DENNIS ASS1 Y METHODS.
Page 12
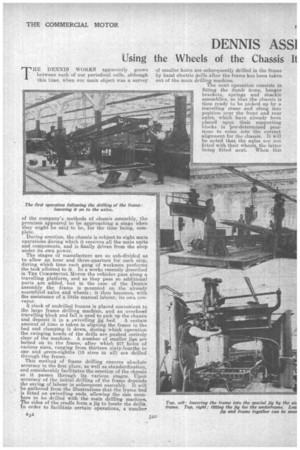
Page 13
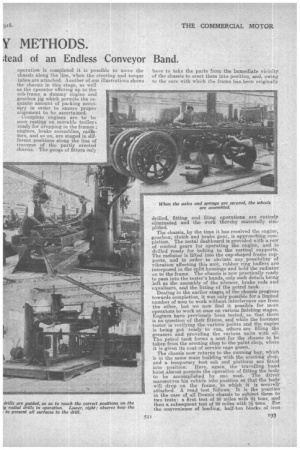
Page 14
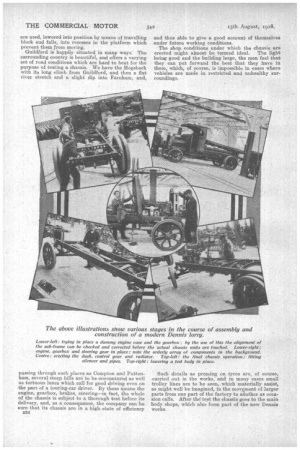
If you've noticed an error in this article please click here to report it so we can fix it.
Using the Wheels of the Chassis It tead of an Endless Conveyor Band.
THE DENNIS WORKS apparently grows between each of our periodical calls, although this time, when our main object was a survey
of the company's methods of chassis assembly, the premises appeared to be approaching a stage when they might be said to be, for the time being, complete. During erection, the chassis is subject to eight main operations during which it receives all the main units and components, and is finally driven from the shop under its own power.
The stages of manufacture are so sub-divided as to allow an hour and three-quarters for each stop, during which time each gang of workmen performs the task allotted to it. In a works recently described in THE COMMERCIAL MOTOE the vehicles pass along a travelling platform, and as they pass so additional parts are added, but in the case of the Dennis assembly the frame is mounted on the already assembled axles and wheels ; it then becomes, with the assistance of a little manual labour, its own conveyor.
A stack of undrilled frames is placed convenient to (he large frame drilling machine, and an overhead travelling block and fall is used to pick up the chassis and deposit it in a swivelling jig bed: A certain amount of time is taken in aligning the frame in the bed and clamping it down, during which operation the swinging heads of the drills are pushed entirely clear of the machine. A .number of smaller jigs are bolted on to the frame, after which 217 holes of various sizes, ranging from thirteen sixty-fourths to one and seven-eighths (15 sizes in all) are drilled through the frame.
This method of frame drilling ensures absolute smuracy in the first place, as well as standardization, and considerably facilitates the erection of the chassis as it passes through its various stages. Upon accuracy of the initial drilling of the frame depends the saving of labour in subsequent assembly. It will be gathered from the illustrations that the frame bed is fitted on swivelling ends, allowing the side members to be drilled with the main drilling machine. The sides of the cradle form a jig to locate the drills. In order to facilitate certain operations, a number Bj2
of smaller holes are subsequently drilled in the frame by hand electric drills after the frame has been taken out of the main drilling machine.
The next operation consists in fitting the dumb irons, hanger brackets, springs and shackle assemblies, so that the chassis is then ready to be picked up by a travelling crane and slung into position over the front and rear axles, which have already been placed upon their supporting blocks in Pre-determined positions to come into the correct alignment for the chassis. It will be noted that the axles are not fitted with their wheels, the latter being fitted next. When this operation is completed it is possible to move the chassis along the line, when the steering and torque tubes are attached. Another of our illustrations shows the chassis in this stage, as well as the operator offering up to the sub-frame a dummy engine andgearbox jig which permits the requisite amount of packing necessary in order to ensure proper alignment to be ascertained.
Complete engines are to be seen resting on movable trolleys ready for dropping in the frames ; engines, brake assemblies, radiators, and so on, are staged in different positions along the line of traverse of the partly erected chassis. The gangs of fitters only have to take the parts from the immediate vicinity of the chassis to erect them into position, and, owing to the care with which the frame has been originally drilled, fitting and 'filing operations are entirely eliminated and the work thereby materially simplified.
The chassis, by the time it has received the engine, gearbox, clutch and brake gear, is approaching completion. The metal dashboard is provided with a row of control gears for operating the engine, and is drilled ready for bolting to the vertical supports. The radiator is lifted into the cup-shaped frame supports, and in order to obviate any possibility of vibration affecting this unit, rubber ring buffers are interposed in the split housings and hold the radiator on to the frame. The chassis is now practically ready to pass into the tester's hands, only such details being left as the assembly of the silencer, brake rods and equalisers, and the fitting of the petrol tank.
Dealing in the earlier stages of the chassis progress towards completion, it was only possible for a limited number of men to work without interference one from the other, but we now find it possible for more operators to work at once on various finishing stages. Engines have previously been tested, so that there is no question of their fitness, and while the foreman tester is verifying the various points and the engine • is being got readyto run, others are filling the greasers and providing the various units with oil. The petrol tank forms a seat for the chassis to be taken from the erecting shop to the paint shop, where it is given its coat of service sage green.
The chassis now returns to the running bay, which is in the same main building with the erecting shoP, and a temporary test cab and platform are fitted into position. Here, again, the travelling hand hoist almost permits the operation of fitting the body to be accomplished by one man. The driver manceuvres his vehicle into position so that the body will drop on the frame, to which it is securely attached. A road test follows. It is • the practice in the case of all Dennis chassis to subject them to two tests: a first test of 30 miles with 2 tons, and then a subsequent test of 20 miles with 3f; tons. For the convenience of loading, half-ton blocks of iron are used, lowered into position by means of travelling block and falls, into recesses in the platform which prevent them from moving.
Guildford is happily situated in many ways. The surrounding country is beautiful, and 'offers a varying set of road conditions which are hard to beat for the purpose of testing a chassis. We have the Hogsback with its long climb from Guildford, and then a flat river stretch and a slight dip into Farnham, and, passing through such places as Compton and Puttenham, several steep hills are to be encountered as well as tortuous lanes which call for good driving even on the part of a touring-car driver. By these means the engine, gearbox, brakes, steering—in fact, the whole of the chassis is subject to a thorough test before its delivery, and, as a consequence, the company can be sure that its chassis are in a high state of efficiency and thus able to give a, good account of themselves under future working conditions. The shop conditions under which the chassis are erected might almost be termed ideal. The light being good and the building large, the men feel that they can put forward the best that they have in them, which, of course, is impossible in cases where vehicles are made in restricted and unhealthy surroundings.
Such details as pressing on tyres are, of course, carried out in the works, and in many cases small trolley lines are to be seen, which materially assist, as might well be imagined, in the movAment of larger parts from one part of the factory to another as occasion calls. After thd test the chassis goes to the main body shops, which also form part of the new Dennis works.