A manual link that gets the spares out
Page 47
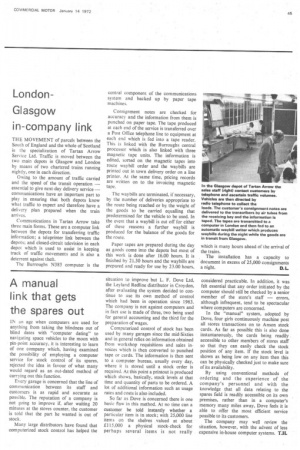
If you've noticed an error in this article please click here to report it so we can fix it.
IN an age when computers are used for anything from taking the blindness out of blind dates with "computer dating" to navigating space vehicles to the moon with pin-point accuracy, it is interesting to learn of one company which, having examined the possibility of employing a computer service for stock control of its spares, rejected the idea in favour of what many would regard as an out-dated method of carrying out this function.
Every garage is concerned that the line of communication between its staff and customers is as rapid and accurate as possible. The reputation of a company is not going to improve if, after waiting 20 minutes at the stores counter, the customer is told that the part he wanted is out of stock.
Many large distributors have found that computerized stock control has helped the situation to improve but L. F. Dove Ltd, the Leyland Redline distributor in Croydon, after evaluating the system decided to continue to use its own method of control which had been in operation since 1963. The company is not against computers and in fact use is made of three, two being used for general accounting and the third for the preparation of wages.
Computerized control of stock has been used by many garages since the mid-Sixties and in general relies on information obtained from workshop requisitions and sales invoices which is then converted to punched tape or cards. The information is then sent to a computer bureau, usually every day, where it is stored until a stock order is required. At this point a printout is produced which shows, basically, stock levels at that time and quantity of parts to be ordered. A lot of additional information such as usage rates and costs is also included.
So far as Dove is concerned there is one basic flaw in this method. At no time can a customer be told instantly whether a particular item is in stock; with 25,000 line items on the shelves valued at about 1115,000 a physical stock-check for perhaps several items is not really considered practicable. In addition, it was felt essential that any order initiated by the computer should still be checked by a senior member of the store's staff — errors, although infrequent, tend to be spectacular where computers are concerned.
In the "manual" system, adopted by Dove, four girls continuously machine post all stores transactions on to Anson stock cards. As far as possible this is also done instantaneously, the cards being readily accessible to other members of stores staff so that they can easily check the stock position of any item. If the stock level is shOwn as being low on any item then this can be physically checked just to make sure of its availability.
By using conventional methods of ordering and the experience of the company's personnel and with the knowledge that all data relating to the spares field is readily accessible on its own premises, rather than in a computer's memory many miles away, Dove feels it is able to offer the most efficient service possible to its customers.
The company may well review the situation, however, with the advent of less expensive in-house computer systems. TAL