'ERMINAL DELAYS COST?
Page 99
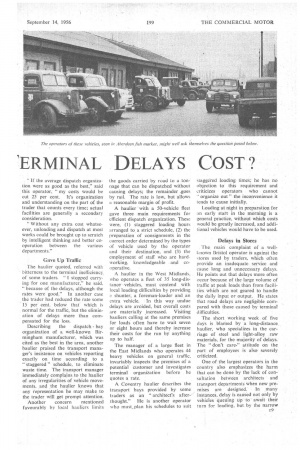
Page 100
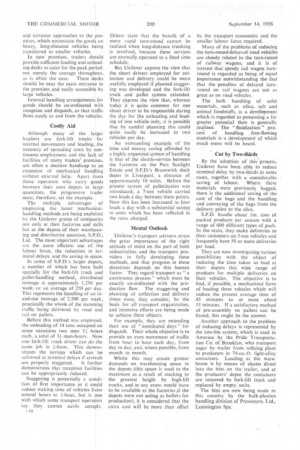
If you've noticed an error in this article please click here to report it so we can fix it.
• If the average dispatch organization were as good as the best," said this operator, "my costs would be cut 25 per cent. It's organization and understanding on the part of the trader that counts every time; actual facilities are generally a secondary consideration.
"Without any extra cost whatsoever, unloading and dispatch at most works could be brought up to scratch by intelligent thinking and better cooperation between the various departments."
Gave Up Traffic The haulier quoted, referred with bitterness to the terminal inefficiency
of some traders. I stopped carrying for one manufacturer," he said, "because of the delays, although the rates were good." In another case the trader had reduced the rate some 15 per cent below that which is normal for the traffic, but the elimination of delays more than compensated for the loss.
Describing the dispatch bay organization of a well-known Birmingham manufacturer, which was cited as the best in the area, another haulier praised the transport manager's insistence on vehicles reporting exactly on time according to a "staggered " schedule, to eliminate waste time. The transport manager immediately complains to the haulier of any irregularities of vehicle movements, and the haulier knows that any representation he may make to the trader will get prompt attention.
Another concern mentioned favourably by local hauliers limits the goods carried by road to a tonnage that can be dispatched without causing delays; the remainder ,goes by rail. The rate is low, but allows a reasonable margin of profit.
A haulier with a 50-vehicle fleet gave three main requirements for efficient dispatch organization. These were, (1) staggered loading hours arranged to a strict schedule, (2) the preparation of consignments in the correct order determined by the types of vehicle used by the operator arid their destination. and (3) the employment of staff who are hardworking, knowledgeable • and co operative.
A haulier in the West Midlands, who operates a fleet of 35 long-distance vehicles, must contend with local loading difficulties by providing a shunter, a foreman-loader and an extra vehicle. In this way undue delays are avoided, but overall costs are materially increased. Visiting hauliers calling at the same premises for loads often have to wait seven or eight hours and thereby increase their costs for the run by anything up to half.
The manager of a large fleet in the East Midlands who operates 44 heavy vehicles on general traffic, invariably inspects the premises of a potential customer and investigates terminal organization before he quotes a rate.
A Coventry haulier describes the transport bays provided by some tiaders as an "architect's after-thought." He is another operator who must, plan his schedules to suit staggered loading times; he has no objection to this requirement and criticizes operators who cannot organize out" the inconvenience it tends to cause initially.
Loading at night in preparation for an early start in the morning is a general practice, without which costs would be greatly increased, and additional vehicles would have to be used.
Delays in Stores
The main complaint of a wellk nown Bristol operator is against the stores used by traders, which often provide an inadequate service and cause long and unnecessary delays. He points out that delays more often occur because of the large volume of traffic at peak loads than from facilities which are not geared to handle the daily input or output. He states that road delays are negligible compared with those caused by terminal difficulties.
The short working week of five days is blamed by a long-distance haulier, who specializes in the carriage of steel and light-alloy raw materials, for the majority of delays.. The " don't care." attitude On the part of employees is also severely criticized.
One of the largest operators in the country also emphasizes the harm that can be done by the lack of consaltation between architects and transport departments when new premises are designed. In many instances, delay is caused not only by vehicles quelling Up to await their turn for loading, but by the narrow and tortuous approaches to the premises, which necessitate the good S on heavy, long-distance vehicles Wng transferred to smaller vehicles, In new premises, traders should provide sufficient loading and unloading decks to cater for the peak period. not merely the average throughout, as is often the case. These decks should be near the main entrance to the premises and easily accessible by large vehicles.
Internal handling arrangements for goods should be co-ordinated with reception and dispatch, so that traffic flows easily to and from the vehicles.
