EJECTION SOLVES THE STABILITY PROBLEM
Page 126
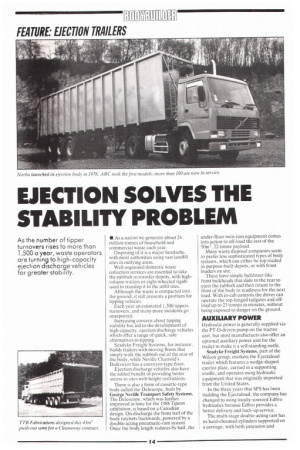
Page 127
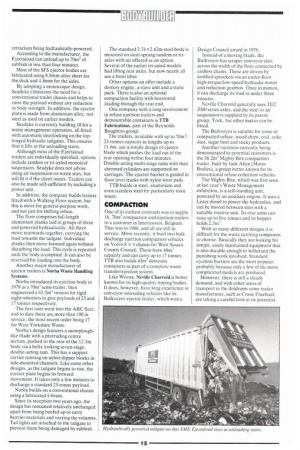
If you've noticed an error in this article please click here to report it so we can fix it.
As the number of tipper turnovers rises to more than 1,500 a year, waste operators are turnin9 to high-capacity ejection discharge vehicles for greater stability.
• As a nation we generate about 24 million tonnes of household and commercial waste each year.
Disposing of it is a major headache, with most authorities using vast landfill sites in outlying areas.
Well organised domestic waste collection services are essential to take the rubbish to transfer depots, with highvolume trailers or eight-wheeled rigids used to tranship it to the infill sites.
Although the waste is compacted into the ground, it still presents a problem for tipping vehicles.
Each year an estimated 1,500 tippers turnovers, and many more incidents go unreported.
Increasing concern about tipping stability has led to the development of high-capacity, ejection discharge vehicles which offer a range of quick, safe alternatives to tipping.
Seadyke Freight Systems, for instance, builds trailers with moving floors that simply walk the rubbish out of the rear of the body, while Neville Charrold's Bulkveyor has a conveyor-type floor.
Ejection discharge vehicles also have the added benefit of providing better access to sites with height restrictions.
There is also a form of cassette-type body called the Delescope, built by George Neville Transport Safety Systems. The Delescope, which was further improved in time for the 1988 Tipcon exhibition, is based on a Canadian design. On discharge the front half of the body ratchets backwards, powered by a double-acting pneumatic-ram system. Once the body length reduces by half, the
under-floor twin-ram equipment comes into action to off-load the rest of the 50m3, 22-tonne payload.
Many waste disposal companies seem to prefer less sophisticated types of body systems, which can either be top loaded in purpose-built depots, or with front loaders on site.
These have simple bulldozer-like front bulkheads that slide to the rear to eject the rubbish and then return to the front of the body in readiness for the next load. With in-cab controls the driver can operate the top-hinged tailgates and offload up to 23 tonnes in minutes, without being exposed to danger on the ground.
AUXILIARY POWER
Hydraulic power is generally supplied via the P1-0-driven pump on the tractor unit, but most manufactuers also offer an optional auxiliary power unit for the trailer to make it a self-standing outfit.
Seadyke Freight Systems, part of the Wilcox group. markets the Ejectaload trailer which features a wedge-shaped ejector plate, carried in a supporting cradle, and operates using hydraulic equipment that was originally imported from the United States.
In the three years that SFS has been building the Ejectaload, the company has changed to using locally-sourced Edbro hydraulics because Edbro provides a better delivery and back-up service.
The multi-stage double-acting ram has its hard-chromed cylinders supported on a carriage, with both extension and retraction being hydraulically-powered.
According to the manufacturer, the Ejectaload can unload up to 70m3 of rubbish in less than four minutes.
Most of the SFS ejector bodies are fabricated using 8.8mm alloy sheet for the deck and 4.8mm for the sides.
By adopting a monocoque design, Seadyke eliminates the need for a conventional trailer chassis and helps to raise the payload without any reduction in body strength. In addition, the ejector plate is made from aluminium alloy, not steel as used on earlier models.
Seadyke is currently building 18 for a waste management operation, all fitted with automatic interlocking on the top. hinged hydraulic tailgates. This ensures that it lifts as the unloading starts.
Although most of the Ejectaload trailers are individually specified, options include tandem or tri-axled monoleaf suspension. Seadyke does not advise using air suspension on waste sites, but will fit it if the client insists. Trailers can also be made self-sufficient by including a power unit.
