Four Aspects of Engine Design
Page 71
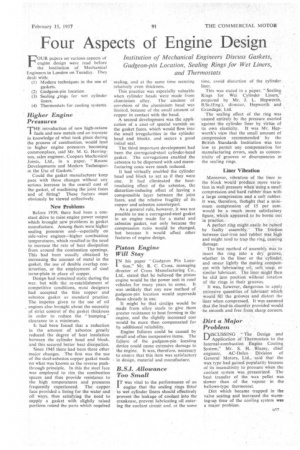
If you've noticed an error in this article please click here to report it so we can fix it.
Institution of Mechanical Engineers Discuss Gaskets, Gudgeon-pin Location, Sealing Rings for Wet Liners, and Thermostats
FOUR papers on various aspects of engine design were read before the Institution of Mechanical Engineers in London on Tuesday. They
dealt with: (1) Modern techniques in the use of gaskets.
(2) Gudgeon-pin location.
(3) Sealing Jings for wet cylinder liners.
(4) Thermostats for cooling systems.
Higher Engine Pressures
THE introduction of new high-octane fuels and new metals and an increase in knowledge of what took place during the process of combustion, would lead to higher engine pressures becoming commonplace, said Mr. M. G. Herrington, sales engineer, Coopers Mechanical Joints, Ltd., in a paper, "Recent Developments and Modern Techniques in the Use of Gaskets."
Could the gasket manufacturer keep pace with these changes without any serious increase in the overall cost of the gasket, of machining the joint faces and of fitting? These factors must obviously be viewed collectively.
New Problems
Before 1939, there had been a constant drive to raise engine power output which brought new problems in gasket manufacture, Among them were higher sealing pressures and—especially on side-valve engines—higher combustion temperatures, which resulted in the need to increase the rate of heat dissipation • from around the combustion openings. This had been usually obtained by increasing the amount of metal in the gasket. the use of double overlap construction, or the employment of steel terne-plate in place of copper.
Design had remained static during the war, but with the re-establishment of competitive conditions, most designers had accepted the thin copper and asbestos gasket as standard practice. The impetus given to the use of oil engines also brought about the necessity of strict control of the gasket thickness in order to reduce the "bumping " clearance to a minimum.
It had been found that a reduction in the amount of asbestos greatly reduced the degree of heat insulation between the cylinder head and block, and this secured better heat dissipation.
Since 1945 there had been three other major changes. The first was the use of the steel-asbestos copper gasket made on what was known as the reverse pushthrough principle. In this the steel face was employed to rim the combustion spaces and thus provide resistance to the high temperatures and pressures frequently experienced. The copper face provided a lining for the water and oil ways, thus satisfying the need to supply a gasket with slightly raised portions round the parts which required sealing, and at the same time securing relatively even thickness.
This practice was especially valuable when cylinder heads were made from aluminium alloy. The amount. of corrdsion of the aluminium head was limited, because of the small amount of copper in contact with the head. A second development was the application of a coat -of special varnish on the gasket faces, which would flow into the small irregularities in the cylinder head and blocks, and secure a good initial seal.
The third important development had been the corrugated-steel cylinder-head gasket. The corrugations enabled the asbestos to be dispensed with and manufacturing costs were much reduced.
It had virtually enabled the cylinder head and block to act as if they were one. It had eliminated the heatinsulating effect of the asbestos, the distortion-inducing effect of having a compressible layer between the joint faces, and the relative fragility of its copper and asbestos counterpart.
As a general rule, however, it was not possible to use a corrugated-steel gasket in an engine made for a metal and asbestos gasket, not only because the compression ratio would be changed, but because it would affect other features of engine design.
Piston Engine Will Stay IN his paper " Gudgeon Pin Loca1 tion," Mr. R. C. Cross, managing director of Cross Manufacturing Co.. Ltd., stated that he believed the piston engine would be the power unit in road vehicles for many years to come. It was unlikely that any new method of gudgeon-pin location would supersede those already in use
It might be that circlips would be made from alloy steels to give them greater resistance to heat forming in the engine, and the slightly increased cost would be more than compensated for by additional reliability.
Engine failures could be caused by small and often inexpensive items. The failure of the gudgeon-pin locating device could cause extensive damage to the engine. It was, therefore, necessary to ensure that this item was satisfactory in design, material and manufacture.
Allowance Too Small
I T was vital to the performance of an engine that the sealing rings fitted to wet cylinder liners should effectively prevent the leakage of coolant into the crankcase, prevent lubricating oil entering the coolant circuit and, at the same time, avoid distortion of the cylinder liner.
This was stated in a paper, Sealing Rings for Wet Cylinder Liners," prepared by Mr. J. L. Hepworth, B.Sc.(Eng.), director, Hepworth and Grandage, Ltd.
The sealing effect of the ring was caused entirely by the pressure exerted against the cylinder liner by Virtue of
its own elasticity. It was Mr. Hepworth's view that the small amount of compression recommended by the British Standards Institution was too low to permit any compensation for manufacturing errors, such as concentricity of grooves or discrepancies in the sealing rings.
Liner Vibration
Moreover, vibration of the liner in the block would produce more variation in wall pressure when using a small compression and hard rubber than with a large compression and a soft rubber. It was, therefore, thought that a minimum compression of 15 per cent. would be a much more satisfactory figure, which appeared to be borne out in practice.
A perfect ring might easily be ruined by faulty assembly. The friction between cast-iron and rubber was high and might tend to trap the ring, causing damage.
The best method of assembly was to insert the ring into a dry groove, whether in the liner or the • cylinder, and smear lightly the mating component with lubricating oil, soft, soap, or similar lubricant. The liner might then be slid into position without rotation of the rings in their grooves, It was, however, dangerous to apply extensive quantities of lubricant which would fill the grooves and distort the liner when compressed. It was assumed that the lead-in chamfer provided would be smooth and free from sharp corners.
Dirt a Major Problem
D1SCUSSING "The Design and Application of Thermostats to the Internal-combustion Engine Cooling System," Mr. S. H. Blazey, chief engineer, AC-Delco Division of GeneralMotors, Ltd., said that the wax type had gained popularity because of its insensitivity to pressure when the coolant system was pressurized. The heat transfer of the wax pellet was slower than of the vapour in the bellows-type thermostat.
Dirt which became trapped in the valve seating and increased the warming-up time of the cooling system WEIS a major problem.