There may be brass in hauling muck but you need
Page 64
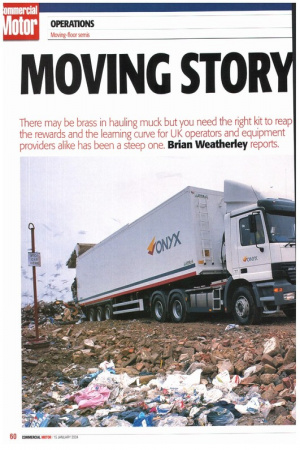
Page 65

Page 66
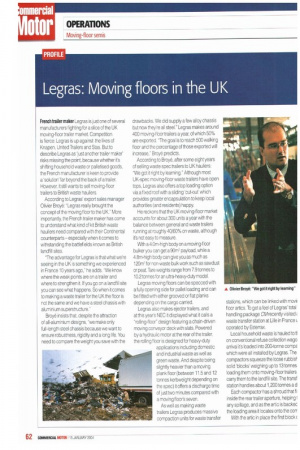
Page 67
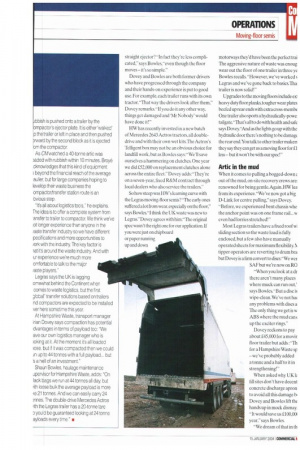
Page 68
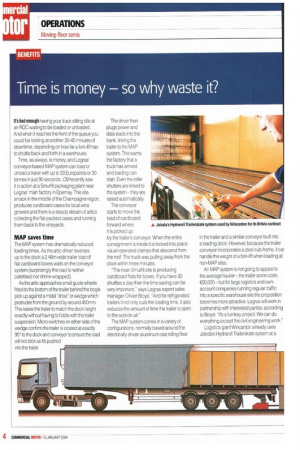
Page 69
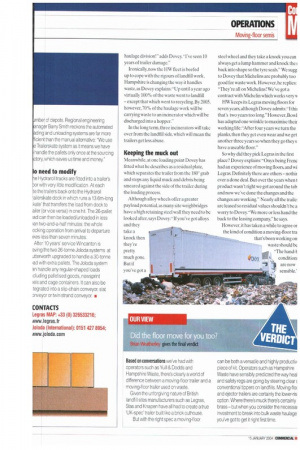
If you've noticed an error in this article please click here to report it so we can fix it.
the right kit to reap the rewards and the learning curve for UK operators and equipment providers alike has been a steep one. Brian Weatherley reports.
INhen the first moving-floor trailers appeared in the UK they looked like the obvious answer to bulk aste handling. Good capacity, flexible to use id above all infinitely safer than a convenonal tipper when discharging. Unfortunately, iat initial optimism soon sank beneath the arface of UK landfill sites. It's now clear that iere's a world of difference between an "on" rid "off-road" moving-floor trailer— and the :arning process has often been a painful one. Hampshire Waste (HW) was Setup by 'rench giant Onyx 10 years ago. It has a rolling 5-year contract to handle waste for Hampshire :ounty Council, working under the umbrella organisation of Hampshire Waste Integra.
HW's haulage division, based at Havant, has a simple remit,according to transport manager Brian Dovey."We do all the waste and recyclable materials from household waste to mixtures of soil and rubble, paper, card and bottles."
That material is carried by HW's vehicles to transfer stations, recycling operations, landfill sites and incinerators throughout the county. As well as operating 22 R0-110 vehicles on collection work Frw runs 28 moving-floor bulk waste trailers, all built by Legras.There are another four in the pipeline that will gradually replace older stock. The first moving-floor trailer entered servic seven years ago, and they all operate in a toug environment."They're used every day and ge 'destroyed' every day!" quips haulage mainte nance supervisor Shaun Bowles.
Flexibility, please
And Dovey demands maximum flexibility from them. "Hampshire Waste also runs a composting operation and the moving-floor Legras trailers haul compost and green waste. he says."They can do anything from landfill tc incinerators to recycling."
However, the bulk of the work involves transfer of non-black-bag waste to landfill site and black bags to the county's incinerator. "We run anything onto a landfill as long as it's not hazardous." Dovey explains. "When the incinerators get overloaded then their material goes to landfill."
So why a moving floor? Dovey's response i! unequivocal: "Our policy is we don't like 40ft tippers on a landfill!"
