Tipping gear manufacturers are going through a period of consolidation,
Page 34
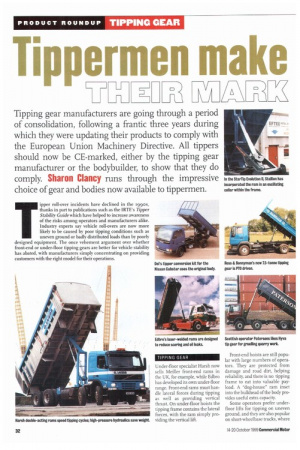
Page 35
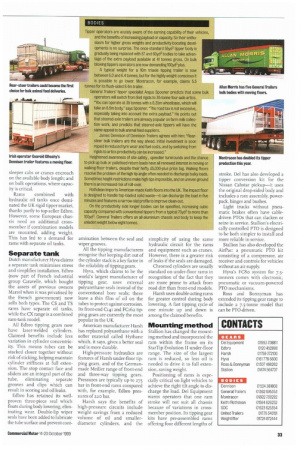
If you've noticed an error in this article please click here to report it so we can fix it.
following a frantic three years during which they were updating their products to comply with the European Union Machinery Directive. All tippers should now be CE-marked, either by the tipping gear manufacturer or the bodybuilder, to show that they do comply. Sharon Clancy runs through the impressive choice of gear and bodies now available to tippermen.
Tipper roll-over incidents have declined in the 1990s, thanks in part to publications such as the IRTE's Tipper Stability Guide which have helped to increase awareness of the risks among operators and manufacturers alike. Industry experts say vehicle roll-overs are now more likely to be caused by poor tipping conditions such as uneven ground or badly distributed loads than by poorly designed equipment. The once vehement argument over whether front-end or under-floor tipping gears are better for vehicle stability has abated, with manufacturers simply concentrating on providing customers with the right model for their operations.
TIPPING GEAR
Under-floor specialist Harsh now sells Meiller front-end rams in the UK, for example, while Edbro has developed its own under-floor range. Front-end rams must handle lateral forces during tipping as well as providing vertical thrust. On under-floor hoists the tipping frame contains the lateral forces, with the ram simply providing the vertical lift.
Front-end hoists are still popular with large numbers of operators. They are protected from damage and road dirt, helping reliability, and there is no tipping frame to eat into valuable payload. A "dog-house" ram inset into the bulkhead of the body provides useful extra capacity.
Some operators prefer underfloor lifts for tipping on uneven ground, and they are also popular on short-wheelbase trucks, where
sleeper cabs or cranes encroach on the available body length; and on bulk operations, where capacity is critical.
Rams combined with hydraulic oil tanks once dominated the UK rigid tipper market, thanks partly to top-seller Edbro. However, some European chassis need an additional crossmember if combination models are mounted, adding weight. This has led to a demand for rams with senarale oil tanks.
Separate tank
Dutch manufacturer Hyva claims a separate tank minimises stress and simplifies installation. Edbro (now part of French industrial group Caravelle, which bought the assets of previous owners Marrel when it was privatised by the French government) now sells both types. The CS and TS rams have separate oil tanks, while the CX range is a combined ram-tank model.
All Edbro tipping gears now have laser-welded cylinders. Claimed benefits include less variation in cylinder concentricity. This means tubes can be stacked closer together without risk of sticking, helping maintain cylinder stiffness at full extension. The stop contact face and sliders are an integral part of the tube, eliminating separate grooves and clips which can result in scoring and oil leaks.
Edbro has retained its wellproven three-piece seal which floats during body lowering, eliminating wear. Double-lip wiper seals have been added to lubricate the tube surface and prevent cont
amination between the seal and wiper grooves.
All the tipping manufacturers recognise that keeping dirt out of the cylinder stack is a key factor in the reliability of tipping gears.
Hyva, which claims to be the world's largest manufacturer of tipping gear, uses external polyurethane seals instead of the conventional bore seals; these leave a thin film of oil on the tubes to protect against corrosion. Its front-end Ci4i and FC162 tipping gears are currently the most popular in the UK.
