DEMOUNTABLE
Page 55

Page 56
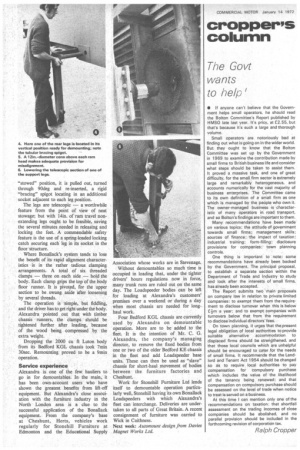
If you've noticed an error in this article please click here to report it so we can fix it.
DISTRIBUTION.
by Alan Bunting, MIMechE
Body swop test Freight BonaHack's demountable system is readily identifiable through its unique use of small castor wheels on the bottom of the support legs. These wheels, of 4m. diameter, allow the parked body to inch sideways as it is drawn into alignment while remounting.
Tolerance in lateral alignment is one of the most attractive features of the system. If the driver reverses the chassis with sufficient care to avoid fouling the support legs with the rear wheels, then he can pick up the body. Built into the floor structure on the body centre-line are two conical recesses. Each lifting jack on the chassis terminates in a spherical end, which makes contact with the cone — 12in. across — so that a misalignment of up to 6in. on either side is catered for automatically.
Achieving accurate alignment is one of the most time-consuming aspects of most demountable systems. Bonallack has recognized this fact and made particularly generous provision for drivers poor at reversing. The castor wheels on the Alexandra body could not be spun by hand, but the built-in friction — whether caused by corrosion or deliberately tight assembly — is of obvious benefit when a body is parked on a sloping area or somewhere exposed to side-winds.
At first sight, lifting the body with point contact only on its centre line could produce an unstable situation. In practice the front and rear rams are operated separately, the opposite end being supported either on its legs or on the chassis frame. At the front two hydraulic rains are mounted side by side, linked by a short cross-beam to which the lifting -ball" is attached.
Two separate control levers are employed on the electro-hydraulic Smiths powerpack, which is conveniently mounted on the nearside of the chassis and isolated against tampering by a master switch in the cab. With about 14in. of travel, the rains used by Bonallack are particularly suitable for achieving interchangeability in a demountable fleet with different height chassis — on, say, 16im and 20in. wheels.
When demounting a body, the front end must be lifted first, the body being supported at the rear lifting point on a hinge-pin extending from the chassis as part of the ram-mounting cross-member.
In normal circumstances, no Bonallack demountable body is likely to suffer leg collapse. The legs are of 34in. square steel tube. To lower each one from its horizontal "stowed" position, it is pulled out, turned through 90deg and re-inserted, a rigid "bracing" spigot locating in an additional socket adjacent to each leg position.
The legs are telescopic — a worthwhile feature from the point of view of neat stowage; but with 14in. of ram travel non • extending legs ought to be feasible, saving the several minutes needed in releasing and • locking the feet. A commendable safety • feature is the use of a spring-loaded locking catch securing each leg in its socket in the floor structure.
• Where Bonaliack's system tends to lose • the benefit of its rapid alignment characteristics is in the rather tedious clamping . arrangements. A total of six threaded • clamps — three on each side — hold the body. Each clamp grips the top of the body floor runner. It is pivoted, for the upper section to be swung aside after loosening • by several threads.
The operation is simple, but fiddling, . and the driver has to get right under the body. Alexandra pointed out that with timber chassis runners, the clamps should be tightened further after loading, because • of the wood being compressed by the extra weight.
• Dropping the 2000 cu ft Luton body from its Bedford KGL chassis took 7min 30sec. Remounting proved to be a 9min operation.
Service experience
Alexandra is one of the few hauliers to go in for deinouatables. In the main, it has been own-account users who have shown the greatest benefits from lift-off equipment. But Alexandra's close association with the furniture industry in the North London area is a clue to the • successful application of the Bonallack equipment. From the company's base at Cheshunt, Herts, vehicles work regularly for Stonehill Furniture at Edmonton and the Educational Supply ° Association whose works are in Stevenage.
Without clemountables so much time is occupied in loading that, under the tighter drivers' hours regulations now in force, many trunk runs are ruled out on the same day. The Loadspeeder bodies can be left for loading at Alexandra's customers' premises over a weekend or during a day when most chassis are needed for long-. haul work.
• Four Bedford KGL chassis are currently used by Alexandra on demountable operation. More are to be added to the fleet. It is the intention of Mr. C. G. Alexandra, the company's managing director, to remove the fixed bodies from one or two of the older Bedford KE chassis in the fleet and add Loadspeeder base units. These can then be used as "slave" chassis for short-haul movement of bodies between the furniture factories and Cheshunt.
Work for Stonehill Furniture Ltd lends itself to demountable operation particularly well, Stonehill having its own Bonallack Loadspe,eders with which Alexandra's fleet can interchange. Deliveries are undertaken to all parts of Great Britain. A recent consignment of furniture was carried to Wick in Caithness.
Next week: Automount design from Davies Magnet Works Ltd.