LIGHT-ALLC BRICK-BOD REDUCES DAMAGE
Page 64
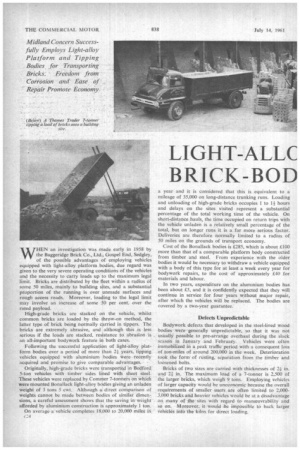
Page 65
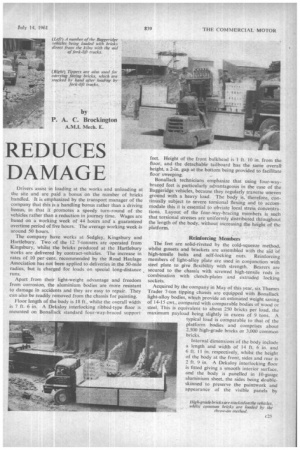
Page 66
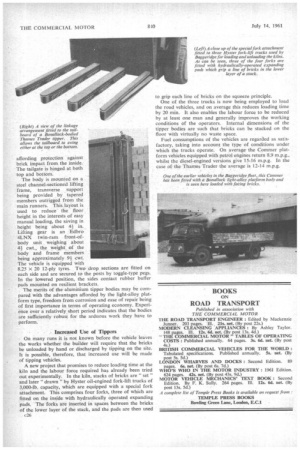
If you've noticed an error in this article please click here to report it so we can fix it.
by P. A. C. Brockington
A.M.I. Mech. E.
WHEN an investigation was made early in 1958 by the Baggeridge Brick Co., Ltd., Gospel End, Sedgley, of the possible advantages of employing vehicles equipped with light-alloy platform bodies, due regard was given to the very severe operating conditions of the vehicles and the necessity to carry loads up to the maximum legal limit. Bricks are distributed by the fleet within a radius of some 50 miles, mainly to building sites, and a substantial proportion of the running is over unmade surfaces and rough access roads. Moreover, loading to the legal limit may involve an increase of some 50 per cent. over the rated payload.
High-grade bricks are stacked on the vehicle, whilst common bricks are loaded by the throw-on method, the latter type of brick being normally carried in tippers. The bricks are extremely abrasive, and although this is less serious if the loads are stacked, resistance td abrasion is an all-important bodywork feature in both cases:
Following the successful application of light-alloy platform bodies over a period of more than 21 years, tipping vehicles equipped with aluminium bodies were recently acquired and promise to give comparable advantages.
Originally, high-grade bricks were transported in Bedford 5-ton vehicles with timber sides lined with sheet steel. These vehicles were replaced by Commer 7-tonners on which were mounted Bonallack light-alloy bodies giving an unladen weight of 3 tons 5 cwt. Although a direct comparison of weights cannot be made between bodies of similar dimensions, a careful assessment shows that the saving in weight afforded by aluminium construction is approximately 1 ton.
On average a vehicle completes 18,000 to 20,000 miles in a year and it is considered that this is equivalent to a mileage of 35,000 on long-distance trunking runs. Loading and unloading of high-grade bricks occupies I to If hours and delays on the sites visited represent a substantial percentage of the total working time of the vehicle. On short-distance.hauls, the time occupied on return trips with the vehicle unladen is a relatively small percentage of the total, but on longer runs it is a far more serious factor. Deliveries are therefore normally limited to a radius of 50 miles on the grounds of transport economy.
Cost of the Bona!lack bodies is £285, which is about £100 more than that of a comparable platform body constructed from timber and steel. From experience with the older bodies it would be necessary to withdraw a vehicle equipped with a body of this type for at least a week every year for bodywork repairs, to the cost of approximately £40 for materials and labour.
In two years, expenditure on the aluminium bodies has been about £5, and it is confidently expected that they will continue in service for four years without major repair, after which the vehicles will be replaced. The bodies are covered by a two-year guarantee.
Defects Unpredictable Bodywork defects that developed in the steel-lined wood bodies were generally unpredictable, so that it was not usually possible to pre-arrange overhaul during the slack season in January and February. Vehicles were often immobilized in a peak traffic period with a consequent loss of ton-miles of around 200,000 in the week. Deterioration took the form of rusting. separation from the timber and loosened bolts.
Bricks of two sizes are carried with thicknesses of 2-,5; in. and 2i in. The maximum load of a 7-tonner is 2,500 of the larger bricks, which weigh 9 tons. Employing vehicles of larger capacity would be uneconomic because the overall requirements of smaller users are often limited to 2,0003,(R)0 bricks and heavier vehicles would be at a disadvantage on many of the sites with regard to manceuvrability and so on. Moreover, it would • be impossible to back larger vehicles into the kilns for direct loading.
