MODERN METHODS OF PISTON-RING PRODUCTION.
Page 28
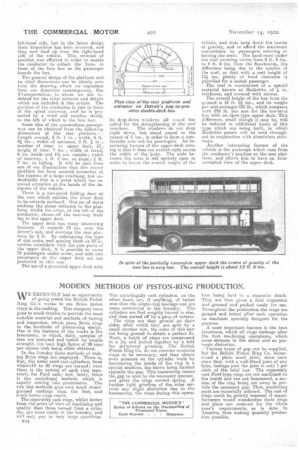
If you've noticed an error in this article please click here to report it so we can fix it.
WE RECENTLY had. an opportunity of going round the British Piston Ring Co.'s works to see Brim piston rins.s in the making. This company have gone to much trouble to provide the most suitable material and methods of ,testing and inspection, which place Brico rings in the forefront of piston-ring design. One of the features of the works is the laboratory, in which, daily, samples of iron are analysed and tested for tensile strength, the very high figure of 20 tons' per squa4e inch being often obtained.
In the foundry three methods of making Brice rings are employed. There is, first, the usual sand-cast cylinders, from whichi12 to 30 rings are turned; next there is the casting of each ring separately for Ford cars; and, lastly, there is the centrifugal method, which is rapidly coming into prominence. The two last methods give very much closergrained 'castings than the first, arid much better rings result. The separately cast rings, whilst better from the point of view of machining and quality than those turned from cylinder, are more -costly in the foundry, and will only pay in very large quantities.
1344 The centrifugally cast cylinders, on the other hand, are, if anything, of better iron than the single-ring castings and are More economical in the foundry. The cylinders are first roughly turned to Size, and then parted off by a gang of cutters.
The rings are then ground on their sides, after which they are split by a small circular saw, the sides of this saw Cut being ground to obtain a perfect fit. Next, a batch of rings are compressed in a jig and locked together by a bolt for peripheral grinding. The British Piston Ring Co. do not consider eccentric rings to be necessary, and they obtain even pressure on the cylinder walls by hammering the inside of the ring in a special machine, the blows being hardest opposite the gap. This hammering causes the gap to open to the necessary amount,. and gives the rings correct spring. A further light grinding of the sides 00rrecta any slight distortion due to the hammering, the rings during this opera tion being held 'in a magnetic chuck. They are then given a final inspection and greased and packed ready for use. Throughout the prbduction the rings are gauged and tested after each operation on machines specially designed for the purpose.
A meat important feature is the heat treatment, which all rings undergo after the first machining operations, which eases stresses in the metal and so prevents distortion.
Various types of gap can be supplied, butthe British Piston Ring Co. recomstend a plain scarf joint, since tests show that, with a well-fitted joint of any type,-leakage past the joint is only 1 per cent. of the total loss. The separately cast Ford-type rings are not machined on the inside and are not hammered, a section of the ring being cut away to provide the necessary gap. Thus, machining. costs are materially reduced. The cost of rings could be greatly lessened if manufacturers would standardize their rings and place one contract for the whole year's requirements, as is done in America, thus making quantity production possible.