Northwest Gas
Page 53
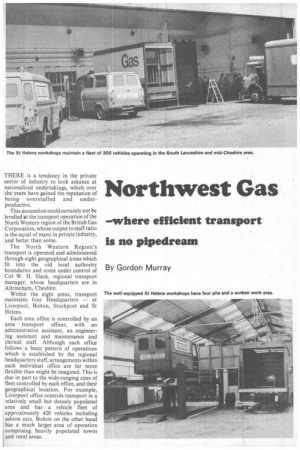
Page 54
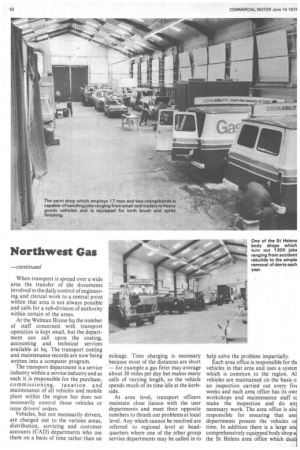
Page 55
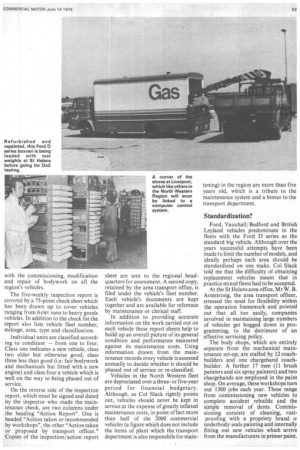
Page 56
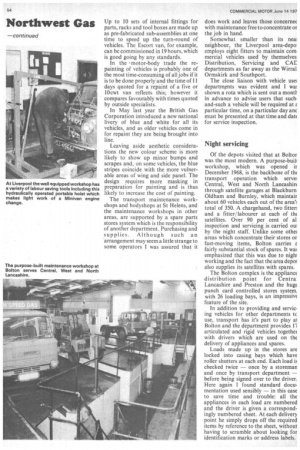
If you've noticed an error in this article please click here to report it so we can fix it.
-where efficient transport is no pipedream
By Gordon Murray
When transport is spread over a wide area the transfer of the documents involved in the daily control of engineering and clerical work to a central point within that area is not always possible and calls for a sub-division of authority within certain of the areas.
At the Welman House hq the number of staff concerned with transport operation is kept small, but the department can call upon the costing, accounting and technical services available at hq. The transport costing and maintenance records are now being written into a computer program. The transport department is a service industry within a service industry and as such it is responsible for the purchase, commissioning, taxation and maintenance of all vehicles and mobile plant within the region but does not necessarily control those vehicles or issue drivers' orders.
Vehicles, but not necessarily drivers, are charged out to the various areas, distribution, servicing and customer accounts (CAD) departments who use them on a basis of time rather than on mileage. Time charging is necessary because most of the distances are short — for example a gas fitter may average about 30 miles per day but makes many calls of varying length, so the vehicle spends much of its time idle at the kerbside.
At area level, transport officers maintain close liaison with the user departments and meet their opposite numbers to thrash out problems at local level. Any which cannot be resolved are referred to regional level at headquarters where one of the other group service departments may be called in to help solve the problem impartially.
Each area office is responsible for tht vehicles in that area and uses a systerr which is common to the region. Al vehicles are maintained on the basis o: an inspection carried out every fivt weeks and each area office has its owr workshops and maintenance staff make the inspection and do an necessary work. The area office is als responsible for ensuring that use departments present the vehicles o time. In addition there is a large an comprehensively equipped body shop a the St Helens area office which deal with the commissioning, modification and repair of bodywork on all the region's vehicles.
The five-weekly inspection report is covered by a 75-point check sheet which has been drawn up to cover vehicles ranging from 6 cwt vans to heavy goods vehicles. In addition to the check list the report also lists vehicle fleet number, mileage, area, type and classification.
Individual units are classified according to condition — from one to four. Class one indicates a new vehicle, class two older but otherwise good, class three less than good (i.e. fair bodywork and mechanicals but fitted with a new engine) and class four a vehicle which is well on the way to being phased out of service.
On the reverse side of the inspection report, which must be signed and dated by the inspector who made the maintenance check, are two columns under the heading "Action Report". One is headed "Action taken or recommended by workshops", the other "Action taken or proposed by transport officer." Copies of the inspection/action report sheet are sent to the regional headquarters for assessment. A second copy, retained by the area transport office, is filed under the vehicle's fleet number. Each vehicle's documents are kept together and are available for reference by maintenance or clerical staff.
In addition to providing accurate information on the work carried out on each vehicle these report sheets help to build up an overall picture of its general condition and performance measured against its maintenance costs. Using information drawn from the maintenance records every vehicle is assessed annually to decide whether it should be phased out of service or re-classified.
