HAUL MIRRORS
Page 92
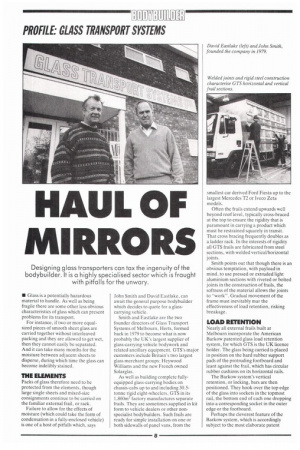
Page 93
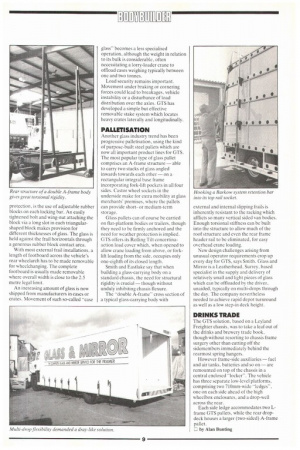
If you've noticed an error in this article please click here to report it so we can fix it.
Designing glass transporters can tax the ingenuity of the bodybuilder. It is a highly specialised sector which is fraught with pitfalls for the unwary.
• Glass is a potentially hazardous material to handle. As well as being fragile there are some other less obvious characteristics of glass which can present problems for its transport.
For instance, if two or more equal sized pieces of smooth sheet glass are carried together without interleaved packing and they are allowed to get wet, then they cannot easily be separated. And it can take many months for the moisture between adjacent sheets to disperse, during which time the glass can become indelibly stained.
THE ELEMENTS
Packs of glass therefore need to be protected from the elements, though large single sheets and mixed-size consignments continue to he carried on the familiar external frail, or rack.
Failure to allow for the effects of moisture (which could take the form of condensation in a fully-enclosed vehicle) is one of a host of pitfalls which, says John Smith and David Eastlake, can await the general purpose bodybuilder which decides to quote for a glasscarrying vehicle.
Smith and Eastlake are the two founder directors of Glass Transport Systems of Melbourn, Herts, formed back in 1979 to become what is now probably the UK's largest supplier of glass-carrying vehicle bodywork and related ancillary equipment. GTS's major customers include Britain's two largest glass merchant groups: Heywood Williams and the new French owned Solarglas.
As well as building complete fullyequipped glass-carrying bodies on chassis-cabs up to and including 30.5tonne rigid eight-wheelers. GTS in its 1,860m2 factory manufactures separate trails. They are sometimes supplied in kit form to vehicle dealers or other nonspecialist bodybuilders. Such frails are ready for simple installation on one or both sidewalls of panel vans, from the
smallest car derived Ford Fiesta up to the largest Mercedes T2 or Iveco Zeta models.
Often the trails extend upwards well beyond roof level, typically cross-braced at the top to ensure the rigidity that is paramount in carrying a product which must be restrained squarely in transit. That cross bracing frequently doubles as a ladder rack. In the interests of rigidity all GTS frails are fabricated from steel sections, with welded verticallhorizontal joints.
Smith points out that though there is an obvious temptation, with payload in mind, to use pressed or extruded light aluminium sections with riveted or bolted joints in the construction of frails, the softness of the material allows the joints to -work". Gradual movement of the frame must inevitably mar the effectiveness of load retention, risking breakage.
LOAD RETENTION
Nearly all external trails built at Melbourn incorporate the American Barkow patented glass load retention system, for which GTS is the UK licence holder. The glass being carried is placed in position on the hard rubber support pads of the protruding footboard and leant against the frail, which has circular rubber cushions on its horizontal rails.
The Barkow system's vertical retention, or locking, bars are then positioned. They hook over the top edge of the glass into sockets in the topmost rail, the bottom end of each one dropping into a corresponding socket in the outer edge or the footboard.
Perhaps the cleverest feature of the Barkow system, which is accordingly subject to the most elaborate patent protection, is the use of adjustable rubber blocks on each locking bar. An easily tightened bolt and wing-nut attaching the block via a long slot in each triangularshaped block makes provision for different thicknesses of glass. The glass is held against the frail horizontals through a generous rubber block contact area.
With most external frail installations, a length of footboard across the vehicle's rear wheelarch has to be made removable for whecichanging. The complete footboard is usually made removable where overall width is close to the 2.5 metre legal limit.
An increasing amount of glass is now shipped from manufacturers in cases or crates. Movement of such so-called -case
glass" becomes a less specialised operation, although the weight in relation to its bulk is considerable, often necessitating a lorry-loader crane to offload cases weighing typically between one and two tonnes.
Load security remains important. Movement under braking or cornering forces could lead to breakages, vehicle instability or a disturbance of load distribution over the axles. GTS has developed a simple but effective removable stake system which locates heavy crates laterally and longitudinally.
PALLETISATION
Another glass industry trend has been progressive palletisation, using the kind of purpose-built steel pallets which are now all important product lines for GTS. The most popular type of glass pallet comprises an A-frame structure — able to carry two stacks of glass angled inwards towards each other — on a rectangular integral base frame incorporating fork-lift pockets in all four sides. Castor wheel sockets in the underside make for extra mobility at glass merchants' premises, where the pallets can provide shortor medium-term storage.
Glass pallets can of course be carried on flat-platform bodies or trailers, though they need to be firmly anchored and the need for weather protection is implied. GTS offers its Rolling Tilt concertinaaction load cover which, when opened to allow crane loading from above, or forklift loading from the side. occupies only one-eighth of its closed length.
Smith and Eastlake say that when building a glass-carrying body on a standard chassis, the need for structural rigidity is crucial — though without unduly inhibiting chassis flexure.
The "double A-frame" cross section of a typical glass-carrying body with external and internal slipping frails is inherently resistant to the racking which afflicts so many vertical sided van bodies. Enough torsional stiffness can be built into the structure to allow much of the roof structure and even the rear frame header rail to be eliminated, for easy overhead crane loading.
New design challenges arising from unusual operator requirements crop up every day for GTS, says Smith. Glass and Mirror is a Leatherhead, Surrey, based specialist in the supply and delivery of relatively small and light pieces of glass which can be offloaded by the driver, unaided, typically on multi-drops through the day. The company nevertheless needed to achieve rapid depot turnround as well as a low step-in deck height.
DRINKS TRADE
The GTS solution, based on a Leyland Freighter chassis, was to take a leaf out of the drinks and brewery trade book. though without resorting to chassis frame surgery other than cutting off the sidemcmbers immediately behind the rearmost spring hangers.
However frame-side auxiliaries— fuel and air tanks, batteries and so on — are remounted on top of the chassis in a central enclosed -locker". The vehicle has three separate low-level platforms, comprising two 710mm-wide "ledges", one on each side ahead of the high wheelbox enclosures, and a drop-well across the rear.
Each side ledge accommodates two Lframe GTS pallets, while the rear dropdeck houses a larger (two-sided) A-frame pallet.
0 by Alan Bunting