REFRIGERATION TECHNIQUES
Page 56
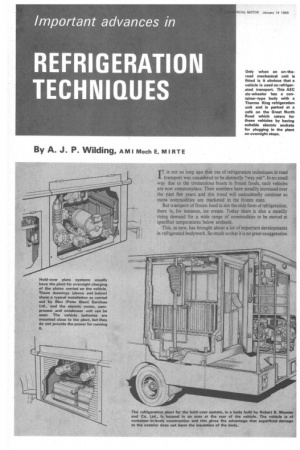
Page 57
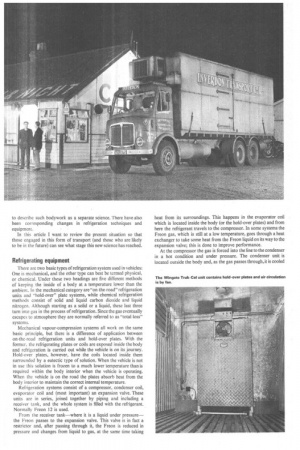
Page 58
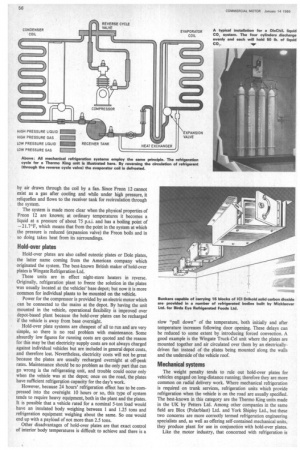
Page 59
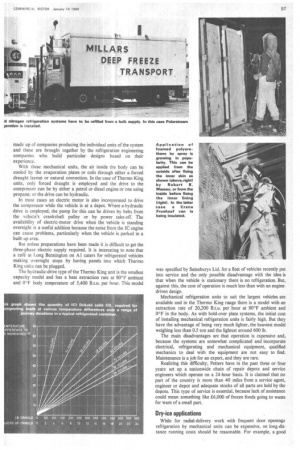
Page 60
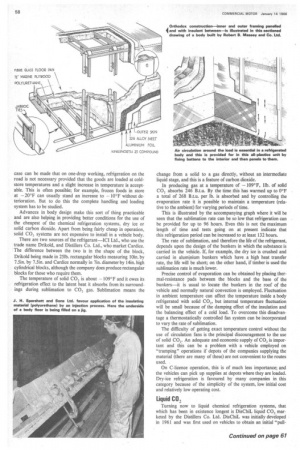
Page 63
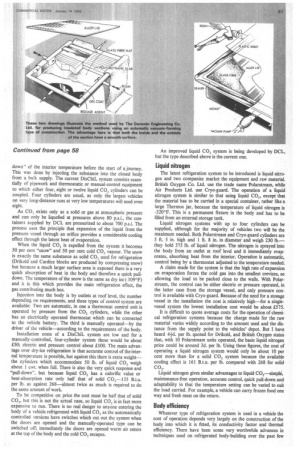
Page 64
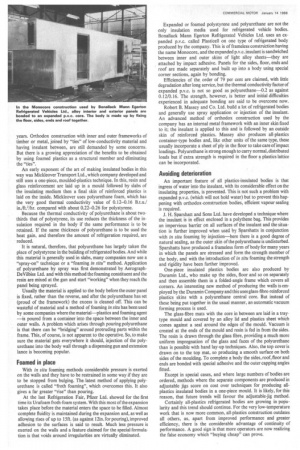
If you've noticed an error in this article please click here to report it so we can fix it.
By A. J. P. Wilding, AMI Mech E, MIRTE IT is not so long ago that Use of refrigeration techniques in road transport was considered to be distinctly "way out". In no small way due to the tremendous boom in frozen foods, such vehicles are now commonplace. Their numbers have steadily increased over the past few years and this trend will undoubtedly continue as more commodities are marketed in the frozen state.
But transport of frozen food is not the only form of refrigeration: there is, for instance, ice cream. Today there is also a steadily rising demand for a wide range of commodities to be moved at specified temperatures below ambient.
This, in turn, has brought about a lot of important developments in refrigerated bodywork. So much so that it is no great exaggeration to describe such bodywork as a separate science. There have also been corresponding changes in refrigeration techniques and equipment.