Given the on-going health and safety concerns over artic tipper stability that's a wis decision as moving floors clearly offer a lower risk route to discharging a ioad."It's also got to do with the payload," Bowles reports. "We used to run 20 Boughton steel ejectors with a 70m4 capacity— we now run the Legras movin floors which are 8.5m and weigh 2.5 tonnes less." The Legras trailers have alloy bodies bu steel chassis.
But isn't the intricacy of a moving-floor trailer a poor compromise compared with a French trailer maker Legras is just one of several manufacturers fighting for a slice of the UK moving-floor trailer market. Competition is fierce Legras is up against the likes of Knapen, United Trailers and Stas. But to describe Legras as 'just another trailer maker' risks missing the point, because whether its shifting household waste or palletised goods, the French manufacturer is keen to provide a 'solution far beyond the back of a trailer. However, it still wants to sell moving-floor trailers to British waste hauliers.
According to Legras' export sales manager Olivier Broye: "Legras really brought the concept of the moving floor to the UK.' More importantly. the French trailer maker has come to understand what kind of kit British waste hauliers need compared with their Continental counterparts especially when it comes to withstanding the battlefields known as British landfill sites.
"The advantage for Legras is that what we're seeing in the UK is something we experienced in France 10 years ago," he adds. "We know where the weak points are on a trailer and where to strengthen it. If you go on a landfill site you can see what happens. So when it comes to making a waste trailer for the UK the floor is not the same and we have a steel chassis with aluminium superstructure."
Broye insists that, despite the attraction of all-aluminium designs. "we make only full-length steel chassis because we want to ensure robustness, rigidity and a long life. You need to compare the weight you save with the drawbacks. We did supply a few alloy chassis but now they're all steel." Legras makes around 400 moving-floor trailers a year, of which 50% are exported. "The goal is to reach 500 walking floor and the percentage of those exported will increase," Broye predicts.
According to Broye, after some eight years of selling waste spec trailers to UK hauliers: "We got it right by learning." Although most UK-spec moving-floor waste trailers have open tops, Legras also offers atop loading option via a fixed roof with a sliding 'cut-out' which provides greater encapsulation to keep local authorities (and residents) happy.
He reckons that the UK moving-floor market accounts for about 300 units a year with the balance between general and waste trailers running at roughly 40/60% on waste, although it's not easy to measure.
With a 4.0m-high body on a moving-floor bulker you can get a 901-6' payload, while a 4.8m-high body can give you as much as 120rn2 for non-waste bulk work such as sawdust or peat. Tare weights range from 7.9 tonnes to 10.2 tonnes for an ultra-heavy-duty model.
Legras moving floors can be specced with a fully opening side for pallet loading and can befitted with either grooved or flat planks depending on the cargo carried.
Legras also makes ejector trailers, and at this year's NEC it displayed what it calls a "rolling-floor" design featuring a chain-driven moving conveyor deck with slats. Powered by a hydraulic motor at the rear of the trailer, the rolling floor is designed for heavy-duty applications including domestic and industrial waste as well as green waste. And despite being slightly heavier than a moving plank floor (between 11.5 and 12 tonnes kerbweight depending on the spec) it offers a discharge time of just two minutes compared with a moving floor's seven.
As well as making waste trailers Legras produces massive compaction units for waste transfer stations, which can be linked with movii floor artics. To get a feel of Legras' total handling package CM recently visited waste transfer station at Lille in France +, operated by Esterrax.
Local household waste is hauled to tl on conventional refuse collection wago arrival its loaded into 200-tonne comps which were all installed by Legras. The compactors squeeze the loose rubbist• solid 'blocks' weighing up to 13 tonnes loading them onto moving-floor trailers carry them to the landfill site. The transf station handles about 1,200 tonnes ad Each compactor has a shroud that fi inside the rear trailer aperture, helping I any spillage, and as the artic is backec the loading area it locates onto the corr With the artic in place the first block c bbish is pushed onto a trailer by the ompactor's ejector plate. It is either Walked' p the trailer or left in place and then pushed rward by the second block as it is ejected om the compactor.
As CMwatched a 40-tonne artic was )aded with rubbish within 10 minutes. Broye .cknowiedges that this kind of equipment >beyond the financial reach of the average aulier. but for large companies hoping to levelop their waste business the ompactoritransfer station route is an .bvious step.
"It's all about logistics tools," he explains. The idea is to offer a complete system from .ansfer to trailer to compactor. We think we've lot longer experience than anyone in the taste transfer industry so we have different pecif ications and more opportunities to fork with the industry The key factor is ]at its around the waste industry. And with ur experience we're much more omfortable to talk to the major taste players."
