FILLING DENT IN LIGH LLOY PANELS
Page 14
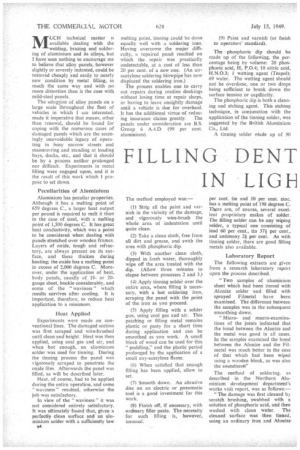
Page 15
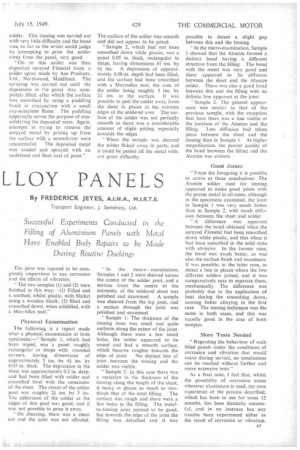
If you've noticed an error in this article please click here to report it so we can fix it.
By FREDERICK JEYES, A.1.N.A., M.1.R.T.E, Transport Engineer, J. Sainsbury, Ltd.
Successful Experiments Conducted in the Filling of Aluminium Panels with Metal Have Enabled Body Repairs to be Made During Routine Dockings
MUCH technical matter is available dealing with the welding, brazing and soldering of aluminium and its alloys, but I have seen nothing to encourage me to believe that alloy panels, however slightly or severely indented, could be restored cheaply and easily to nearly new condition by metal filling, in much the same way and with nomore distortion than is the case with mild-steel panels.
The adoption of alloy panels on a• large scale throughout the fleet of vehicles in which I am interested, made it imperative that means, other than renewal, should be found for coping with the numerous cases of damaged panels which are the seemingly unavoidable legacy of opera, ting in busy narrow streets and inaneeuvring and standing at loading bays, -docks, etc., and that it should be by a process neither prolonged nor difficult. Experiments in metal filling were engaged upon, and it is the result of this work which I propose to set down.
Peculiarities of Aluminium Aluminium has peculiar properties. Although it has a melting point of 659 degrees C., a larger heat output per pound is required to melt it than in the case of steel, with a melting point of 1,500 degrees C. It has great heat cOnductivity, which was a point to be considered when dealing with panels stretched over wooden frames. Layers of oxide, tough and refractory, are always present on its surface, and these thicken during heating; the oxide has a melting point in excess of 2,000 degrees C. Moreover, under the application of heat, body panels, usually of 18or 20gauge sheet, buckle considerably, and some of the " waviness " which results survives after cooling. It is important, therefore, to reduce heat application to a minimum.
Heat Applied
Experiments were made on conventional lines. The damaged section was first scraped and wire-brushed until clean and bright. Heat was then applied, using coal gas and air, and when hot enough, an aluminium solder was used for tinning. During the tinning process the panel was vigorously scraped to penetrate the oxide film. Afterwards the panel was filled, as will be described later.
Heat, of course, had to be applied during the entire operation, and some "waviness" resulted, otherwise the job was satisfactory.
In view of the " waviness " it was not considered entirely satisfactory. It was ultimately found that, given a perfectly -clean sttrface and an aluminium solder with a sufficiently low 54 melting point, tinning could be done equally well with a soldering iron. Having overcome the major difficulty, a repaired panel resulted on which the repair was practically undetectable, at a cost of less than 20 per cent. of a new one. An airacetylene soldering blowpipe has now displaced the soldering iron.)
The process enables one to carry out repairs during routine. dockings without losing time at repair shops, or having to leave unsightly damage until a vehicle is due for overhaul. It has the additional virtue of reduc
ing insurance claims greatly. The panels under consideration are 133. Group 6 A.4.13. (99 per cent. aluminium).
The method employed was:— (1) Strip all the paint and varnish in the vicinity of the damage, and vigorously wire-brush the whole area ot indentation until quite clean.
(2) Take a clean cloth, free from all dirt and grease, and swab the area with phosphoric dip.
(3) With another clean cloth, dipped in fresh water, thoroughly wipe off the area treated with the dip. (Allow• three minutes to elapse between processes 2 and 3.) (4) Apply tinning solder over the entire area, where filling is necessary, with a hot soldering iron, .scraping the panel_ with the point of the iron as you proceed.
(5) Apply filling with a solder gun, using Coal gas and air. This patching or filling metal remains plastic or pasty for a short time during application and can be smoothed as you work. A small block of wood can be used for this "puddling,' and the plastic period prolonged by the application of a small oxy-acetylene flame.
(6) When satisfied that enough filling has been applied, allow to set.
(7) Smooth down. An abrasive disc on an electric or pneumatic tool is a good investment for this work.
(S) Finish off, if necessary, with ordinary filler paste. The necessity for such filling is, however, unusual. (9) Paint and varnish (or finish to operators' standard).
The phosphoric dip should be made up of the following, the percentage being by volume: 20 phosphoric acid, Hs P.0.4; 10 nitric acid, H.N.0.3-; 1 wetting agent (Teepol); 69 water. The wetting agent should not be overdone, one or two drops being sufficient to break down the surface tension or capillarity.
The phosphoric dip is both a cleaning and etching agent. This etching technique, in conjunction with the application of the tinning solder, was suggested by the British Aluminium Co., Ltd.
