TECHNOLOGY: TRANSPORTER
Page 128
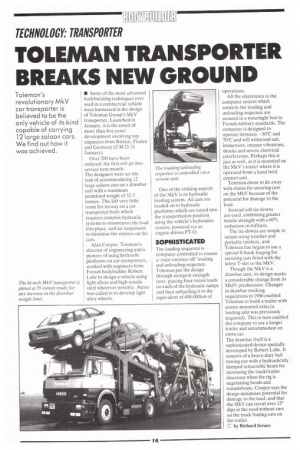
If you've noticed an error in this article please click here to report it so we can fix it.
TOLEMAN TRANSPORTER BREAKS NEW GROUND
Toleman's revolutionary MkV car transporter is believed to be the only vehicle of its kind capable of carrying 12 large saloon cars. We find out how it was achieved.
• Some of the most advanced bodybuilding techniques ever used in a commercial vehicle were harnessed in the design of Toleman Group's MkV transporter. Launched in January, it is the result of more than five years' development involving top engineers from Britain, France and Germany (CM 25-31 January).
Over 200 have been ordered; the first will go into service next month.
The designers were set the task of accommodating 12 large saloon cars on a drawbar unit with a maximum permitted weight of 32.5 tonnes. This left very little room for leeway on a car transporter body which requires complex hydraulic systems to manoeuvre the load into place. and air suspension to minimise the stresses on the cars.
Alan Cooper, Toleman's director of engineering and a pioneer of using hydraulic platforms on car transporters, worked with engineers from French bodybuilder Robert Lohr to design a vehicle using light alloys and high-tensile steel wherever possible. Alcoa was called in to develop light alloy wheels. One of the striking aspects of the MkV is its hydraulic loading system. All cars are loaded on to hydraulic platforms which are raised into the transportation position using the vehicle's hydraulics system, powered via an engine-driven PT-0.
SOPHISTICATED
The loading sequence is computer controlled to ensure a 'once-on/once off' loading and unloading sequence. Toleman put the design through stringent strength tests, placing four-tonne loads on each of the hydraulic ramps and then subjecting it to the equivalent of 400,000km of operations.
All the electronics in the computer system which controls the loading and unloading sequence are secured in a watertight box to French military standards. The computer is designed to operate between —30°C and 70°C and will withstand salt, immersion, intense vibrations, shocks and severe electrical interference. Perhaps this is just as well, as it is mounted on the MkV's trailer where it is operated from a hand held control unit.
Toleman chose to do away with chains for securing cars on the MkV because of the potential for damage to the load.
Instead soft tie-downs are used, combining greater tensile strength with a 60% reduction in stiffness.
The tie-downs are simple to secure using winches and portable ratchets, and Toleman has begun to use a special S-hook forging for securing cars fitted with the latest Tslot to the MkV.
Though the MkV is a drawbar unit, its design marks a considerable change from its Mk1V predecessor. Changes in drawbar tracking regulations in 1986 enabled Toleman to build a trailer with centre-mounted axles (a leading axle was previously required). This in turn enabled the company to use a longer trailer and accommodate an extra car.
The drawbar itself is a sophisticated device specially developed by Robert Lohr. It consists of a heavy-duty ball towing eye with a hydraulically damped retractable beam for increasing the truck/trailer clearance when the rig is negotiating bends and roundabouts. Cooper says the design minimises potential for damage to the load, and that the MkV can travel over 12° dips in the road without cars on the truck fouling cars on the trailer.
G by Richard Scracc