TEAM WORK I 300D ECONOMY
Page 44
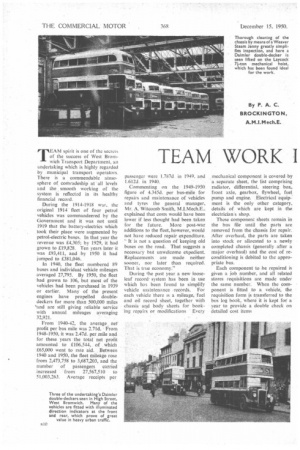
Page 45
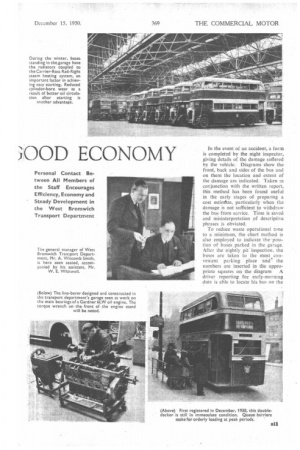
Page 46
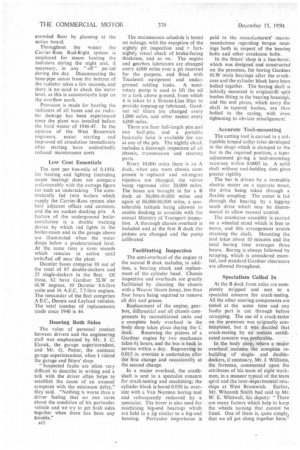
If you've noticed an error in this article please click here to report it so we can fix it.
TEAM spirit is one of the secrets of the success of West Bromwich Transport Department, an undertaking which is highly regarded by municipal transport operators_ There is a commendable atmosphere of comradeship at all levels and the smooth working of the system is reflected in its healthy financial record.
During the 1914-1918 war, the original 1914 fleet of four petrol vehicles was commandeered by the Government and it was not until 1919 that the battery-electrics which took their place were augmented by petrol-electric buses. In that year the revenue was £4,305; by 1929, it had grown to £19,828. Ten years later it was £93,411, and by 1950 it had jumped to £381,046.
In 1940, the fleet numbered 89 buses and individual vehicle mileages averaged 27,795. By 1950, the fleet had grown to 106, but most of the vehicles had been purchased in 1939 or earlier. Many of the present engines have propelled doubledeckers for more than 500,000 miles `and are still giving reliable service with annual mileages averaging 311,921.
From 1940-42, the average. net profit per bus mile was 2.71d. • Front 1948-1950, it was 2.47d. per mile and for these years the total net profit amounted to £106,544„ of . which £65,000 went to rate aid_ . Between t940 and 1950, the fleet mileage rose from 2,473,758 to 3,687,203, and the number of passengers carried increased from 27,567,510 to 51,003,263. Average receipts per passenger were 1.787d, in 1949. and 1.6121 in 1940.
Commenting on the 1949-1950 figure of 4.345d. per bus-mile for repairs and maintenance of vehicles and tyres the general manager, Mr. A. Witcomb Smith, M.I.Mech.E.. explained that costs would have been lower if less thought had been taken for the future. More post-war additions to the fleet, however, would not have reduced repair expenditure_
It is not a question of keeping old buses on the road. That suggests a necessary but unwelcome expedient. Replacements are made neither sooner, nor later than required. That is true economy."
During the past year a new looseleaf record. system has been in use which has been found to simplify vehicle maintenance records. For each vehicle there is a mileage, fuel and oil record sheet, together with chassis ani.1 body sheets for booking repairs or modifications Every mechanical component is covered by a separate sheet, the list comprising radiator, differential, steering box, front axle, gearbox, flywheel, fuel pump and engine. Electrical equipment is the only other category, details of which are kept in the electrician s shop.
These component sheets remain in the bus file until the parts are removed from the chassis for repair. After overhaul, the parts are taken into stock or allocated to a newly completed chassis (generally after a major overhaul) and the cost of reconditioning is debited to the appropriate bus.
Each component to -be repaired is given a job number, and all related stores requisitions are made under the same number, When the component is fitted to a vehicle, the requisition form is transferred to the bus log book, where it is kept for a year to provide a double check on detailed cost items In the event of an accident, a form is completed by the night inspector, giving details of the damage suffered by the vehicle. Diagrams show the front, back and sides of the bus and on them the location and extent of the damage are indicated. Taken in conjunction with the written report, this method has been found useful in the early stages of preparing a cost estimtte, particularly when the damage is not sufficient to withdraw the bus from service. Time is saved and misinterpretation of descriptive phrases is obviated.
To reduce waste operational time to a minimum, the chart method is also employed to intlicatu the position of buses parked in the gahige. After the nightly pit' inspection, the buses arc taken to the mast convenient parking • place and' the numbers are inserted in the appropriate squares on the diagram A driver reporting for early-morning duty is able to locate his bus on the
crowded floor by glancing at the notice board.
Throughout the winter the Carrier Ross Rad-Right system is employed for steam heating the radiators during the night and, if necessary, in any " off " pe: Lod during the day. Disconnecting the hose-pipe union from the bottom of the radiator takes a few seconds, and there is no need to check the water level, as this is automatically kept on the overflow mark.
Provision is made for heating the radiators of all buses and no radiator damage has been experienced since the plant was installed before the hard winter of 1946-47. In the opinion of the West Bromwich engineers, easier starting and improved oil circulation immediately after starting have undoubtedly reduced maintenance costs.
