C l i o % AND
Page 146
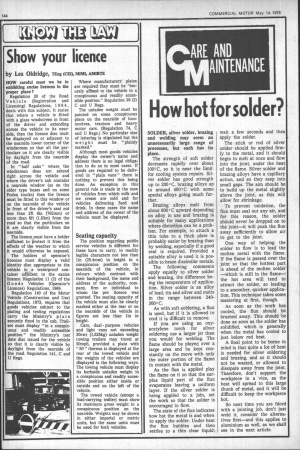
If you've noticed an error in this article please click here to report it so we can fix it.
AINTENANCE ow hot for solder?
SOLDER, silver solder, brazing and welding may seem an unnecessarily large range of processes, but each has its place.
The strength of soft solder decreases rapidly over about 100°C, so it is near the limit for cooling system repairs. Silver solder has good strength up to 200°C, brazing alloys up to around 400°C with some special alloys going much further.
Brazing alloys melt from about 600.0 upward depending on alloy in use and brazing is suitable for many applications where distortion can be a problem. For example, to attach a thin tube to a thick plate is probably easier by brazing than by welding, especially if a good seal is required. Provided a suitable alloy is used it is possible to braze dissimilar metals.
The following comments apply equally to silver solder and brazing, the difference being the temperature of application. Silver solder is an alloy of lead, tin and silver and melts in the range between 240300°C.
As with soft soldering, a flux is used, but if it is allowed to cool it is difficult to remove.
If you are using an oxyacetylene torch for silver soldering use a larger jet than you would for welding. The flame should be played over a large area and be kept constantly on the move with only the outer portion of the flame in contact with the metal.
As the flux is applied play the flame on it so that the surplus liquid part of the flux evaporates leaving a uniform layer. If the silver solder is being applied to a join, set the work so that the solder is encouraged to flow.
The state of the flux indicates how hot the metal is and when to apply the solder. Under heat the flux bubbles and then settles to a thin clear liquid; wait a few seconds and then apply the solder.
The stick or rod of silver solder should be applied firmly to the metal, and it should begin to melt at once and flow into the joint, under the heat of the flame. Silver solder and brazing alloys have a capillary action, and so they seep into small gaps. The aim should be to build up the metal slightly above the joint, as this will allow for shrinkage.
To prevent oxidation, the flux must seal out any air, and for this reason, the solder should never be dropped on to the joint—it will push the flux away sufficiently to allow air to get to the joint.
One way of helping the solder to flow is to lead the molten metal with the flame. If the flame is passed over the joint so that the hottest part is ahead of the molten solder —which is still in the flame— the hot area will tend to attract the solder, so leading to a smoother, quicker application. This technique takes some mastering at first, though.
As soon as the work has cooled, the flux should be brushed away. This should be done as soon as the solder has solidified, which is generally when the metal has cooled to just below red heat.
A final point to be borne in mind is that quite a lot of heat is needed for silver soldering and brazing, and so it should not be wasted, or allowed to dissipate away from the joint. Therefore, don't support the workpiece in a vice, as the heat will spread to this large Chunk of metal, and it will be difficult to keep the workpiece hot.
So next time you are faced with a jointing job, don't just weld it, consider the alternatives first—and this applies to aluminium as well, as we shall see in the next article.