Legras says the UK is lagging omewhat behind the Continent when comes to waste logistics, but the first global" transfer solutions based on trailers nd compactors are expected to be installed ver here sometime this year.
At Hampshire Waste, transport manager Irian Dovey says compaction has potential dvantages in terms of payload too: "We ave our own logistics manager who is 3oking at it. At the moment it's all loaded 3ose, but if It was compacted then we could in up to 44 tonnes with a full payload... but S a hell of an investment."
Shaun Bowles, haulage maintenance Jpervisor for Hampshire Waste, adds: "On lack bags we run at 44 tonnes all day, but fith loose bulk the average payload is more ce 21 tonnes. And we can easily carry 24 nnes. The double-drive Mercedes Actros tith the Legras trailer has a 20-tonne tare 3 you'd be guaranteed looking at 24 tonne ayloads every time." • straight ejector? "In fact they're less complicated," says Bowles,"even though the floor moves it's so simple."
Dovey and Bowles are both former drivers who have progressed through the company and their hands-on experience is put to good use. For example. each trailer runs with its own tractor. "That way the drivers look after them." Dovey remarks. "If you do it any other way, things get damaged and Mr Nobody' would have clone it!"
11W has recently invested in a new batch of Mercedes 2643 Actros tractors, all doubledrive and with their own wet kits. The Actros's Telligent box may not be an obvious choice for landfill work,but as Bowles says:"We'll save ourselves a hammering on clutches. One year we did £52,000 on replacement clutches alone across the entire fleet." Dovey adds: "They're on a seven-year, fixed R&M contract through local dealers who also service the trailers."
So how steep was HW's learning curve with the Legras moving-floor semis'? "The early ones suffered a lot from wear, especially on the floor," says Bowles."1 think the UK waste was new to Legras.Dovey agrees with him:"The original spec wasn't the right one for our application. If you were just on chipboard or paper running up and down motorways they'd have been the perfect trai The aggressive nature of waste was erioug wear out the floor of one trailer in three ye Bowles recalls."However, we've worked Legras and we've gone back to basics.Tha trailer is now solid!"
Upgrades to the moving floors include ex heavy duty floor planks.tougher wear plates beefed up rear ends with extra cross-membe One trailer also sports a hydraulically-powe tailgate."That's all to do with health and safe says Dovey, "And as the lights go up with the hydraulic door there's nothing to be damage the rear end.You talk to other trailer maken they say they can get us a moving floor for £1 lessbut it won't be with our spec!"
Artic in the mud
When it comes to pulling a bogged-down out of the mud, on-site recovery crews are renowned for being gentle. Again, HW lea from its experience. "We've now got a big D-Link for centre pulling," says Dovey. -Before, we experienced bent chassis whe the anchor point was on one frame rail... w even had lorries stretched!"
Most Legras trailers have a fixed roof wi sliding section so the waste load is fully enclosed, but a few also have manually operated sheets for maximum flexibility. N tipper operators are reverting to drum bra but Dovey is a firm convert to dises:"We wer SAF but we're now on RO "When you look at a dr there aren't many places where muck can run out,' says Bowles. "But a disc is wipe-clean. We've not hac any problems with discs a The only thing we get is w ABS where the mud can c up the exciter rings."
Dovey reckons to pay about £45,000 for a movir floor trailer but adds :"Th for a Hampshire Waste sp we've probably added a tonne and a half to it in strengthening!
When asked why UK 1E fill sites don't have decent concrete discharge apron to avoid all this damage b Dovey and Bowles lift the hands up in mock dismay. "It would save us £100,001 year.says Bowles.
"We dream of that in th It's bad enough having your truck sitting idle at an ADO waiting to be loaded or unloaded. And when it reaches the front of the queue you could be looking at another 30-45 minutes of downtime, depending on how far a fork-lift has to shuttle back and forth in a warehouse.
Time, as always, is money, and Legras' conveyor-based MAP system can load or unload a trailer with up to 33 Europallets 01 30 tonnes in just 90 seconds. CM recently saw it in action at a Smurfft packaging plant near Legras' main factory in Epernay. This site, smack in the middle of the Champagne region, produces cardboard cases for local wine growers and there is a steady stream of artics collecting the flat-packed cases and running them back to the vineyards.
