L. J. Cotton Tests A Vehicle for
Page 31
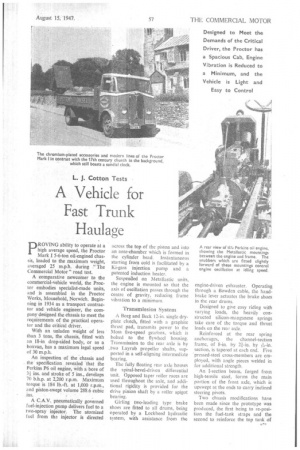
Page 32
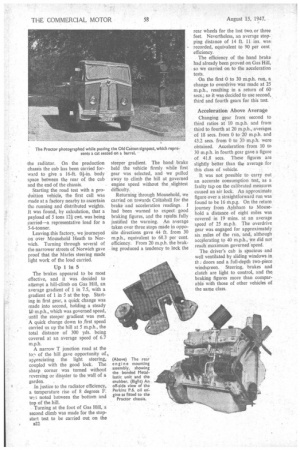
Page 33
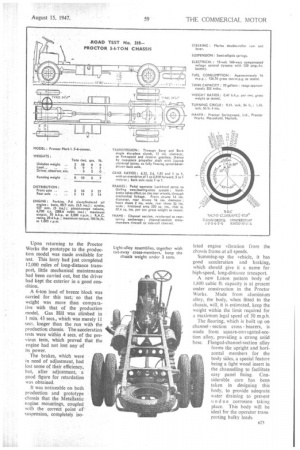
If you've noticed an error in this article please click here to report it so we can fix it.
Fast Trunk Haulage
pROVING ability to operate at a high average speed, the Proctor Mark I 5-6-ton oil-engined chassis, loaded to the maximum weight, averaged 25 m.p.h. during "The Commercial Motor" road test.
A comparative newcomer to the commercial-vehicle world, the Proctor embodies specialist-made units, and is assembled in the Proctor Works, Mousehold, Norwich. Beginning in 1934 as a transport contractor and vehicle engineer, the company designed the chassis to meet the requirements of the practical operator and the critical driver.
With an unladen weight of less ' than 3 tons, the chassis, fitted with an 18-in drop-sided body, or as a boxvan, has a maximum legal speed of 30 m.p.h.
An inspection of the chassis and the ' specification revealed that the Perkins P6 oil engine, with a-bore of 31 ins, and stroke of 5 ins., develops 70 b.h.p. at 2,200 r.p.m. Maximum torque is 184 lb.-ft. at 1,000 r.p.m., and piston-swept volume 288.6 cubic ins. .
A C.A.V. pneumatically governed fuel-injection pump delivers fuel to a two-spray injector. The atomized fuel from the injector is directed across the top of the piston and into an ante-chamber which is formed in the cylinder head. Instantaneous starting from cold is facilitated by a Ki-gass injection pump and a patented induction heater. Suspended on Metallastic units, the engine is mounted so that the axis of oscillation passes through the centre of gravity, reducing frame vibration to a minimum.
Transmission System
A Borg and Beck I2-in, single dryplate clutch, fitted with a graphite thrust pad, transmits power to the Moss five-speed gearbox, which is bolted to the flywheel housing. Transmission to the rear axle is by two Layrub propeller shafts, supported in a self-aligning intermediate bearing.
The fully floating rear axle houses the spiral-bevel-driven differential unit. Opposed taper roller races are used throughout the axle, and additional rigidity is provided for the drive pinion shaft by a roller spigot bearing.
Girling two-leading type brake shoes are fitted to all drums, being operated by a Lockheed hydraulic system, with assistance from the
engine-driven exhauster. Operating through a Bowden cable, the handbrake lever actuates the brake shoes in the rear drums.
Designed to give easy riding with varying loads, the heavily constructed silicon-manganese springs take care of the torque and thrust loads on the rear axle.
Reinforced at the rear spring anchorages, the channel-section frame, of 8-in. by 2i-in. by ?d-in. section, is tapered at each end. Five pressed-steel cross-members are employed, with angle pieces welded in for additional strength.
An I-section beam, forged front high-tensile steel, forms the main portion of the front axle, which is upswept at the ends to carry inclined steering pivots.
Two chassis modifications have
been made since the prototype was produced, the first being to re-position the fuel-tank straps and the second to reinforce the top tank of
the radiator. On the production chassis the cab has been carried forward to give a 16-ft. 01-in, body space between the rear of the cab and the end of the chassis.
Starting the road test with a production vehicle, the first call was made at a factory nearby to ascertain the running and distributed weights. It was found, by calculation, that a payload of 5 tons 124 cwt. was being carried—a representative load for a 5-6-tonner.