In this article I want to review the present situation so that those engaged in this form of transport (and those who are likely to be in the future) can see what stage this new science has reached.
Refrigerating equipment
There arc two basic types of refrigeration system used in vehicles: One is mechanical, and the other type can best be termed physical, or chemical. Under these two headings are five different methods of keeping the inside of a body at a temperature lower than the ambient. In the mechanical category are "on-the-road" refrigeration units and "hold-over" plate systems, while chemical refrigeration methods consist of solid and liquid carbon dioxide and liquid nitrogen. Although starting as a solid or a liquid, these last three turn into gas in the process of refrigeration. Since the gas eventually escapes to atmosphere they are normally referred to as "total-loss" systems.
Mechanical vapour-compression systems all work on the same basic principle, but there is a difference of application between on-the-road refrigeration units and hold-over plates. With the former, the refrigerating plates or coils are exposed inside the body and refrigeration is carried out while the vehicle is on its journey. Hold-over plates, however, have the coils located inside them surrounded by a eutectic type of solution. When the vehicle is not in use this solution is frozen to a much lower temperature than is required within the body interior when the vehicle is operating. When the vehicle is on the road the plates absorb heat from the body interior to maintain the correct internal temperature.
Refrigeration systems consist of a compressor, condenser coil, evaporator coil and (most important) an expansion valve. These units are in series, joined together by piping and including a receiver tank, and the whole system is filled with the refrigerant. Normally Freon 12 is used.
From the receiver tank—where it is a liquid under pressure— the Freon passes to the expansion valve. This valve is in fact a restrictor and, after passing through it, the Freon is reduced in pressure and changes from liquid to gas, at the same time taking heat from its surroundings. This happens in the evaporator coil which is located inside the body (or the hold-over plates) and from here the refrigerant travels to the compressor. In some systems the Freon gas, which is still at a low temperature, goes through a heat exchanger to take some heat from the Freon liquid on its way to the expansion valve; this is done to improve performance.
At the compressor the gas is forced into the line to the condenser in a hot condition and under pressure. The condenser unit is located outside the body and, as the gas passes through, it is cooled by air drawn through the coil by a fan. Since Freon 12 cannot exist as a gas after cooling and while under high pressure, it reliquefies and flows to the receiver tank for recirculation through the system.
The system is made more clear when the physical properties of Freon 12 are known; at ordinary temperatures it becomes a liquid at a pressure of about 75 p.s.i. and has a boiling point of —21.7°F, which means that from the point in the system at which the pressure is reduced (expansion valve) the Freon boils and in so doing takes heat from its surroundings.
Hold-over plates Hold-over plates are also called eutectic plates or Dole plates, the latter name coming from the American company which originated the system. The best-known British maker of hold-over plates is Wingate Refrigeration ltd.
These units are in effect night-store heaters in reverse. Originally, refrigeration plant to freeze the solution in the plates was usually located at the vehicles' base depot; but now it is more common for individual plants to be mounted on the vehicle.
Power for the compressor is provided by an electric motor which can be connected to the mains at the depot. By having the unit mounted in the vehicle, operational flexibility is improved over depot-based plant because the hold-over plates can be recharged if the vehicle is away from base overnight.
Hold-over plate systems are cheapest of all to run and are very simple, so there is no real problem with maintenance. Some absurdly low figures for running costs are quoted and the reason for this may be that electricity supply costs are not always charged against individual vehicles but are included in general depot costs, and therefore lost. Nevertheless, electricity costs will not be great because the plates are usually recharged overnight at off-peak rates. Maintenance should be no problem as the only part that can go wrong is the refrigerating unit, and trouble could occur only when the vehicle was at the depot; once on the road, the plates have sufficient refrigeration capacity for the day's work.
However, because 24 hours' refrigeration effect has to be compressed into the overnight 10 hours or so, this type of system tends to require heavy equipment, both in the plant and the plates. It is possible that a vehicle rated for a nominal 5-ton load would have an insulated body weighing between 1 and 1.25 tons and refrigeration equipment weighing about the same. So one would end up with a payload of not more than 2.5 tons.