In addition, the company builds trailers fitted with a Walking Floor system, but this is more for general-purpose work, and not just for shifting refuse.
The floor comprises full-length aluminium planks laid in groups of three and powered hydraulically. All three move rearwards together, carrying the load towards the tailgate. Individual planks then move forward again without disturbing the load. This cycle is repeated until the body is emptied. It can also be reversed for loading into the body.
Another major manufacturer of ejector trailers is Norba Waste Handling Systems.
Norba introduced its ejection body in 1978 as a 70m3 semi-trailer, then engineered a 43.5m3 version for rigid eight-wheelers to give payloads of 23 and 17 tonnes respectively.
The first ones went into the ARC fleet, and to date there are more than 100 in service, the most recent order being 17 for West Yorkshire Waste.
Norba's design features a snowploughlike blade with a protruding centre section, pushed to the rear of the 12.5m body via a hefty looking seven-stage, double-acting ram. This has a support carrier running on nylon slipper blocks in side-mounted channels. Like some other designs, as the tailgate begins to rise, the ejector plate begins its forward movement. It takes only a few minutes to discharge a standard 23-tonne payload.
Norba builds on a conventional chassis using a fabricated I-beam.
Since its inception two years ago, the design has remained relatively unchanged apart from being beefed up to carry heavier materials and varying the volumes. Tail lights are attached to the tailgate to prevent them being damaged by rubbish. The standard 2.31 x 2.62m steel body is mounted on steel-sprung tandem or triaxles with air offered as an option. Several of the earlier tri-axled models had lifting rear axles, but now nearly all use a front lifter.
Other options on offer include a donkey engine, a slave unit and a static pack. There is also an optional compaction facility with horizontal loading through the rear end.
One company with a long involvement in refuse ejection trailers and demountable containers is TTB Fabrications, part of the Reynolds Boughton group.
The trailers, available with up to 70m3/ 23-tonnes capacity in lengths up to 11.6m, use a simple design of ejector blade which pushes the load out of the rear opening within four minutes. Double-acting multi-stage rams with their chromed cylinders are supported on carriages. The ejector barrier is guided in floor level tracks with nylon wear pads.
TTB builds in steel, aluminium and even stainless steel for particularly toxic waste.
COMPACTION
One of its earliest contracts was to supply 18, 70m3 compaction and ejection trailers to a customer in Interleuven, Belgium. That was in 1980, and all are still in service. More recently, it built two bulk discharge ejection compaction vehicles on Volvo 8 x 4 chassis for West Sussex County Council. These have 48m' capacity and can carry up to 17 tonnes. TTB also builds 43mi demount containers as part of a complete waste transfer/ejection system.
Like Wilcox, Neville Charrold is better known for its high-quality tipping bodies. It does, however, have long experience in conveyor-unloading vehicles like its Bulkveyor ejector trailer, which won a Design Council award in 1976.
Instead of a moving blade, the Bulkveyor has scraper conveyor slats across the width of the floor connected by endless chains. These are driven by toothed sprockets via an under-floor high-torque/low-speed hydraulic motor and reduction gearbox. Once in motion, it can discharge its load in under three minutes.
Neville Charrold generally uses TEC 2000 series axles, and the steel or air suspension is supplied by its parent group, York, but other makes can be fitted.
The Bulkveyor is suitable for loose or compacted refuse, wood chips. coal, coke dust, sugar beet and sticky products.
Another variation currently being demonstrated to potential customers is the 38.2m3 Mighty Bite compaction trailer, built by Jack Allen (Motor Bodies), a group better known for its conventional refuse collection vehicles.
The Mighty Bite, which was first seen at last year's Waste Management exhibition, is a self-standing unit, powered by an auxiliary engine. It uses a Lister diesel to power the hydraulics, and can be moved between sites with a suitable tractive unit. Its rear arms can raise up to five tonnes and its hopper holds 2.3m3.
With so many different designs it is difficult for the waste carrying companies to choose. Basically they are looking for simple, easily maintained equipment that is also durable enough to withstand the punishing work involved. Standard ejection barriers are the most popular, probably because only a few of the more complicated models are produced.
However, there is still a steady demand, and with other areas of transport in the doldrums some trailer manufactures, such as Crane Fruehauf, are taking a careful look at its potential.