Coaching dreams
Page 58
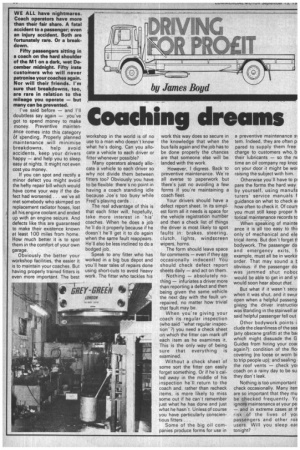
If you've noticed an error in this article please click here to report it so we can fix it.
by James Boyd
WE ALL have nightmares. Coach operators have more than their fair share. A fatal accident to a passenger; even an injury accident. Both are fortunately rare. Or a breakdown.
Fifty passengers sitting in a coach on the hard shoulder of the Ml on a dark, wet December midnight. Fifty irate customers who will never patronise your coaches again. Nor will their friends. I'm sure that breakdowns, too, are rare in relation to the mileage you operate — but many can be prevented.
I've said before — and I'll doubtless say again — you've got to spend money to make money. Preventive maintenance comes into this category of spending. Properly planned maintenance will minimise breakdowns, help avoid accidents, keep your drivers happy — and help you to sleep easy at nights. It might not even cost you money.
If you can spot and rectify a minor defect you might avoid the hefty repair bill which would have come your way if the de fect had worsened . . . we've all met somebody who skimped on replacement radiator hoses, lost all his engine coolant and ended up with an engine seizure. And defects like this are guaranteed to make their existence known at least 100 miles from home.
How much better it is to spot them in the comfort of your own garage.
Obviously the better your workshop facilities, the easier it is to maintain your coaches. But having properly trained fitters is even more important. The best wolkshop in the world is of no use to a man who doesn't know what he's doing. Can you allocate a vehicle to each driver or fitter whenever possible?
Many operators already allocate a vehicle to each driver so why not divide them between fitters too? Obviously you have to be flexible: there's no point in having a coach standing idle because Joe's too busy while Fred's playing cards • .
The real advantage of this is that each fitter will, hopefully, take more interest in 'his' coaches. When he does a job he'll do it properly because if he doesn't he'll get it to do again when the same fault reappears. He'll also be less inclined to do a bodged job.
Speak to any fitter who has worked in a big bus depot and you'll hear tales of repairs done using short-cuts to avoid heavy work. The fitter who tackles his work this way does so secure in the knowledge that when the bus fails again and the job has to be done properly the chances are that someone else will be landed with the work.
However, I digress. Back to preventive maintenance. We're all averse to paperwork but there's just no avoiding a few forms if you're maintaining a coach fleet.
Your drivers should have a defect report sheet. In its simplest form all it needs is space for the vehicle registration number and then a check list of things the driver is most likely to spot faults in brakes, steering, clutch, lights, windscreen wipers, horns.
The form should leave space for comments — even if they are occasionally indecent! You should check defect report sheets daily — and act on them. Nothing — absolutely nothing — infuriates a driver more than reporting a defect and then being given the same vehicle the next day with the fault unrepaired, no matter how trivial that fault may be.
When you're giving your coach its regular inspection (who said "what regular inspec tion"?) you need a check sheet on which the fitter can mark off each item as he examines it. This is the only way of being sure that everything is examined, Without a check sheet 'of some sort the fitter can easily forget something. Or if he's cal led away in the middle of his inspection he'll return to the coach and, rather than recheck items, is more likely to miss some out if he can't remember just what he has done and just what he hasn't. Unless of course you have particularly conscientious fitters .
Some of the big oil companies produce forms for use in a preventive maintenance s■ tern. Indeed, they are often p pared to supply them free charge to customers who. b their lubricants — so the ri( time an oil company rep knoc on your door it might be wo: raising the subject with him.
Otherwise you'll have to pi pare the forms the hard way by yourself, using manufa turers' service manuals f guidance on what to check ai how often to check it. Of courE you must still keep proper h torical maintenance records tc When speaking of mainte ance it is all too easy to thii only of mechanical arid ele trical items. But don't forget ti bodywork. The passenger do and emergency exits, fi example, must all be in workir order. That may sound a t obvious: if the passenger do was jammed shut noboc would be able to get in and y: would soon hear about that.
But what if it wasn't secu when it was shut, and it swur open when a helpful passeng giving the driver instructioi was standing in the stairwell ar said helpful passenger fell out Other bodywork points i clude the cleanliness of the sea (any obscene grafitti at the bai which might dissuade the G Guides from hiring your coac again?); condition of the floi covering (no loose or worn bi to trip people up); and sealing the roof vents — check yoi coach on a rainy day to be su they don't leak.
Nothing is too unimportant check occasionally. Many :ten are so important that they mu be checked frequently. Yc ignore maintenance at your pe — and in extreme cases at tt risk of the lives of yoi passengers and other roa users. Will you sleep eaf. tonight?