D or hauliers running
Page 32
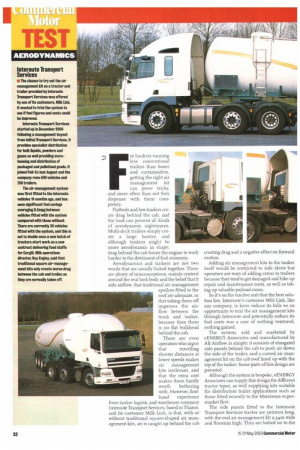
Page 33
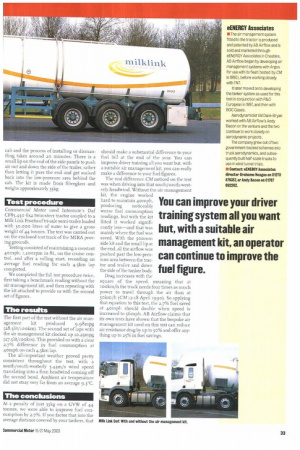
If you've noticed an error in this article please click here to report it so we can fix it.
less conventional trailers than boxes and curtainsiders, getting the right air management kit can prove tricky, and more often than not they dispense with them com pletely.
Flatbeds and low-loaders create drag behind the cab, and the load can present all kinds of aerodynamic nightmares. Multi-deck trailers simply create a large barrier, and although tankers might be more aerodynamic in shape, drag behind the cab forces the engine to work harder to the detriment of fuel economy.
Aerodynamics and tankers are not two words that are usually linked together. There are plenty of misconceptions, mainly centred around the oval tank body and the belief that it aids airflow, that traditional air management spoilers fitted to the roof are adequate, or that taking them off improves the airflow between the truck and tanker, because then there is no flat bulkhead behind the cab.
There are even operators who argue that travelling shorter distances at lower speeds makes air management kits irrelevant, and that the extra cost makes them hardly worth bothering with. However, firsthand experience from tanker logistic and warehouse company Interoute Transport Services, based in Thame, and its customer Milk Link, is that, with or without traditional square-shaped air man agement kits, air is caught up behind the cab creating drag and a negative effect on forward motion.
Adding air management kits to the tanker itself would be restricted to side skirts but operators are wary of adding extras to trailers because they tend to get damaged and hike up repair and maintenance costs, as well as taking up valuable payload room, So it's on the tractive unit that the best solution lies. Interoute's customer Milk Link, like any company, is keen reduce its bills so an opportunity to trial the air management kits through Interoute and potentially reduce its fuel costs was a case of nothing ventured, nothing gained.
The system, sold and marketed by eENERGY Associates and manufactured by AB Airflow, is simple; it consists of elongated side panels behind the cab to push air down the side of the trailer, and a curved air management kit on the cab roof lined up with the top of the tanker. Some parts of this design are patented.
Although the system is bespoke, eENERGY Associates can supply this design for different tractor types, as well supplying kits suitable for distribution trailer applications such as those fitted recently to the Morrisons supermarket fleet.
The side panels fitted to the Interoute Transport Services tractor are 5 oomm long, with the oval air management kit 2.34m wide and 800mm high. They are bolted on to the
cab and the process of installing or dismantling takes around 20 minutes. There is a small lip on the end of the side panels to push air out and down the side of the trailer, rather than letting it pass the end and get sucked back into the low-pressure area behind the cab. The kit is made from fibreglass and weighs approximately 35kg.
Test procedure
Commercial Motor used lnteroute's Daf CF85.43o 6x2 twin-steer tractor coupled to a Milk Link. Fruehauf tri-axle semi-trailer loaded with 30,000 litres of water to give a gross weight of 44 tonnes. The test was carried out on the enclosed test track of the MIRA proving grounds.
Testing consisted of maintaining a constant 40mph, 1,200rpm in 8L, on the cruise control, and after a rolling start, recording an average fuel reading for each 4.5Iuri lap completed.
We completed the full test procedure twice, first taking a benchmark reading without the air management kit, and then repeating with the kit attached to provide us with the second set of figures.
The results
The first part of the test without the air management kit produced 9.98mpg (28.3Iit/iookm). The second set of laps with the air management kit clocked up io.25mpg (27.51it/rookm). This provided us with a clear 2.7% difference in fuel consumption at 40mph on each 45km lap.
The all-important weather proved pretty consistent throughout the test, with a south/south-westerly 5.4310 wind speed translating into a firm headwind coming off the second bend. Ambient air temperature did not stray very far from an average 9.3°C.
The conclusions At a penalty of just 35kg on a GVW of 44 tonnes, we were able to improve fuel consumption by 2.7%. If you factor that into the average distance covered by your tankers, that should make a substantial difference to your fuel bill at the end of the year. You can improve driver training all you want but, with a suitable air management kit, you can really make a difference to your fuel figures.
The real difference CM noticed on the test was when driving into that south/south-westerly headwind. Without the air management kit, the engine worked hard to maintain 40mph, producing noticeably worse fuel consumption readings, but with the kit fitted it worked significantly less—and that was mainly where the fuel was saved. With the 500mm side kit and the small lip at the end, all the airflow was pushed past the low-pressure area between the tractor and trailer and down the side of the tanker body.
Drag increases with the square of the speed, meaning that at tookm/h the truck needs four times as much power to travel through the air than at 50km/h (CM 12-18 April t990). So applying that equation to this test, the 2.7% fuel saved at 40mph should double when speed is increased to 6mph. AB Airflow claims that its own tests have shown that the bespoke air management kit used on this test can reduce air resistance drag by up to 50% and offer anything up to 25% in fuel savings.
fuel figure.