MAP saves time
The MAP system has dramatically reduced loading times. As the attic driver reverses up to the dock a 2,46m-wide trailer load of flat cardboard boxes waits on the conveyor system (surprisingly the load is neither palletised nor shrink-wrapped).
As the attic approaches small guide wheels fitted to the bottom of the trailer behind the bogie pick up against a metal 'shoe" or wedge which protrudes from the ground by around 450mm. This raises the trailer to match the dock height exactly without having to f iddle with the trailer suspension. Micro-switches on elther side of the wedge confirm the trailer is located at exactly 90° to the dock and conveyor to ensure the load will not sock as it's pushed into the trailer. The driver then plugs power and data leads into the bank, linking the trailer to the MAP system. This warns the factory that a truck has arrived and loading can start. Even the roller shutters are linked to the system -they are raised automatically The conveyor starts to move the load of cardboard forward where it is picked up by the trailer's conveyor. When the entire consignment is inside it is locked into place via air-operated clamps that descend from the roof. The truck was pulling away from the dock within three minutes.
"The main Smurf it site is producing cardboard flats for boxes. If you have 30 shuttles a day then the time saving can be very important," says Leg ras export sales manager Olivier Broye. And for refrigerated trailers it not only cuts the loading time, it also reduces the amount of time the trailer is open to the outside air."
The MAP system comes in a variety of configurations. normally based around the electrically driven aluminium-slat rolling floor in the trailer and a similar conveyor built into a loading dock. However, because the trailer conveyor incorporates a steel sub-frame, it car handle the weight of a fork-lift when loading at non-MAP sites.
An MAP system is not going to appeal to the average haulier the trailer alone costs €50,000 but for large logistics and ownaccount companies running regular traffic into a specific warehouse site the proposition becomes more attractive. Legras will work in partnership with interested parties; according to Broyei "it's a turnkey project. We can do everything except the civil engineering work."
Logistics giant Wincanton already uses Joloda's HydrarollTrallerskate system at a mber of depots. Regional engineering anager Barry Smith reckons the automated ading and unloading systems are far more icient than the manual alternative: "We use e Trailerskate system as it means we have handle the pallets only once at the sourcing ctory, which saves us time and money."
o need to modify
e Hydraroll tracks are fitted into a trailer's r with very little modification. At each te the trailers back onto the Hydraroll ailerskate dock in which runs a 13.6m-long ikate' that transfers the load from dock to ailer (or vice versa) in one hit. The 26-pallet ad can then be loaded/unloaded in less on two-and-a-half minutes: the whole °eking operation from arrival to departure tkes less than seven minutes.
After 10 years service Wincanton is aving the two 26-tonne Joloda systems at utterworth upgraded to handle a 30-tonne lad with extra pallets. The Joloda system an handle any regular-shaped loads 'eluding palletised goods, newsprint els and cage containers. It can also be tegrated into a slip-chain conveyor, slat Dnveyor or twin strand conveyor. • haulage division!" adds Dovey. -I've seen 10 years of trailer damage."
Ironically,now the HW fleet is beefed up to cope with the rigours of landfill work, Hampshire is changing the way it handles waste. as Dovey explains:"Up until a year ago virtually 100% of the waste went to landfill except that which went to recycling. By 2005. however:70% of the haulage work will be carrying waste to an incinerator which will be discharged into a hopper."
In the long term. three incinerators will take over from the landfill side, which will mean the trailers get less abuse.
Keeping the muck out
Meanwhile, at one loading point Dovey has fitted what he describes as a residual plate, which separates the trailer from the 180° grab and stops any liquid muck and debris being smeared against the side of the trailer during the loading process. steel wheel and they take a knock you can always get a lump hammer and knock the back into shape so the tyre seals." We sugg to Davey that Michelins are probably too good for waste work. However, he replies: "They're all on Michelins! We've got a contract with Michelin which works very vl HW keeps its Legras moving floors for seven years. although Dovey admits:"! thii that's two years too long." However, Bowl has adapted one wrinkle to maximise their working life: "After four years we turn the planks, then they get even wear and we get another three years so when they go they s have a useable floor."
So why did they pick Legras in the first place? Dovey explains: "Onyx being Frenc had an experience of moving floors, and wi Legras. Definitely there are othersnothir ever a done deal. But over the years when t product wasn't right we got around the tab and now we've done the changes and the changes are working." Nearly all the traile: are leased so residual values shouldn't be a worry to Dovey. -We more or less hand the back to the leasing company." he says.
However,it has taken a while to agree or the kind of condition a moving-floor tra that's been working on waste should be "The hand-t 40Nyx condition: are now sensible.'