Leaving this factory, we journeyed on over Mousehold Heath to Norwich. Turning through several of the narrower streets of Norwich gave proof that the Manes steering made light work of the load carried.
Up 1 in 5 The brakes appeared to be most effective, and it was decided to attempt a hill-climb on Gas Hill, an average gradient of 1 in 7.5, with a gradient of 1 in 5 at the top. Starting in first gear, a quick change was made into second, holding a steady 1,0 m.p.h., which was governed speed, until the steeper gradient was met. A quick change down to first speed carried us up the hill at 5 m.p.h., the total distance of 300 yds. being covered at an average speed of 6.7 A narrow T junction road at the top of the hill gave opportunity of , appreciating the light steering, coupled with the good lock. The sharp corner was turned without reversing or disaster to the wall of a garden.
In justice to the radiator efficiency, a temperature rise of 8 degrees F. Via 7; noted between the bottom and top of the hill.
Turning at the foot of Gas Hill, a second climb was made for the stopstart test to be carried out on the steeper gradient. The hand brake held the vehicle firmly while first gear was selected, and we pulled away to climb the hill at governed engine speed without the slightest difficulty.
Returning through Mousehold, we carried on towards COltishall for the brake and acceleration readings. had been warned to expect good braking figures, and the results fully justified the warning. An average taken over three stops made in opposite directions gave 44 ft. from 30 m.p.h., equivalent to 68.3 per cent. efficiency. From 20 m.p.h. the braking produced a tendency to lock the rear wheels for the last two, or three feet. Nevertheless, an average stopping distance of 14 ft. 11 ins, was recorded, equivalent to 90 per cent efficiency.
The efficiency of the hand brake had already been proved on Gas Hill, so we carried on to the acceleration tests.
On the first 0 to 30 mph. run, a change to overdrive was made at 25 m.p.h., resulting in a return of 60 secs.; so it was decided to use second, third and fourth gears for this test.
Acceleration Above Average
Changing gear from second to third ratios at 10 m.p.h. and from third to fourth at 20 mp.h., averages of 18 secs. from 0 to 20 m.p.h. and 43.2 secs. from 0 to 30 m.p.h. were obtained. Acceleration from 10 to 30 mph. in fourth gear gave a figure of 41.8 secs. These figures are slightly better than the average for this class of vehicle.
It was not possible to carry out an accurate consumption test, as a faulty tap on the calibrated measures caused an air lock. An approximate figure over a straightforward run was found to be 16 m.p.g. On the return journey from Aylsham to Mousehold a distance of eight miles was covered in 19 mins. at an average speed of 25 m.p.h. The overdrive gear was engaged for approximately six miles of the run, and, although accelerating to 40 m.p.h., we did not reach maximum governed speed.
The driver's cab is spacious • and well ventilated by sliding windows in th..: doors and a full-depth two-piece windscreen. Steering, brakes and clutch are light to control, and the braking figures more than comparable with those of other vehicles of the same class.
Upon returning to the Proctor Works the prototype to the production model was made available for test. This lorry had just completed 12,000 miles of long-distance transport, little mechanical maintenance had been carried out, but the driver had kept the exterior in a good condition.
A 6-ton load of breeze block was carried for this test, so that the weight was more than comparative with that of the production model. Gas Hill was climbed in 1 min. 43 secs., which was merely 1I secs, longer than the run with the production chassis. The acceleration tests were within 4 secs. of the previous tests, which proved that the engine had not lost any of its power.
The brakes, which were in need of adjustment, had lost some of their efficiency, but, after adjustment, a good figure for retardation was obtained.
It was noticeable on both production and prototype chassis that the Metallastic engine mountings, coupled with the correct point of suspension, completely iso
latcd engine vibration from the chassis frame at all speeds.
Summing-up the vehicle, it has good acceleration and braking, which should give it a name for high-speed, long-distance transport.
A new Luton pattern body of 1,800 cubic ft. capacity is at present under construction in the Proctor Works. Made from aluminium alloy, the body, when fitted to the chassis, will, it is estimated, keep the weight within the limit required for a maximum legal speed of 30 m.p.h.
The flooring, which is built up on channel section cross bearers, is made from square-corrugated-section alloy, providing a strong solid base. Flanged-channel-section alloy forms the upright and horizontal members for the body sides, a special feature being a light wood insert in the channelling to facilitate easy panel fixing. Considerable care has been taken in designing this body, to provide adequate water draining to prevent undue corrosion taking place. This body will be ideal for the operator transporting bulky loads.