Cement Goes in Bulk
Page 48
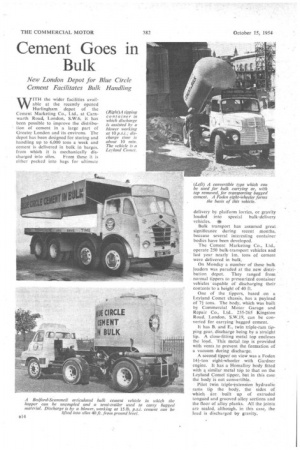
Page 49
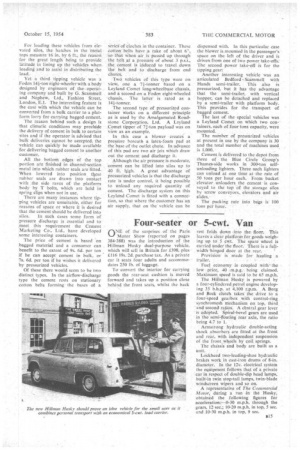
If you've noticed an error in this article please click here to report it so we can fix it.
New London Depot for Blue Circle Cement Facilitates Bulk Handling
WITH the wider facilities available at the recently opened Hurlingham depot of the Cement Marketing Co., Ltd., at Camwarth Road, London, S.W.6, it has been possible to improve the distribution of cement in a large part of Greater London and its environs. The depot has been designed for storing and handling up to 6,000 tons a week and cement is delivered in bulk in barges. from which it is mechanically dis
charged into silos. From these it is eiher packed into bags for ultimate
delivery by platform lorries, or gravity loaded into special bulk-delivery vehicles. •
Bulk transport has assumed great significance during recent months, because several interesting container bodies have been developed.
The Cement Marketing Co., Ltd., operate 250 bulk-transport vehicles and last year nearly Im. tons of cement were delivered in hulk.
On Monday a number of these bulk loaders was paraded at the new distribution depot. They ranged from normal tippers to pressurized container vehicles capable of discharging their contentslo a height of 40 ft.
One of the tippers, based on a Leyland Comet chassis, has a payload of 7+ tons. The body, which was built by Commercial Motor Garage and Repair Co., Ltd., 255-265 Kingston Road. London, S.W.19, can be converted for carrying bagged cement.
It has B. and E., twin triple-ram tipping gear, discharge being by a straight tip. A close-fitting metal top encloses the load.. This metal top is provided with vents to prevent the formation of a vacuum during discharge.
A second tipper on view was a Foden 14+-ton eight-wheeler with Gardner engine. It has a Homalloy body fitted with a similar metal top to that on the Leyland Comet tipper, but in this case the body is not convertible.
Pilot twin triple-extension hydraulic rams tip the body, the sides of which are built up of extruded tongued and grooved alloy sections and the floor of alloy planks. All the joints are sealed, although. in this case, the load is discharged by gravity.
For loading these vehicles from elevated silos, the hatches in the Metal tops measure 16 in. by 6 ft., the reason for the great length being to provide latitude in lining up the -vehicles when loading and to assist in distributing the load.
Yet a third tipping vehicle was a Foden 144-ton eight-wheeler with a body designed by engineers of the operating company and built by G. Scammell .and Nephew, Ltd., Fashion Street, London, E.1. The interesting feature is the ease with which the vehicle can be converted from a bulk carrier to a platform lorry for carrying bagged•cernent.
The reason behind such a design is that climatic conditions may preeltide the delivery of cement in bulk to certain sites and if the operator is advised that bulk deliveries cannot be accepted. the vehicle can quickly be made available for delivering bagged cement to another customer.
All the bottom edges of the top portion are finished in channel-section metal into which rubber seals are.fitted. When lowered into position. these rubber seals are drawn into contact with the side raves of the platform body by T bolts, which are held in spring clips when not in use.
There are many instances where tipping vehicles are unsuitable, either for reasons of space or where it is desired that the cement should be delivered into
silos. In such cases some form of pressure discharge is essential and to meet this requirement the Cement Marketing Co., Ltd., have developed some interesting containers.
The price of cement is based on bagged material and a consumer can benefit to the extent of 9s. 6d. per ton if he can accept cement in bulk, or 7s. 6d. per ton if he wishes it delivered by pressurized vehicles.
Of these there would seem to be two distinct types. In the airflow-discharge type the cement rests on stationary cotton belts forming . the bases of a series of cloches in the container. These cotton belts have a rake of about 6°, so that When air is passed up through the belt at a pressure of about 3 p.s.i., the cement is induced to travel down the belt and to discharge from end chutes.
Two vehicles of this type were on view, one a Ti-tonner based on a Leyland Comet long-wheelbase chassis, and a second on a Foden eight-wheeled 'chassis. The latter is rated as a 141-tonner.
The second type of pressurized container Works on a different principle as is used by the Amalgamated Roadstone Corporation, Ltd. A Leyland Comet tipper of 71-ton payload was on view as an example. In this case a blower creates' a pressure beneath a latex-foam pad at the 'base of the outlet chute. In advance of this pad are two air jets which draw out the cement and discharge it.
• Although the air pressure is moderate, cement can be lifted into silos up to 40 ft. ligh. A great advantage of pressurized vehicles is that the discharge rate is under control; it being possible to unload any required quantity of cement. The discharge system on this Leyland Comet is fitted with a connection, so that where the customer has an air supply, that on the vehicle can be
dispensed with. In this particular case the blower is mounted in the passenger's space on the left of the driver and is driven from one of two power take-offs. The second power take-off is for the tipping gear.
Another interesting vehicle was an articulated Bedford Scammell with Hands semi-trailer. This also is pressurized, but it has the advantage that the semi-trailer, with vertical hopper, can be detached and replaced by a semi-trailer with platform body. This provides for the transport of bagged cement.
The last of the special vehicles was a Leyland Comet on which two containers, each of four tons capacity, were mounted.
The number of pressurized vehicles at present in use by the company is 30 and the total number of machines used is 1.000.
Cement is delivered to the depot from three of the Blue Circle Group's Thames-side works in 300,ton selfunloading lighters. Three such lighters can unload at one time at the rate of 50 tons per hour each. From bucket elevator, unloaders the cement is conveyed to the top of the storage silos by screw conveyors, elevators and air slides.
The packing rate into bags is 100 tons per hour.