The relentless stop-start demands of express delivery work takes a
Page 38
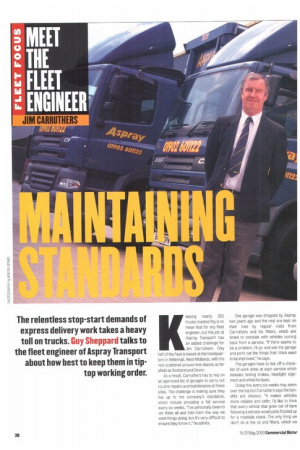
Page 39
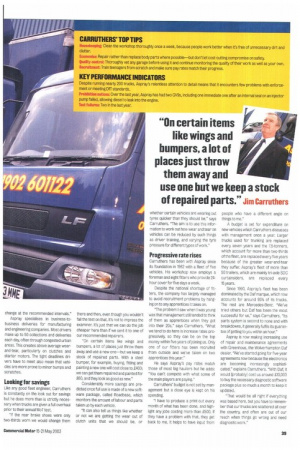
If you've noticed an error in this article please click here to report it so we can fix it.
heavy toll on trucks. Guy Sheppard talks to the fleet engineer of Aspray Transport about how best to keep them in tiptop working order.
Keeping nearly 200 trucks roadworthy is no mean feat for any fleet engineer, but the job at Aspray Transport has an added challenge for Jim Carruthers. Only haft' of the fleet is based at the headquarters in Willenhall, West Midlands, with the rest scattered around nine depots as far afield as Scotland and Devon.
As a result, Carruthers has to rely on an approved list of garages to carry out routine repairs and maintenance at these sites. The challenge is making sure they live up to the company's standards, which include providing a full service every six weeks. "I've personally been to vet them all and told them the way we want things doing, but it's very difficult to ensure they follow it," he admits. One garage was dropped by Aspray two years ago and the rest are kept on their toes by regular visits from Carruthers and his fitters, which are timed to coincide with vehicles coming back from a service. "If there seems to be a problem, I'll go and see the garage and point out the things that I think need to be improved," he says.
The garages have to tick off a checklist of work done at each service which includes testing brakes, headlight alignment and wheel torques.
Doing this every six weeks may seem over the top but Carruthers says the benefits are obvious. "It makes vehicles more reliable and safer. I'd like to think that every vehicle that goes out of here following a service would pass if pulled up for a roadside check. The only thing we don't do is the oil and filters, which we change at the recommended intervals."
Aspray specialises in business-tobusiness deliveries for manufacturing and engineering companies. Most drivers make up to 50 collections and deliveries each day, often through congested urban areas. This creates above average wearand-tear, particularly on clutches and starter motors. The tight deadlines drivers have to meet also mean that vehicles are more prone to minor bumps and scratches.
Looking for savings
Like any good fleet engineer, Carruthers is constantly on the look out for savings but he does more than is strictly necessary when trucks are given a full overhaul prior to their annual MoT test.
"If the rear brake shoes were only two-thirds worn we would change them there and then, even though you wouldn't fail the test on that. It's not to impress the examiner. It's just that we can do the job cheaper here than if we sent it to one of our recommended repairers.
"On certain items like wings and bumpers, a lot of places just throw them away and use a new one—but we keep a stock of repaired parts. With a steel bumper, for example, buying, fitting and painting a new one will cost close to £400; we can get them repaired and painted for £60, and they look as good as new."
Considerably more savings are predicted once full use is made of a new software package, called Roadbase, which monitors the amount of labour and parts taken up by each vehicle.
"It can also tell us things like whether or not we are getting the wear out of clutch units that we should be, or whether certain vehicles are wearing out tyres quicker than they should be," says Carruthers. "The aim is to use this information to work out how wear and tear on vehicles can be reduced by such things as driver training, and varying the tyre pressure for different types of work."
Progressive rate rises
Carruthers has been with Aspray since its foundation in 1982 with a fleet of five vehicles. His workshop now employs a foreman and eight fitters who provide 24hour cover for five days a week, Despite the national shortage of fitters, the company has largely managed to avoid recruitment problems by hanging on to any apprentices it takes on.
"The problem I saw when I was young was that management still tended to think of them as apprentices when they got into their 20s," says Carruthers. 'What we tend to do here is increase rates progressively, so they can be on the top money within five years ofjoining us. Only one of our fitters has been recruited from outside and we've taken on two apprentices this year."
He says Aspray's pay rates match those of most big hauliers but he adds: "You can't compete with what some of the main players are paying."
Carruthers' budget is not set by management but a close eye is kept on his spending.
"I have to produce a print-out every month of what has been done, and highlight any jobs costing more than £500. If they have a problem with that, they get back to me. It helps to have input from people who have a different angle on things to me."
A budget is set for expenditure on new vehicles which Carruthers discusses with management once a year. Larger trucks used for trucking are replaced every seven years and the 7.5-tonners, which account for more than two-thirds of the fleet, are replaced every five years because of the greater wear-and-tear they suffer. Aspray's fleet of more than 50 trailers, which are mainly tri-axle SDC curtainsiders, are replaced every 15 years.
Since 1990, Aspray's fleet has been dominated by the Daf marque, which now accounts for around 95% of its trucks. The rest are Mercedes-Benz. "We've tried others but Daf has been the most successful for us," says Carruthers. "Its parts system is second to none and with breakdowns, it generally fulfils its guarantee of getting to you within an hour."
Aspray is now making increasing use of repair and maintenance agreements with Greenhous, the Wolverhampton Daf dealer. 'We've started going for five-year agreements now because the electronics are becoming increasingly sophisticated," explains Carruthers. "With Daf, it would [probably] cost us around £10,000 to buy the necessary diagnostic software package plus so much a month to keep it updated.
"That would be all right if everything was based here, but you have to remember that our trucks are scattered all over the country, and often are out of our reach when things go wrong and need diagnostic work."