Know Your Air Brakes
Page 60
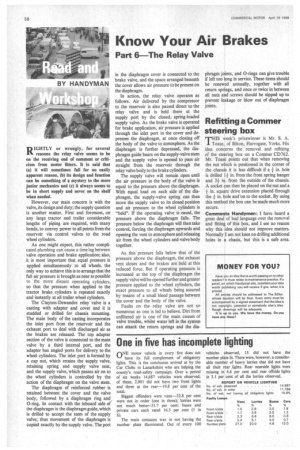
If you've noticed an error in this article please click here to report it so we can fix it.
RIGHTLY or wrongly, for several reasons the relay valve seems to be on the receiving end of comment or criticism from motor fitters. It is said that (a) it will sometimes fail for no easily apparent reason, (b) its design and function can be something of a mystery to the more junior mechanics and (c) it always seems to be in short supply and never on the shelf when needed.
However, our main concern is with the valve, its design and duty; the supply question is another matter. First and foremost, on any large tractor and trailer considerable lengths of piping are required, with many bends, to convey power to all points from the reservoir via control valves to the road wheel cylinders.
' As one might expect, this rather complicated plumbing can cause a time lag between valve operation and brake application; also, it is most important that equal pressure is applied simultaneously to all wheels, the only way to achieve this is to arrange that the full air pressure is brought as near as possible to the more distant operating cylinders. so that the pressure when applied to the tractor brake cylinders is repeated exactly and instantly at all trailer wheel cylinders.
The Clayton-Dewandre relay valve is a casting with adapter and cover and it is studded or drilled for chassis mounting. The main body of the casting incorporates the inlet port from the reservoir and the exhaust port to deal with discharged air as the brakes are released. The top adapter section of the valve is connected to the main valve by a third internal port, and the adapter has angled ports for delivery to the wheel cylinders. The inlet port is formed by a cap nut, which retains the supply valve, retaining spring and supply valve seat, and the supply valve, which passes air on to the wheel cylinders is controlled by the action of the diaphragm on the valve stem.
The diaphragm of reinforced rubber is retained between the cover and the valve body, followed by a diaphragm ring and 0-ring. In contact with the inboard side of the diaphragm is the diaphragm guide, which is drilled to accept the stem of the supply valve; thus movement of the diaphragm is copied exactly by the supply valve. The port in the diaphragm cover is connected to the brake valve, and the space arranged beneath the cover allows air pressure to be present on the diaphragm.
In action, the relay valve operates as follows. Air delivered by the compressor to the reservoir is also passed direct to the relay valve and is held there at the supply port by the closed, spring-loaded supply valve. As the brake valve is operated for brake application, air pressure is applied through the inlet port in the cover and depresses the diaphragm, at once closing off the body of the valve to atmosphere. As the diaphragm is further depressed, the diaphragm guide bears on the supply-valve stem and the supply valve is opened to pass air straight from the reservoir through the relay valve body to the brake cylinders.
The supply valve will remain open until the air pressure in the body of the valve is equal to the pressure above the diaphragm. With equal load on each side of the diaphragm, the supply-valve spring can then move the supply valve to its closed position and air pressure to the wheel cylinders is "held". If the operating valve is eased, the pressure above the diaphragm falls. The pressure below the diaphragm will then take control, forcing the diaphragm upwards and opening the vent to atmosphere and releasing air from the wheel cylinders and valve body together.
As this-pressure falls below that of the pressure above the diaphragm, the exhaust vent closes and the brakes are held at this reduced force. But if operating pressure is increased at the top of the diaphragm the supply valve will be opened further and greater pressure applied to the wheel cylinders, the exact pressure to all wheels being assured by means of a small bleed passage between the cover and the body of the valve.
Faults on the relay valve are not so numerous as one is led to believe. Dirt from unfiltered air is one of the main causes of valve trouble, whilst water left in the system can attack the return springs and the dia phragm joints, and 0-rings can give trouble if left too long in service. These items should be renewed annually, together with all return springs, and once or twice in between all nuts and screws should be nipped up to prevent leakage or blow out of diaphragm joints.