Other disadvantages of hold-over plates are that exact control of interior body temperatures is difficult to achieve and there is a slow "pull down" of the temperature, both initially and after temperature increases following door opening. These delays can be reduced to some extent by introducing forced convection. A good example is the Wingate Truck-Cel unit where the plates are mounted together and air circulated over them by an electricallydriven fan instead of the plates being mounted along the walls and the underside of the vehicle roof.
Mechanical systems The weight penalty tends to rule out hold-over plates for vehicles engaged on long-distance running; therefore they are more common on radial delivery work. Where mechanical refrigeration is required on trunk services, refrigeration units which provide refrigeration when the vehicle is on the road are usually specified. The best-known in this category are the Thermo King units made in the UK by Petters Ltd. Among other companies in the same field are Blox (Polarblast) Ltd. and York Shipley Ltd., but these two concerns are more correctly termed refrigeration engineering specialists and, as well as offering self-contained mechanical units, they produce plant for use in conjunction with hold-over plates.
Like the motor industry, that concerned with refrigeration is made up of companies producing the individual units of the system and these are brought together by the refrigeration engineering companies who build particular • designs based on their experience.
With these mechanical units, the air inside the body can be cooled by the evaporation plates or coils through either a forced draught layout or natural convection. In the case of Thermo King units, only forced draught is employed and the drive to the compressor can be by either a petrol or diesel engine or one using propane: or the drive can be hydraulic.
In most eases an electric motor is also incorporated to drive the compressor while the vehicle is at a depot. Where a hydraulic drive is employed, the pump for this can be driven by belts from the vehicle's crankshaft pulley or by power take-off. The availability of electric-motor drive when the vehicle is standing overnight is a useful addition because the noise from the IC engine can cause problems, particularly when the vehicle is parked in a built-up area.
But unless preparations have been made it is difficult to get the three-phase electric supply required. It is interesting to note that a café at Long Bennington on Al caters for refrigerated vehicles making overnight stops by having panels into which Thermo King units can be plugged.
The hydraulic-drive type of the Thermo King unit is the smallest capacity model and has a heat extraction rate at 80cF ambient and 0°F body temperature of 5,400 B.t.u. per hour. This model was specified by Sainsburys Ltd. for a fleet of vehicles recently put into service and the only possible disadvantage with the idea is that when the vehicle is stationary there is no refrigeration. But, against this, the cost of operation is much less than with an enginedriven design.
Mechanical refrigeration units to suit the largest vehicles are available and in the Thermo King range there is a model with an extraction rate of 20,200 B.t.u. per hour at 80°F ambient and 0°F in the body. As with hold-over plate systems, the initial cost of installing mechanical refrigeration units is fairly high. But they have the advantage of being very much lighter, the heaviest model weighing less than 0.5 ton and the lightest around 600 lb.
The main disadvantages are that operation is expensive and, because the systems are somewhat complicated and incorporate electrical, refrigerating and mechanical equipment, qualified mechanics to deal with the equipment are not easy to find. Maintenance is a job for an expert, and they are rare.
Realizing this difficulty, Petters have in the past three or four years set up a nationwide chain of repair depots and service engineers which operate on a 24-hour basis. It is claimed that no part of the country is more than 40 miles from a service agent, engineer or depot and adequate stocks of all parts are held by the depots. This type of service is essential, because lack of assistance could mean something like £6,000 of frozen foods going to waste for want of a small part.
Dry-ice applications
While for radial-delivery work with frequent door openings refrigeration by mechanical units can be expensive, on long-distance running costs should be reasonable. For example, a good case can be made that on one-drop working, refrigeration on the road is not necessary provided that the goods are loaded at coldstore temperatures and a slight increase in temperature is acceptable. This is often possible; for example, frozen foods in store at —20°F can usually stand an increase to —10°F without deterioration. But to do this the complete handling and loading system has to be studied.
Advances in body design make this sort of thing practicable and are also helping in providing better conditions for the use of the cheapest of the chemical refrigeration systems, dry ice or solid carbon dioxide. Apart from being fairly cheap in operation, solid CO, systems are not expensive to install in a vehicle body. There are two sources of the refrigerant—ICI Ltd., who use the trade name Drikold, and Distillers Co. Ltd., who market Cardice. The difference between the two is in the shape of the block, Drikold being made in 251b. rectangular blocks measuring 10in. by 7.5in. by 7.5in. and Cardic.e normally in 7in. diameter by 14in. high cylindrical blocks, although the company does produce rectangular blocks for those who require them.
