/ KEEPING 7 THEM RUNNING
Page 73
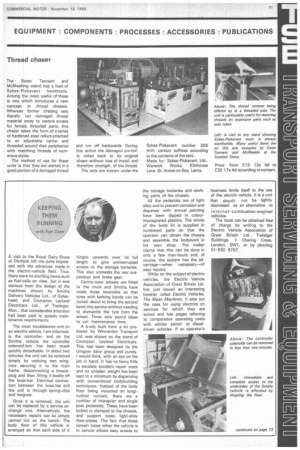
If you've noticed an error in this article please click here to report it so we can fix it.
\ with Ron Cater • A visit to the Royal Dairy Show at Olympia left me quite impressed with the advances made in the electric-vehicle field. True, there were no startling items such as fuel-cells on view, but it was obvious from the design of the machines shown by Smiths Delivery Vehicles Ltd.. of Gateshead, and Crompton Leyland Electricars Ltd., of Tredegar, Mon., that considerable attention had been paid to speedy maintenance requirements.
The most troublesome unit on an electric vehicle. I am informed, is the controller, and on the Smiths vehicle the controller solenoid-box has been made quickly detachable. In about two minutes the unit can be removed simply by undoing two wingnuts securing it to the main frame, disconnecting a breezeplug and then lifting it bodily off the buss-bar. Electrical connection between the buss-bar and the unit is through spring-clips and tongues.
Once it is removed, the unit can be replaced by a service exchange one. Alternatively, the necessary repairs can be simply carried out on the bench. The body floor of this vehicle is arranged so that each side of it hinges upwards over its full length to give uninterrupted access to the storage batteries. This also unmasks the rear suspension and brake gear.
Centre-nave wheels are fitted to the truck and Smiths have made these reversible so that tyres with kerbing bands can be turned about to bring the second band into service without needing to dismantle the tyre from the wheel. Three very sound ideas to cut maintenance time.
A body built from a kit produced by Wincanton Transport Ltd. was shown on the stand of Crompton Leyland Electricars. This had been designed by the Unigate dairy group and purely. I would think, with an eye on the job in hand. It has no fancy frills to escalate accident repair costs and its unladen weight has been kept to a minimum by dispensing with conventional bodybuilding techniques. Instead of the body floor being mounted on longitudinal runners, there are a number of triangular and single post pedestals. These have been bolted or clamped to the chassis, and support loose, light-alloy floor-plates. The fact that these remain loose when the vehicle is in service allows easy access to the storage batteries and working parts of the chassis.
All the pedestals are of light alloy and to prevent corrosion and dispense with annual painting have been dipped in colourimpregnated plastics. The whole of the body kit is supplied in numbered parts so that the operator can obtain the chassis and assemble the bodywork in his own shop. The maker claims that this can be done in only a few man-hours and, of course, the system has the advantage—when necessary—of easy repairs.
While on the subject of electric vehicles, the Electric Vehicle Association of Great Britain Ltd. has just issued an interesting booklet called Electric Vehicles, The Mean Machines. It sets out the case for using electrics on services for which they are suited and has pages referring to comparative operating costs with similar petrolor dieseldriven vehicles. If an operator's business lends itself to the use of the electric vehicle, it is a unit that should not be lightly dismissed as an alternative to internal-combustion-engined vehicles.
The book can be obtained free' of charge by writing to the Electric Vehicle Association of Great Britain Ltd., Trafalgar Buildings. 1 Charing Cross, London, SW1, or by phoning 01-930 6757.