American manufacturer Harsh has replaced polyurethane with a softer material called Hythane which, it says, gives a better seal and is more durable.
High-pressure hydraulics are features of Harsh under-floor tipping gears, and of the Germanmade Meiller range of front-end and three-way tipping gears. Pressures are typically up to 275 bar in front-end rams compared with, for example, Edbro pressures of 220 bar.
Harsh says the benefits of high-pressure circuits include weight savings from a reduced volume of oil and smallerdiameter cylinders, and the simplicity of using the same hydraulic circuit for the rams and equipment such as cranes. However, there is a greater risk of leaks if the seals are damaged.
Chromed cylinders are usually standard on under-floor rams in recognition of the fact that they are more prone to attack from road dirt than front-end models.
Harsh uses double-acting rams for greater control during body lowering. A fast tipping cycle of one minute up and down is among the daimed benefits.
Mounting method
Stallion has changed the mounting method and incorporated the ram within the frame on its StarTip Evolution II under-floor range. The size of the largest ram is reduced, so less oil is needed to drive it to full extension, saving weight.
Positioning of rams is especially critical on light vehicles to achieve the right tilt angle to discharge the load. Del Equipment warns operators that one ram stroke will not suit all chassis because of variations in crossmember position. Its tipping gear kits have pre-assembled rams offering four different lengths of
stroke. Del has also developed a tipper conversion kit for the Nissan Cabstar pickup—it uses the original drop-sided body and includes a ram assembly, power. pack, hinges and bushes.
Light trucks without pneumatic brakes often have cabledriven PTOs that can slacken or seize in service. Stallion's electrically controlled PTO is designed to be both simpler to install and more reliable in service.
Stallion has also developed the AirPac: a pneumatic PTO kit consisting of a compressor, air receiver and controls for vehicles without an air supply.
Hyva's I:0o system for 7.5tonners comes with electronic, pneumatic or vacuum-powered PTO mechanisms.
Ross and Bonnyman has extended its tipping gear range to include a 7.5-tonne model that can be PTO-driven.
BODIES
Tipper operators are acutely aware of the earning capability of their vehicles, and the benefits of increasing payload or capacity. So their enthusiasm for higher gross weights and productivity-boosting developments is no surprise. The once-standard 55yd3 tipper body is gradually being replaced with 57 and 60yd3 bodies to take advantage of the extra payload available at 41 tonnes gross. On bulk blowing tippers operators are now demanding 100yd3 plus.
A typical weight for a 10m triaxle tipping trailer is now between 6.0 and 6.4 tonnes, but for the highly weight-conscious it is possible to go lower. Montracon, for example, claims 5.5 tonnes for its flush-sided 9.4m trailer.
General Trailers' tipper specialist Angus Spooner predicts that some bulk operators will switch from 8x4 rigids to 35-tonne four-axle artics. You can operate at 35 tonnes with a 6.35m wheelbase, which will take an 8.5m body," says Spooner. "The road tax is not excessive, especially taking into account the extra payload." He points out that steered-axle trailers are already popular on farm milk collection work, and predicts that steered-axle tippers will have the same appeal to bulk animal feed suppliers.
James Dennison of Dennison Trailers agrees with him: "Rearsteer bulk trailers are the way ahead. Initial investment is soon repaid in reduced tyre wear and fuel costs, and by switching from rigids to artics productivity can be increased."
Heightened awareness of site safety, speedier turnrounds and the chance to pick up bulk or palletised return loads have all renewed interest in moving or walking-floor trailers, despite their hefty 15,000-plus price tag. Walking floors resolve the problem of the high tip angle often needed to discharge bulky loads. Sometimes height restrictions make high tips impossible, and on uneven ground there is an increased risk of roll-over.
Rothdean imports American-made Keith floors into the UK. The Impact floor is designed to handle top-loaded solid waste—it can discharge the load in five minutes and features a narrow-slat profile to improve clean-out.
On the productivity side longer bodies can be specified, increasing cubic capadty compared with conventional tippers from a typical 70yd3 to more than 100yd3. General Trailers offers an all-aluminium chassis and body to keep the unladen weight below eight tonnes.