MANUAL LABOUR
Page 54
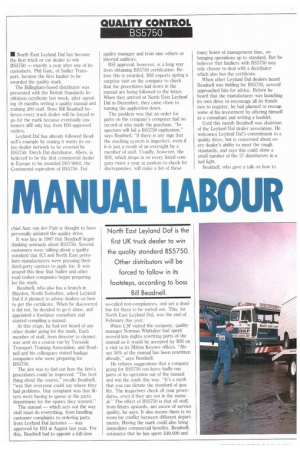
Page 59
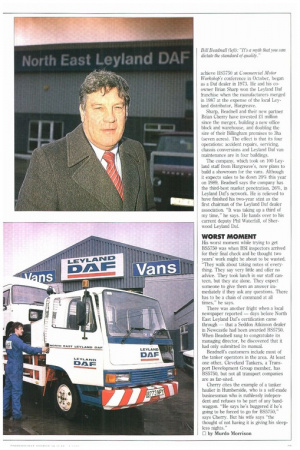
If you've noticed an error in this article please click here to report it so we can fix it.
North East Leyland Daf is the first UK truck dealer to win the quality standard BS5750. Other distributors will be forced to follow in its footsteps, according to boss Bill Beadnell.
I/ North East Leyland Daf has become the first truck or car dealer to win BS5750 — exactly a year after one of its customers. Phil Gate, of Sadler Transport, became the first haulier to be awarded the quality mark.
The Billingham-based distributor was presented with the British Standards Institution certificate last week, after spending 18 months writing a quality manual and training 200 staff. Boss Bill Beadnell believes every truck dealer will be forced to go for the mark because eventually customers vc5II only buy from BSI-approved outlets.
Leyland Daf has already followed Beadnell's example by stating it wants its entire dealer network to be covered by BS5750. Dutch Daf distributor, Alters, is believed to be the first commercial dealer in Europe to be awarded ISO 9002, the Continental equivalent of BS5750. Daf chief Aart van der Padt is thought to have personally initiated the quality drive.
It was late in 1987 that Beadnell began thinking seriously about BS5750. Several customers were talking about a quality standard that ICI and North East petrohum manufacturers were pressing their third-party carriers to apply for. It was around this time that Sadler and other road tanker companies began preparing for the mark.
Beadnell, who also has a branch in Blaydon, North Yorkshire, asked Leyland Daf if it planned to advise dealers on how to get the certificate. When he discovered it did not, he decided to go it alone, and appointed a freelance consultant and started compiling a manual.
At this stage, he had not heard of any other dealer going for the mark. Each member of staff, from director to cleaner, was sent on a course run by Teesside Transport Training Association, and Beadnell and his colleagues visited haulage companies who were preparing for BS5750.
The aim was to find out how the firm's procedures could be improved. "The best thing about the course," recalls Beadnell, "was that everyone could say where they had problems. One complaint was that fitters were having to queue at the parts department for the spares they wanted."
The manual — which sets out the way staff must do everything, from handling customer complaints to ordering parts from Leyland Daf factories — was approved by BSI in August last year. For this, Beadnell had to appoint a full-time quality manager and train nine others as internal auditors.
BSI approval, however, is a long way from obtaining BS5750 certification. Before this is awarded, BSI experts spring a surprise visit on the company to check that the procedures laid down in the manual are being followed to the letter. When they arrived at North East Leyland Daf in December, they came close to turning the application down.
The problem was that an order for parts on the company's computer had no record of who made the purchase. "Inspectors will fail a 11S5750 application," says Beadnell, -if there is any sign that the stocking system is imperfect, even if it is just a result of an oversight by a member of staff. Usually, however, the BSI, which drops in on every listed company twice a year at random to check for discrepancies, will make a list of these
so-called non-compliances, and set a deadline for them to be sorted out. This, for North East Leyland l)af, was the end of February this year.
When CM visited the company, quality manager Norman Whittaker had spent several late nights rewriting parts of the manual so it would be accepted by BSI on a visit to its Milton Keynes offices. "About 50% of the manual has been rewritten already," says Beadnell.
He refutes suggestions that a company going for BS5750 can leave badly-run parts of its operation out of the manual and win the mark this way. "It's a myth that you can dictate the standard of quality. The inspectors check all your procedures, even if they are not in the manual." The effect of BS5750 is that all staff, from fitters upwards, are aware of service quality, he says. It also means there is no room for conflict between different departments. Having the mark could also bring immediate commercial benefits. Beadnell, estimates that he has spent ,£40,000 and many hours of management time, on bringing operations up to standard. But he believes that hauliers with BS5750 may only choose to deal with a distributor which also has the certificate.
When other Leyland Daf dealers heard Beadnell was bidding for 8S5750, several approached him for advice. Before he heard that the manufacturer was launching its own drive to encourage all its franchises to register, he had planned to recoup some of his investment by offering himself as a consultant and writing a booklet.
Until this month Beadnell was chairman of the Leyland Daf dealer association. He welcomes Leyland Dais commitment to a quality drive, but is concerned about every dealer's ability to meet the tough standards, and says this could show a small number of the 57 distributors in a bad light.
Beadnell, who gave a talk on how to achieve BS5750 at Commercial Motor Workshop's conference in October, began as a Daf dealer in 1973. He and his coowner Brian Sharp won the Leyland Daf franchise when the manufacturers merged in 1987 at the expense of the local Leyland distributor, Hargreave.
Sharp, Beadnell and their new partner Brian Cherry have invested S',1 million since the merger, building a new office block and warehouse, and doubling the size of their Billingham premises to 3ha (seven acres). The effect is that its four operations: accident repairs, servicing, chassis conversions and Leyland Daf van maintenance are in four buildings.
The company, which took on 100 Leyland staff from Hargreave's, now plans to build a showroom for the vans. Although it expects sales to be down 20% this year on 1989, Beadnell says the company has the third-best market penetration, 26%, in Leyland Dots network. He is relieved to have finished his two-year stint as the first chairman of the Leyland Daf dealer association. It was taking up a third of my time," he says. He hands over to his current deputy Phil Waterfall, of Sherwood Levland Dd.
WORST MOMENT
His worst moment while trying to get BS5750 was when BSI inspectors arrived for their final check and he thought two years' work might be about to be wasted. They walk about taking notes of everything. They say very little and offer no advice. They took lunch in our staff canteen, but they ate atone. They expect someone to give them an answer immediately if they ask any questions. There has to be a chain of command at all times," he says.
There was another fright when a local newspaper reported — days before North East Leyland Dots certification came through — that a Seddon Atkinson dealer in Newcastle had been awarded 1355750. When Beadnell rang to congratulate its managing director, he discovered that it had only submitted its manual.
Beadnell's customers include most of the tanker operators in the area. At least one other, Cleveland Tankers, a Transport Development Group member, has BS5750, but not all transport companies are as far-sited.
Cherry cites the example of a tanker haulier in Humberside, who is a self-made businessman who is ruthlessly independent and refuses to be part of any bandwaggon. He says he's buggered if he's going to be forced to go for BS5750," says Cherry. But his wife says "the thought of not having it is giving his sleepless nights."
CI by Murdo Morrison