Vehicles in the North Western fleet are depreciated over a threeor five-year period for financial budgetary. Although, as Col Slack rightly points out, vehicles should never be kept in service at the expense of greatly inflated maintenance costs, in point of fact more than half of the 2000 commercial vehicles (a figure which does not include the items of plant which the transport department is also respons bile for main tening) in the region are more than five years old, which is a tribute to the maintenance system and a bonus to the transport department.
Standardization?
Ford, Vauxhall/ Bedford and British Leyland vehicles predominate in the fleets with the Ford D series as the standard big vehicle. Although over the years successful attempts have been made to limit the number of models, and ideally perhaps each area should be standardized on one make, Col Slack told me that the difficulty of obtaining replacement vehicles meant that in practice mixed fleets had to be accepted.
At the St Helens area office, Mr W. B. Armstrong, the area transport officer, stressed the need for flexibility within the operation framework and pointed out that all too easily, companies involved in maintaining large numbers of vehicles get bogged down in programming, to the detriment of an effective servicing policy.
The body shops, which are entirely separate from the mechanical maintenance set-up, are staffed by 12 coachbuilders and one chargehand coachbuilder. A further 17 men (11 brush painters and six spray painters) and two chargehands are employed in the paint shop. On average, these workshops turn out 1300 jobs each year. These range from commissioning new vehicles to complete accident rebuilds and the simple removal of dents. Commissioning consists of cleaning, rustproofing with a propriety brand 01 underbody seals painting and internally fitting out new vehicles which arrive from the manufacturers in primer paint. Up to 10 sets of internal fittings for parts, racks and tool boxes are made up as pre-fabricated sub-assemblies at one time to speed up the turn-round of vehicles. The Escort van, for example, can be commissioned in 19 hours, which is good going by any standards.
In the 'motor-body trade the repainting of vehicles is probably one of the most time-consuming of all jobs if it is to be done properly and the time of 11 days quoted for a repaint of a five or lOcwt van reflects this; however it compares favourably with times quoted by outside specialists.
In May last year the British Gas Corporation introduced a new national livery of blue and white for all its vehicles, and as older vehicles come in for repaint they are being brought into line.
Leaving aside aesthetic considerations the new colour scheme is more likely to show up minor bumps and scrapes and, on some vehicles, the blue stripes coincide with the more vulnerable areas of wing and side panel. The design requires more masking in preparation for painting and is thus likely to increase the cost of painting.
The transport maintenance workshops and bodyshops at St Helens, and the maintenance workshops in other areas, are supported by a spare parts stores system which is the responsibility of another department. Purchasing and supplies. Although such an arrangement may seem a little strange to some operators I was assured that it does work and leaves those concernec with maintenance free to concentrate or the job in hand.
Somewhat smaller than its new neighbour, the Liverpool area-depo. employs eight fitters to maintain corn. mercial vehicles used by themselves Distribution, Servicing and CAE departments as far away as the Wirral Ormsk irk and Southport.
The close liaison with vehicle usei departments was evident and I wa! shown a rota which is sent out a mond in advance to advise users that such' and-such a vehicle will be required at particular time, on a particular day anc must be presented at that time and date for service inspection.
Night servicing
Of the depots visited that at Boltor was the most modern. A purpose-buili workshop, which was opened ir December 1968, is the backbone of the transport operation which serve! Central, West and North Lancashire through satellite garages at Blackburn Oldham and Burnley, which maintair about 60 vehicles each out of the area' total of 350. A chargehand, two fitter: and a fitter/ labourer at each of the satellites. Over 90 per cent of al inspection and servicing is carried oui by the night staff. Unlike some othei areas which concentrate their stores or fast-moving items, Bolton carries 2 fairly substantial stock of spares. It wa5. emphasized that this was due to nighi working and the fact that the area depoi also supplies its satellites with spares.
The Bolton complex is the appliance distribution point for Centra' Lancashire and Preston and the huge punch card controlled stores system, with 26 loading bays, is an impressive feature of the site.
In addition to providing and servicing vehicles for other departments tc use, transport has it's part to play al Bolton and the department provides fl articulated and rigid vehicles togethei with drivers which are used on the delivery of appliances and spares.
Loads made up in the stores are locked into casing bays which have roller shutters at each end. Each load checked twice — once by a storeman and once by transport department — before being signed over to the driver. Here again I found standard documentation used sensibly — in this case to save time and trouble: all the appliances in each load are numbered and the driver is given a correspondingly numbered sheet. At each delivery point he simply drops off the required items by reference to the sheet, without having to scramble about looking for identification marks or address labels.