L ast month hauliers working out of Dublin Port stopped working
Page 38
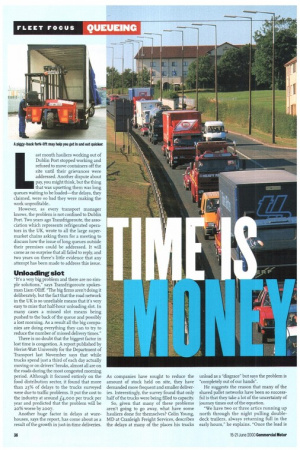
Page 39
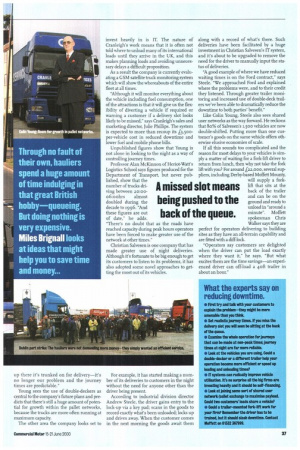
If you've noticed an error in this article please click here to report it so we can fix it.
and refused to move containers off the site until their grievances were addressed. Another dispute about pay, you might think, but the thing that was upsetting them was long queues waiting to be loaded—the delays, they claimed, were so bad they were making the work unprofitable.
However, as every transport manager knows, the problem is not confined to Dublin Port. Two years ago Transfrigoroute, the association which represents refrigerated operators in the UK, wrote to all the large supermarket chains asking them for a meeting to discuss how the issue of long queues outside their premises could be addressed. It will come as no surprise that all failed to reply, and two years on there's little evidence that any attempt has been made to address this issue.
Unloading slot
"It's a very big problem and there are no simple solutions," says Transfrigoroute spokesman Liam 011iff. "The big firms aren't doing it deliberately, but the fact that the road network in the UK is so unreliable means that it's very easy to miss that half-hour unloading slot In many cases a missed slot means being pushed to the back of the queue and possibly a lost morning. As a result all the big companies are doing everything they can to try to reduce the number of missed delivery times."
There is no doubt that the biggest factor in lost time is congestion. A report published by Her jot-Watt University for the Department of Transport last November says that while trucks spend just a third of each day actually moving or on drivers' breaks, almost all are on the roads during the most congested morning period. Although it focused entirely on the food distribution sector, it found that more than 23% of delays to the trucks surveyed were due to traffic problems. It put the cost to the industry at around f4,000 per truck per year and predicted that the problem will be 20% worse by 2007
Another huge factor in delays at warehouses, says the report, has come about as a result of the growth in just-in-time deliveries. As companies have sought to reduce the amount of stock held on site, they have demanded more frequent and smaller deliveries. Interestingly, the survey found that only half of the trucks were being filled to capacity.
So, given that many of these problems aren't going to go away, what have some hauliers done for themselves? Colin Young, MD at Cranleigh Freight Services, describes the delays at many of the places his trucks unload as a "disgrace" but says the problem is "completely out of our hands".
He suggests the reason that many of the shared pallet networks have been so successful is that they take a lot of the uncertainty of journey times out of the equation.
"We have two or three artics running up north through the night pulling doubledeck trailers, always returning full in the early hours," he explains. "Once the load is
up there it's trunked on for delivery—it's no longer our problem and the journey times are predictable."
Young sees the use of double-deckers as central to the company's future plans and predicts that there's still a huge amount of potential for growth within the pallet networks, because the trucks are more often running at maximum capacity.
The other area the company looks set to invest heavily in is IT. The nature of Cranleigh's work means that it is often not told where to unload many of its international loads until they arrive in the UK, and this makes planning loads and avoiding unnecessary delays a difficult proposition.
As a result the company is currently evaluating a GSM satellite truck monitoring system which will show the whereabouts of the entire fleet at all times.
"Although it will monitor everything about the vehicle including fuel consumption, one of the attractions is that it will give us the flexibility of diverting a vehicle if required or warning a customer if a delivery slot looks likely to be missed," says Cranleigh's sales and marketing director, Julie Phillips. The system is expected to more than recoup its £3,500per-vehicle cost in reduced downtime and lower fuel and mobile phone bills.
Unpublished figures show that Young is not alone in looking to the night as a way of controlling journey times.
Professor Alan McKinnon of Heriot-Watt's Logistics School says figures produced for the Department of Transport, but never published, show that the number of trucks driving between 2o:oo o6:oohrs almost doubled during the decade to 1996. And these figures are out of date," he adds. "There's no doubt that as the roads have reached capacity during peak hours operators have been forced to make greater use of the network at other times."
Christian Salvesen is one company that has made greater use of night deliveries. Although it's fortunate to be big enough to get its customers to listen to its problems, it has also adopted some novel approaches to getting the most out of its vehicles.
For example, it has started making a number of its deliveries to customers in the night without the need for anyone other than the driver being present.
According to industrial division director Andrew Steele, the driver gains entry to the lock-up via a key pad; scans in the goods to record exactly what's been unloaded; locks up and drives away. When the customer comes in the next morning the goods await them along with a record of what's there. Such deliveries have been facilitated by a huge investment in Christian Salvesen's IT system, and it's about to be upgraded to remove the need for the driver to manually input the status of deliveries.
"A good example of where we have reduced waiting times is on the Ford contract," says Steele. "We approached Ford and explained where the problems were, and to their credit they listened. Through greater trailer monitoring and increased use of double-deck trailers we've been able to dramatically reduce the downtime to both parties' benefit."
Like Cohn Young, Steele also sees shared user networks as the way forward. He reckons that So% of Salvesen's 1,50o vehicles are now double-shifted. Putting more than one customer's goods on the same vehicle offers otherwise elusive economies of scale.
If all this sounds too complicated and the reason for most delays to your vehicles is simply a matter of waiting for a fork-lift driver to return from lunch, then why not take the fork lift with you? For around £22,000, several suppliers, including Derby-based Moffett Mounty, will supply a forklift that sits at the back of the trailer and can be on the ground and ready to unload in "around a minute". Moffett spokesman Chris Walker says they are perfect for operators delivering to building sites as they have an all-terrain capability and are fitted with a diff-lock.
"Operators say customers are delighted when the driver can put the load exactly where they want it," he says. "But what excites them are the time savings—an experienced driver can off-load a 40ft trailer in about an hour."