Costly Aid
Although many of the larger hauliers use fork-lift trucks for internal movements and loading, the necessity of spreading costs by continuous employment and the lack of facilities of many traders' premises, are often a decisive handicap to an extension of mechanical handling without external help. Apart from those operators who carry goods between their own depots in large quantities, the progressive trader must, therefore, set the example.
The multiple advantages of employing the latest mechanicalhandling methods are being exploited by the Unilever group of companies not only at their factories and mills but at the depots of their warehousing and distributive associate, S.P.D., Ltd. The most important advantages are the more efficient use of the labour force, the reduction in terminal delays, and the saving in space.
In some of S.P.D.'s larger depots, a number of which has been built specially for the fork-lift truck and pallet-handling method, distributed tonnage is approximately 1,250 per week, or an average of 250 per day. This represents the handling of an inand-out tonnage of 2,500 per week, practically the whole of the incoming traffic being delivered by road and rail on pallets.
Before this method was employed, the unloading of 14 tons occupied on some occasions two men 11 hours each, a total of 3-1 man-hours. Now one fork-lift truck driver can do the same job in +-hour. This demonstrates the savings which can be achieved in terminal delays if arrivals are properly staggered. It further demonstrates that reception facilities can be appropriately reduced.
Staggering is potentially a condition of first importance as it could reduce waiting time of vehicles from several hours to +-hour, but is one with which some transport operators say they cannot easily comply.
1-10
Others state that the benefit of a more rapid turn-round cannot be realized when long-distance trunking is involved, because these services are normally operated to a fixed time schedule.
But Unilever express the view that the shunt drivers employed for collection and delivery could be more usefully employed if planned staggering was developed and the fork-lift truck and pallet system extended. They express the view that, whereas today it is quite common for one shunt driver to be responsible during the day for the unloading and loading of one vehicle only, it is possible that by careful planning this could quite easily •be increased to two vehicles per day.
An outstanding example of the time and money saving afforded by a highly organized system of handling is that of the shuttle-service between the factories on the Port Sunlight Estate and S.P.D.'s Brunswick dock depot in Liverpool, a distance of approximately 10 mile's. Before the present system of palletization was introduced, a 7-ton vehicle carried two loads a day between these points. Now this has been increased to four loads a day with a substantial saving in costs which has been reflected in the rates charged.
Mental Outlook Unilever's transport advisers stress the great importance of the right attitude of mind on the part of both industrialists and the transport providers in fully developing these methods, and that progress in these directions depends on this human factor. They regard transport as "a continuous process" which must be exactly co-ordinated with the production flow. The staggering and planning of collection and delivery times must, they consider, be the basis for all transport organization, and intensive efforts are being made to achieve these objects.
For example, they are extending their use of "nominated days" for dispatch. Their whole objective is to provide an even movement of traffic from hour to hour each day, from day to day, and, where possible, from month to month.
Whilst this may create greater demands on warehousing space in the depots (this space is used to the maximum as a result of stacking to the greatest height by high-lift trucks, and in any event would have to be available at the factories if the depots were not acting as buffers for production), it is considered that the extra cost will be more than offset by the transport economics and the smaller labour force required.
Many of the problems of reducing the turn-round delays of road vehicles are closely related to the turn-round of railway wagons, and it is of interest that speedy rail wagon turnround is regarded as being of equal importance notwithstanding the fact that the penalties of delayed turnround on rail wagons are not as great as on road vehicles, The bulk handling of solid materials, such as silica, salt and animal foodstuffs, is a development which is regarded 'as possessing a far greater potential than is generally realized. The " fluidization " process of handling free-flowing materials is a development of which much more will be heard.
Cut by Two-thirds By the adoption of this process, Unilever have been able to reduce terminal delay by two-thirds in some cases, together with a considerable saving of labour. Where these materials were previously bagged, there is the additional saving of the cost of the bags and the handling and conveying of the bags from the delivery point to the silos.
S.P.D. handle about Im. tons of packed products per annum with a range of 600 different types of pack. In the main, they make deliveries to their customers on 5-ton vehicles and frequently have 50 or more deliveries per load.
They are now investigating various possibilities with the object of reducing the time taken to load at their depots this wide range of products for multiple deliveries on their vehicles. The objective is to find, if possible, a mechanized form of loading these vehicles which will reduce the present average time of 45 minutes to at most about 15 minutes. If a satisfactory method of pre-assembly on pallets can be found, this might be the answer.
Another approach to the problem of reducing delays is represented by the tote-bin system, which is used in America by the Pride Transportation Co. of Brooklyn, who transport sugar by trailer from refining plant to producers in 74-cu.-ft. light-alloy containers. Loading at the warehouse is by means of chutes direct into the bins on the trailer, and at the producers' depot the containers are removed by fork-lift truck and replaced by empty units.
The bins are now being made in this country by the bulk-plastics handling division of Pressoturn, Ltd., Leamington Spa.