Drivers assist in loading at the works and unloading at the site and are paid a bonus on the number of bricks handled. It is emphasized by the transport manager of the company that this is a handling bonus rather than a driving bonus, in that it promotes a speedy turn-round of the vehicles rather than a reduction in journey time. Wages are based on a working week of 44 hours and a guaranteed overtime period of five hours. The average working week around 50 hours.
The company have works at Sedgley, Kingsbury and Hartlebury. Two of the 12 7-tonners are operated from Kingsbury, whilst the bricks produced at the Hartlebury works are delivered by contract-vehicles. The increase in rates of 10 per cent. recommended by the Road Haulage Association has not been applied to deliveries in the 50-mile radius, but is charged for loads on special long-distance runs.
Apart from their light-weight advantage and freedom from corrosion, the aluminium bodies are more resistant to damage in accidents and they are easy to repair. They can also be readily removed from the chassis for painting.
Floor length of the body is 18 ft.. whilst the overall width is 7 ft. 6 in. A Dekaloy interlocking ribbed-type floor is mounted on Bonallack standard four-way-braced support
feet. Height of the front bulkhead is 1 ft. 10 in. from the floor, and the detachable tailboard has the same overall height, a 2-in, gap at the bottom being provided to facilitate floor sweeping.
Bonallack technicians emphasize that using four-waybraced feet is particularly advantageous in the case of the Baggeridge vehicles, because they regularly traverse uneven ground with a heavy load. The body is, therefore, continually subject to severe torsional flexing and to accommodate this it is essential to obviate local stress. concentrations. Layout of the four-way-bracing members is such that torsional stresses are uniformly distributed throughout the length of the body, without increasing the height of the platform.
Reinforcing Members The feet are solid-riveted by the cold-squeeze method, whilst gussets and brackets are assembled with the aid of high-tensile bolts and self-locking nuts. Reinforcing members of light-alloy plate are used in conjunction with steel plate to give flexibility with strength. Bearers are secured to the chassis with screwed high-tensile rods in combination with clench-plates and extruded locking sockets.
Acquired by the company in May of this year. six Thames Trader 7-ton tipping chassis are equipped with Bonallack light-alloy bodies, which provide an estimated weight saving of 14-15 cwt., compared with comparable bodies of wood or steel. This is equivalent to about 250 bricks per load, the maximum payload being slightly in excess of 9 tons. A typical load is comparable to that of the platform bodies and comprises about 2,500 high-grade bricks or 3,000 common bricks.
Internal dimensions of the body include a length and width of 14 ft. 6 in. and 6 ft. 11 in. respectively, whilst the height of the body at the front, sides and rear is 2 ft. 9 in. A Dekaloy interlocking floor is fitted giving a smooth interior surface. and the body is panelled in 10-gauge aluminium sheet, the sides being doubleskinned to preserve the paintwork and appearance of the visible Panels by affording protection against brick impact from the inside. The tailgate is hinged at both top and bottom.
The body is mounted on a steel channel-sectioned lifting frame, transverse support being provided by tapered members outrigged from the main runners. This layout is used to reduce the floor height in the interests of easy manual loading, the saving in height being about 41 in. Lifting gear is an Edbro 4LNX twin-ram front-ofbody unit weighing about 41cwt., the weight of the body and frame members being approximately 91 cwt. The vehicle is equipped with 8.25 x 20 12-ply tyres. Two drop sections are fitted on each side and are secured to the posts by toggle-type pegs. In the lowered position, the sides contact rubber buffer pads mounted on resilient brackets.
The merits of the aluminium tipper bodies may be compared with the advantages afforded by the light-alloy platform type, freedom from corrosion and ease of repair being of first importance in terms of operating economy. Experience over a relatively short period indicates that the bodies are sufficiently robust for the arduous work they have to perform.
Increased Use of Tippers
On many runs it is not known before the vehicle leaves the works whether the builder will require that the bricks be unloaded by hand or discharged by tipping on the site. It is possible, therefore, that increased use will be made of tipping vehicles.
A new project that promises to reduce loading time at the kiln and the labour force required has already been tried out experimentally. In the kiln, stacks of bricks are "set" and later "drawn "by Hyster oil-engined fork-lift trucks of 3,000-lb. capacity, which are equipped with a special fork attachment. This comprises four forks, three of which are fitted on the inside with hydraulically operated expanding pads. The forks are inserted in spaces between the bricks of the lower layer of the stack, and the pads are then used c26 to grip each line of bricks on the squeeze principle.
One of the three trucks is now being employed to load the road vehicles, and on average this reduces loading time by 20 min. It also enables the labour force to be reduced by at least one man and generally improves the working conditions of the operators. Internal dimensions of the tipper bodies are such that bricks can be stacked on the floor with virtually no waste space.
Fuel consumptions of the vehicles are regarded as satisfactory, taking into account the type of conditions under which the trucks operate. On averagethe Commer platform vehicles equipped with petrol engines return 8.9 m.p.g., whilst the diesel-engined versions give 15-16 m.p.g. In the case of the Thames Trader the average is 12-14 m.p.g.