A tinning solder Made up of 90 per cent, tin and 10 per cent, zinc, has a melting point of 198 degrees C. There are, of course, several excellent proprietary makes of solder. The filling solder can be any wiping solder, a typical one consisting of lead 60 per cent., tin 37i per cent., and antimony 2f per cent. As with tinning solder, there are good filling metals also available.
Laboratory Report
The following extracts are given from a research laboratory report upon the process described.
"Two samples of aluminium sheet which had been tinned with Alunize solder and filled with sprayed Filrnetal have been examined. The difference between the samples was in the subsequent smoothing down.
" Microand macro-examinations of the joints indicated that the bond between the Alunize and the metal was good in all cases. In the samples examined the bond between the Alunize and the Filmetal was much better in the case of that which had been wiped using a wooden block, as was also the soundness?'
The method of soldering, as described in the Northern Aluminium development department's works visit report, was as follows:— " The damage was first cleaned by scratch brushing, swabbed with a solution of phosphoric acid, and then washed with clean wafer. The cleaned surface waS then finned, using an ordinary iron and Alunize solder. This tinning was carried out with very little difficulty and the bond was, so far as the writer could judge by attempting to prise the solder away from the panel, very good.
"On to this solder was then deposited sprayed Filmetal from a solder spray made by Ace Products, Ltd., Northwood, Middlesex. The spraying was carried out until the depression in the panel was completely filled, after which the surface was smoothed by using a puddling block in conjunction with a small oxy-acetylene flame. The puddling apparently serves the purpose of consolidating the deposited mass. Again, attempts at trying to remove the sprayed metal by prising up from the surface with a screwdriver were unsuccessful. The deposited metal was sanded and sprayed with an undercoat and final coat of paint."
The joint was reputed to be completely impervious to any corrosion and the effects of vibration.
"The two samples (1) and (2) were finished in this way:—(1) Filled and s..loothed, whilst plastic, with Slicket using a wooden block; (2) filled and smoothed down, when solidified, with a Morristlex tool."
Physical Examination
The following is a report made after a physical examination of both specimens:—" Sample 1, which had been wiped, was a panel roughly rectangular in shape with rounded corners, having dimensions of approximately 5 ins. by 4i ins. by 0.05 in. thick. The depression in the sheet was approximately 0.2 in. deep, and had been. filled with solder and smoothed level with the remainder of the sheet. The extent of the solder pool was roughly 2i ins. by 3 ins. The adherence of the solder at the edges of this pool was good, and it was not possible to prise it away.
On shearing, there was a clean cut and the joint was not affected. The surface of the solder was smooth and did not appear to be pitted.
"Sample 2, which had not been smoothed down while plastic, was a panel 0.05 in. thick, rectangular in shape, having dimensions 41 ins. by 6i ins. A depression of approximately 0.08-in, depth had been filled, and the surface had been smoothed with a Morrisflex tool, the area of the solder being roughly 5 ins, by n ins at the surface. It was possible to peel the solder away from the sheet in places at the. extreme edges of the soldered area. The surface of the solder was not perfectly smooth as there was a considerable amount of slight pitting, especially towards the edges.
" When the sample was sheared the solder flaked away in parts, and it could be peeled off the metal without great difficulty.
"In the macro examination, Samples 1 and 2 were sheared across the centre of the solder pool, and a section from the centre to the extremity of the soldered sheet was polished and examined. A sample was sheared from the lap joint, and a section through the joint was polished and examined.
"Sample 1: The thickness of the tinning zone was small and quite uniform along the extent of the joint. Although there were a few small holes, the solder appeared to be sound and had a smooth surface, which became rougher towards the edge of joint. No distinct line of joint between the tinning and the solder was visible.
"Sample 2: In this case there was a variation in the thickness of the tinning along the length of the sheet, it being at places as much as two
thirds that of the total filling. The surface was rough and there were a few holes in the filling. The metalto-tinning joint seemed to be good, but towards the edge of the joint the filling was detached and it was
possible to detect a slight gap between this and the tinning.
" In the micro-examination, Sample I showed that the Alunize formed a distinct band having a different structure from the filling. The bond with the metal was very good and there appeared to be diffusion between the sheet and the Alunize solder. There was also a good bond between this and the filling with no definite line apparent at the joint.
"Sample 2: The general appearance was similar to that of the previous sample, with the exception that here there was a line visible at the junction of the Alunize and the filling. Less diffusion had taken place between the sheet and the tinning than in Sample 1. At higher magnification, the poorer quality of the bond between the filling and the Alunize was evident.
Good Joints "From the foregoing it is possible to arrive at these conclusions: The Alunize solder used for tinning appeared to make good joints with the parent metal in all cases, although in the specimens examined, the joint in Sample 1 was very much better than in Sample 2, with much diffusion between the sheet and solder.
difference was apparent between the bond obtained when the sprayed Filmetal had been smoothed down while plastic, and that when, it had been smoothed in the solid state with abrasive. In the former case, the bond was much better, as was also the surface finish and soundness. It was possible, in the latter case, to detect a line in places where the two different solders joined, and it was comparatively easy to separate them, mechanically, The difference was probably due to the application of heat during the smoothing down, causing better alloying in the first case. The tinning technique was the same in both cases, and this was equally good in the case of both samples.
More Tests Needed
"Regarding the behaviour of such filled panels under the conditions of corrosion and vibration that would occur during service, no conclusions can be reached without further and more extensive tests."
As a final note, I feel that, whilst the possibility of corrosion exists wherever aluminium is used, my own experience of the process described, which has been in use for some 12 months, has been distinctly successful, and in no instance has any trotible been experienced either as the result of corrosion or vibration.