WIND TUNNEL WIZARDRY
Page 126
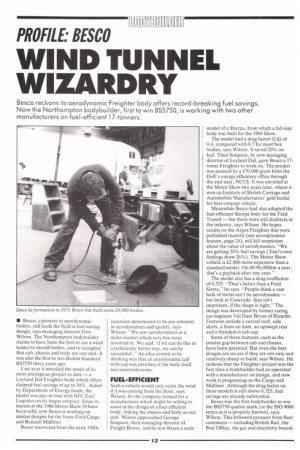
Page 127
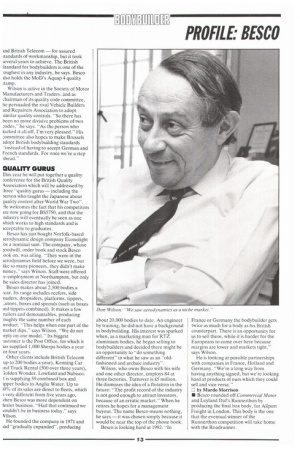
If you've noticed an error in this article please click here to report it so we can fix it.
• Besco, a pioneer in aerodynamic bodies, still leads the field in fuel-saving design, says managing director Don Wilson, The Northampton bodybuilder claims to have been the first to use a wind tunnel to mould bodies, and to recognise that cab, chassis and body are one unit. It was also the first to win British Standard BS5750 three years ago.
Last year it unveiled the result of its most prestigious project to date — a Leyland Daf Freighter body which offers claimed fuel savings of up to 30%. Aided by Department of Energy funds, the model was put on trial with NFC Exel Logistics on its Argos contract. Since its launch at the 1988 Motor Show 50 have been sold; now Besco is working on similar designs for the Iveco Ford Cargo and Renault Midliner.
Besco recovered from the early 1980s recession determined to be pre-eminent in aerodynamics and quality, says Wilson: "We saw aerodynamics as a niche market which very few were involved in. We said, `if we can do this in a technically better way, we can be successful'." An idea central to its thinking was that an aerodynamic cab with cap was pointless if the body itself was unaerodynamic.
Such a vehicle would only resist the wind if it was coming from the front, says Wilson. So the company looked for a manufacturer which might be willing to assist in the design of a fuel-efficient body, linking the chassis and body as one unit. Wilson approached George Simpson, then managing director of Freight Rover, and he lent Besco a scale model of a Sherpa, from which a full-size body was built for the 1986 Show.
The model had a drag factor (Cd) of 0.4, compared with 0.7 for most box bodies, says Wilson. It saved 20% on fuel. Then Simpson, by now managing director of Leyland Daf, gave Besco a 17tonne Freighter to work on. The project was assisted by a £70,000 grant from the DoE's energy efficiency office through the end-user, NCCS. It was unveiled at the Motor Show two years later, where it won an Institute of British Carriage and Automobile Manufacturers' gold medal for best concept vehicle.
Meanwhile Besco had also adapted the fuel-efficient Sherpa body for the Ford Transit — but there were still doubters in the industry, says Wilson. He hopes results on the Argos Freighter that were published recently (see aerodynamics feature, page 24), will kill scepticism about the value of aerodynamics. "We are getting 30% fuel savings ( Exel's own findings show 26%). The Motor Show vehicle is £2,000 more expensive than a standard model. On 80-96,000km a year, that's a payback after one year."
The model also has a drag coefficient of 0.325. "That's better than a Ford Sierra," he says. "People think a vast hulk of metal can't be aerodynamic — but look at Concorde. Size isn't important, if the shape is right." The design was developed by former racing car engineer Val Dare Bryan of Ricardo. Features include a curved roof, side skirts, a front air dam, an upswept rear and a blended-in cab cap.
Some of these features, such as the precise gap between cab and chassis, have been patented. But even the best designs are no use if they are not easy and relatively cheap to build, says Wilson. He reckons that the Freighter project was the first time a bodybuilder had co-operated with a manufacturer on design, and now work is progressing on the Cargo and Midliner. Although the drag factor on these models is still above 0.325, fuel savings are already substantial.
Besco was the first bodybuilder to win the BS5750 quality mark (or the ISO 9000 series as it is properly known), says Wilson. This followed pressure from fleet customers — including British Rail, the Post Office, the gas and electricity boards
and British Telecom — for assured aandards of workmanship, but it took ieveral years to achieve. The British standard for bodybuilders is one of the ;oughest in any industry, he says. Besco also holds the MoD's Aquap 4 quality ;tamp.
Wilson is active in the Society of Motor Manufacturers and Traders, and as chairman of its quality code committee, he persuaded the rival Vehicle Builders and Repairers Association to adopt similar quality controls. "So there has been no more divisive problems of two :odes," he says. "As the person who kicked it all off, I'm very pleased." His zommittee also hopes to make Brussels adopt British bodybuilding standards -instead of having to accept German and French standards. For once we're a step ahead."
This year he will put together a quality ::onference for the British Quality Association which will be addressed by :hree "quality gurus — including the 3erson who taught the Japanese about quality control after World War Two". He welcomes the fact that his competitors are now going for BS5750, and that the ndustry will eventually be seen as one which works to high standards and is acceptable to graduates.
Besco has just bought Norfolk-based aerodynamic design company Econolight 'or a nominal sum. The company, whose ;oodwill, order book and stock Besco ook on, was ailing. "They were in'the aerodynamics field before we were, but ike so many pioneers, they didn't make noney," says Wilson. Staff were offered .e-employment at Northampton, but only he sales director has joined.
Besco makes about 2,500 bodies a tear. Its range includes reefers, side oaders, dropsiders, platforms, tippers, ,utons, boxes and specials (such as boxes and tippers combined). It makes a few railers and demountables, producing soughly the same number of each aroduct. -This helps when one part of the narket dips," says Wilson. "We do not eply on one model." Its biggest :ustomer is the Post Office, for which it las supplied 1.000 Sherpa bodies a year or four years.
Other clients include British Telecom up to 200 bodies a year), Kenning Car Ind Truck Rental (500 over three years), 3olden Wonder, Lowfield and Nabisco. t is supplying 59 combined box and ipper bodies to Anglia Water. Up to '.0% of its sales are direct to fleets, which s very different from five years ago, vhen Besco was more dependent on lealer business. "Had that continued we wouldn't be in business today," says Vilson.
He founded the company in 1971 and lad "gradually expanded", producing about 20,000 bodies to date. An engineer by training, he did not have a background in bodybuilding. His interest was sparked when, as a marketing man for RTZ aluminium bodies, he began selling to bodybuilders and decided there might be an opportunity to "do something different" in what he saw as an "oldfashioned and archaic industry".
Wilson, who owns Besco with his wife and one other director, employs 84 at three factories. Turnover is £5 million. He dismisses the idea of a flotation in the future: "The profit record of the industry is not good enough to attract investors, because of an erratic market." When he retires he hopes for a management buyout. The name Besco means nothing, he says— it was chosen simply because it would be near the top of the phone book.
Besco is looking hard at 1992. "In France or Germany the bodybuilder gets twice as much for a body as his British counterpart. There is an opportunity for us to sell there, while it is harder for the Europeans to come over here because margins are lower and markets tight," says Wilson.
He is looking at possible partnerships with companies in France, Holland and Germany. "We're a long way from having anything signed, but we're looking hard at products of ours which they could sell and vice versa."
by Murdo Morrison
• Besco rounded off Commercial Motor and Leyland Daf's Runnerthon by producing the final box body, for Allport Freight in London. This body is the one that the eventual winner of the Runnerthon competition will take home with the Roadrunner.