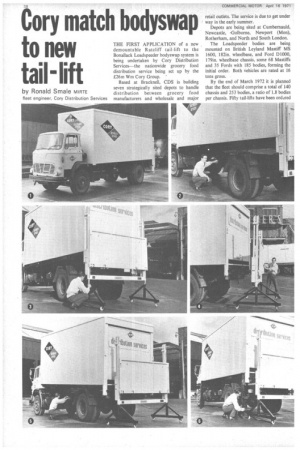
Page 41
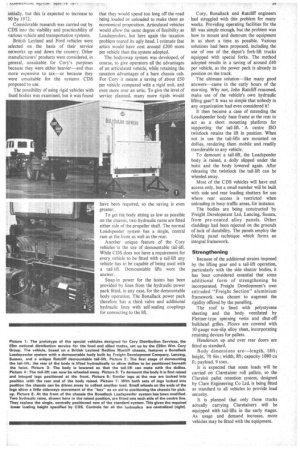
If you've noticed an error in this article please click here to report it so we can fix it.
by Ronald Smale MIRTE
fleet engineer, Cory Distribution Services
THE FIRST APPLICATION of a new demountable Rateliff tail-lift to the BonaHack Loadspeeder bodyswap system is being undertaken by Cory Distribution Services—the nationwide grocery food distribution service being set up by the £.26m Wm Cory Group. '
Based at Bracknell, CDS is building seven strategically sited depots to handle distribution between grocery food manufacturers and wholesale and major retail outlets. The service is due to get under way in the early summer.
Depots are being sited at Cumbemauld, Newcastle, -Golbome, Newport (Mon), Rotherham, and North and South London.
The Loadspeeder bodies are being mounted on British Leyland Mastiff MS 1600, 182in. wheelbase, and Ford D1000, 179in. wheelbase chassis, some 68 Mastiffs and 35 Fords with 185 bodies, forming the initial order. Both vehicles are rated at 16 tons gross.
By the end of March 1972 it is planned that the fleet should comprise a total of 140 chassis and 253 bodies, a ratio of 1.8 bodies per chassis. Fifty tail-lifts have been ordcred initially, but this is expected to increase to 90 by 1972.
Considerable research was carried out by CDS into the viability and practicability of various vehicle and transportation systems.
British Leyland and Ford vehicles were selected on the basis of their service networks up and down the country. Other manufacturers' products were considered, in general, unsuitable for Cory's purposes because they were either heavier—and thus more expensive to tax—or because they were unsuitable for the systems CDS proposed to use.
The possibility of using rigid vehicles with fixed bodies was examined, but it was found that they would spend too long off the road being loaded or unloaded to make them an economical proposition. Articulated vehicles would allow the same degree of flexibility as Loadspeeders, but here again the taxation problem reared its ugly head. I estimate that artics would have cost around £200 more per vehicle than the system adopted.
The bodyswap system was developed, of course, to give operators all the advantages of an articulated vehicle, while retaining the taxation advantages of a bare chassis cab. For Cory it means a saving of about £50 per vehicle compared with a rigid unit, and even more over an artic. To give the level of service planned, many more rigids would have been required, so the saving is even greater.
To get the body sitting as low as possible on the chassis, two hydraulic rams are fitted either side of the propeller shaft. The normal Loadspeeder system has a single, central ram at the front as well as the rear.
Another unique feature of the Cory vehicles is the use of demountable tail-lift. While CDS does not have a requirement for every vehicle to be fitted with a tail-lift any vehicle has to be capable of being used with a tail-lift. Demountable lifts were the answer.
Snap-in power for the hoists has been provided by lines from the hydraulic power pack fitted, in any case, for the demountable body operation. The Bonallack power pack therefore has a third valve and additional hydraulic lines with self-sealing couplings for connecting to the lift. Cory, Bonallack and Ratcliff engineers had struggled with this problem for many weeks. Providing operating'facilities for the lift was simple enough, but the problem was how to mount and demount the equipment in as short a time as possible. Various solutions had been proposed, including the use of one of the depot's fork-lift trucks equipped with special forks. The method adopted results in a saving of around £40 per vehicle, as the power pack is already in position on the truck.
The ultimate solution like many good answers—came in the early hours of the morning. Why not, John Ratcliff reasoned, make use of the vehicle's own hydraulic lifting gear? It was so simple that nobody in any organization had even considered it!
It then became a case of extending the Loadspeeder body base frame at the rear to act as a short mounting platform for supporting the' tail-lift. A centre ISO twistlock retains the lift in position. When not in use the tail-lifts are mounted on dollies, rendering them mobile and readily transferable to any vehicle.
To demount a tail-lift, the Loadspeeder body is raised, a dolly slipped under the hoist and the body lowered again. After releasing the twistlock the tail-lift can be wheeled. away.
Most of the CDS vehicles will have end access only, but a small number will be built with side and rear loading shutters for use where rear access is restricted when unloading in busy traffic areas, for instance.
The bodies are being constructed by Freight Development Ltd, Lancing, Sussex, from pre-coated alloy panels. Other claddings had been rejected on the grounds of lack of durability. The panels employ the folding panel technique which forms an integral framework.
Strengthening Because of the additional strains imposed by the lifting gear and a tail-lift operation, particularly with the side shutter bodies, it has been considered essential that some additional form of strengthening be incorporated. Freight Development's own extruded "Freight Section" aluminium framework was chosen to augment the rigidity offered by the panelling.
The roof is lined with polystyrene sheeting and the body ventilated by Flettner-type spinning vents and shut-off bulkhead grilles. Floors are covered with 10-gauge non-slip alloy sheet, incorporating retaining devices for pallets.
Henderson up and over rear doors are fitted as standard.
Body dimensions are—length, 18ft; height, 7ft fin.; width, 8ft: capacity 1080 cu ft; payload, 9 tons.
It is expected that some loads will be carried on Claretainer roll pallets, so the Clarelok pallet retention system, designed by Clare Engineering Co Ltd, is being fitted as standard to all vehicles to provide load security.
It is planned that only those trucks actually carrying Claretainers will be equipped with tail-lifts in the early stages. As usage and demand increase, more vehicles may be fitted with the equipment.