Low Cost Essentials The cost per bus-mile of 0.145d. tor heating and lighting (including steam heating) does not compare unfavourably with the average figure for such an undertaking The automatically fed twin boilers which supply the Carrier-Ross system also heat adjacent offices and canteens, and the six sunken docking pits A feature of the underground boiler installation is a double warning device by which red lights in the boiler-room and in the garage above are illuminated when the water drops below a predetermined level. At the same time a siren sounds which remains in action until switefled off near the plant.
Daimler buses comprise 83 out of the total of 87 double-deckers and 25 single-deckers he the fleet. Of these, 62 have Gardner 5LW or 61.W engines. 10 Daimler 8.6-litre units and 16 A.E.C. 7.7-litre engines. The remainder of the fleet comprises A.E.C., Dennis and Leyland vehicles. The total number of replacements made since 1940 is 44.
Hearing Both Sides The value of personal contact between drivers and the engineering staff was emphasized by Mr. J. C. Elcock, the garage superintendent, and Mr. G. Pester, the assistant garage superintendent, when I visited the garage and fitters' shop.
"Suspected faults are often very difficult to describe in writing and a talk with the driver often helps to establish the cause of an unusual symptom with the minimum delay," they said. "Nothing is worse than a driver feeling that no one cares about the condition of his particular vehicle and we try to get both sides together when there has been any trouble."
s12 The maintenance schedule is based on mileage, with the exception of the
nightly pit inspection and fortnightly visual check of brake-facing thickness, and so on. The engine and gearbox lubricants are changed every 4,000 miles over a pit reserved for the purpose, and fitted with Tecalemit equipment and underground settling tanks. A semirotary pump is used to lift the oil to a tank above ground, from which it is taken to a Stream-Line litter to provide topping-up lubricant. Gardner oil filters are changed every 1,000 miles, and other makes every
4,000 miles. .
There are four full-length pits and two half-pits. and a portable hydraulic hoist is available for use at any of the pits The nightly check includes a thorough inspection of all chassis, transmission and steering parts. Every 10,000 miles there is an A dock, when any worn chassis component is -replaced and oil-engine injectors are changed, the valves being reground after 20,000 miles. The buses are brought in for a B dock at 30,000-40,000 miles and again at 60,000-80,000 miles, a considerable latitude being allowed to enable docking to coincide with the annual Ministry of Transport inspection. A thorough chassis overhaul is included and at the first B dock the pistons are changed and the pump calibrated.
Facilitating Inspection
The semi-overhaul of the engine at the second B dock includes, in addition, a bearing check and replacement of the cylinder head. Chassis inspection and overhauls are greatly facilitated by cleaning the chassis with a Weaver Steam Jenny, less than four hours being required to remove all dirt and grease.
Replacement of the engine, gearbox, differential and all chassis cornponents by reconditioned units and a complete body overhaul in the body shop takes place during the C dock. Renewing the pistons of a Gardner engine by two mechanics takes 64 hours, and the bus is back in service within a day. Regrooving to 0.015 in, oversize is undertaken after the first change and occasionally at the second change.
In a major overhaul, the crankshaft is sent to a specialist concern for crack-testing and machining; the cylinder block is bored 0.030 in. oversize with a Van Norman boring tool and subsequently resleeved by a specialist. The borer is also used for machining big-end bearings which are held in a jig similar to a big-end housing. Particular importance is paid to the manufacturers' recommendations regarding torque readings both in respect of the bearing bolts and other crankcase bolts.
In the fitters' shop is a line-borer, which was designed and constructed on the premises, for boring Gardner 6LW main bearings after the crankcase and the cylinder block have been bolted together. The boring shaft is initially mounted in original-fit split bushes fitting in the bearing housing's. and the end plates, which carry the shift in tapered bushes, are then bolted to the casing, with even tightening to obviate misalignment
Accurate Tool-mounting
The cutting tool is carried in a collapsible hinged collar (also developed in the shop) which is clamped to the bar in the required position, a taper adjustment giving a tool-mounting accuracy within 0.0005 in. A solid shaft without tool-holding slots gives greater rigidity The bar is driven by a reversible electric motor on a separate stand, the drive being taken through a flexible coupling. The cutter is fed through the bearing by a lagging. tooth drive which may be disconnected to allow manual control.
The crankcase assembly is carried on a wheeled stand which is free to move, and this arrangement avoids straining the shaft. Mounting the tool takes about 10 minutes and the total boring time averages three hours. Boring is always followed by set aping, which is considered essential, and standard Gardner clearances are allowed throughout.
Specialists Called In At the B dock front axles are completely stripped and sent to a specialist concern for crack-testing. All the other steering components are tested at the same time and any faulty part is cut through before scrapping. The use of a crack-tester on the premises was originally contemplated, but it was decided that crack-testing by an outside certificated concern was preferable. In the body shop, where a major overhaul includes the complete rebuilding of singleand doubledeckers, if necessary, Mr. J. Williams, the foreman, commented upon the attributes of his team of eight workmen, in a manner typical of the team spirit and the inter-departmental Teleships at West Bromwich. Earlier, Mr. Witcomb Smith had said to Mr. W. E. Whitwell, his deputy: "There are many factors which help to keep the wheels turning that cannot be listed. One of them is, quite simply, that we all get along together here."