The temperature of solid CO, is about —109°F and it owes its refrigeration effect to the latent heat it absorbs from its surroundings during sublimation to CO, gas. Sublimation means the change from a solid to a gas directly, without an intermediate liquid stage, and this is a feature of carbon dioxide.
In producing gas at a temperature of —109°F, llb. of solid CO, absorbs 246 B.t.u. By the time this has warmed up to 0°F a total of 268 B.t.u. per lb. is absorbed and by controlling the evaporation rate it is possible to maintain a temperature (relative to the ambient) for varying periods of time.
This is illustrated by the accompanying graph where it will be seen that the sublimation rate can be so low that refrigeration can be provided for up to 96 hours. Even this is not the maximum length of time and tests going on at present indicate that this refrigeration period can be increased to at least 132 hours.
The rate of sublimation, and therefore the life of the refrigerant, depends upon the design of the bunkers in which the substance is carried in the vehicle. If, for example, the dry ice is crushed and carried in aluminium bunkers which have a high heat transfer rate, the life will be short; on the other hand, if timber is used the sublimation rate is much lower.
Precise control of evaporation can be obtained by placing thermal-resistance pads between the blocks and the base of the bunkers—it is usual to locate the bunkers in the roof of the vehicle and normally natural convection is employed. Fluctuation in ambient temperature can affect the temperature inside a body refrigerated with solid CO„ but internal temperature fluctuation will be small because of the damping effect of the insulation and the balancing effect of a cold load. To overcome this disadvantage a thermostatically controlled fan system can be incorporated to vary the rate of sublimation.
The difficulty of getting exact temperature control without the use of circulation fans is the principal discouragement to the use of solid CO,. An adequate and economic supply of CO, is important and this can be a problem with a vehicle employed on "tramping" operations if depots of the companies supplying the material (there are many of these) are not convenient to the routes used.
On C-licence operation, this is of much less importance; and the vehicles can pick up supplies at depots where they are loaded. Dry-ice refrigeration is favoured by many companies in this category because of the simplicity of the system, low initial cost and relatively low operating cost.
Liquid CO2
Turning now to liquid chemical refrigeration systems, that which has been in existence longest is DisChiL liquid CO, marketed by the Distillers Co. Ltd. DisChiL was initially developed in 1961 and was first used on vehicles to obtain an initial "pull
downof the interior temperature before the start of a journey. This was done by injecting the substance into the closed body from a bulk supply. The current DisChiL system consists essentially of pipework and thermostatic or manual-control equipment to which either four, eight or twelve liquid CO, cylinders can be coupled. Four cylinders are usual, as only the largest vehicles on very long-distance runs at very low temperatures will need even eight.
As CO, exists only as a solid or gas at atmospheric pressure and can only be liquefied at pressures above 80 p.s.i., the containers supplied by DCL are pressurized to about 700 p.s.i. The process uses the principle that expansion of the liquid from the pressure vessel through an orifice provides a considerable cooling effect through the latent heat of evaporation.
When the liquid CO, is expelled from the system it becomes 50 per cent "snow" and 50 per cent cold CO, vapour. The snow is exactly the same substance as solid CO, used for refrigeration (Drikold and Cardice blocks are produced by compressing snow) but because a much larger surface area is exposed there is a very quick absorption of heat in the body and therefore a quick pulldown. The temperature of the snow is the same as dry ice (-109°F) and it is this which provides the main refrigeration effect, the gas contributing much less.
Injection into the body is by outlets at roof level, the number depending on requirements, and three types of control system are available: Two are automatic, in one a thermostat control unit is operated by pressure from the CO, cylinders, while the other has an electrically operated thermostat which can be connected to the vehicle battery. The third is manually operated—by the driver of the vehicle—according to the requirements of the body.
Installation costs of a DisChiL system are low and for a manually-controlled, four-cylinder system these would be about £50; electric and pressure control about E100. The main advantage over dry-ice refrigeration is that accurate control of the internal temperature is possible, but against this there is extra weight— the cylinders which accommodate 50 lb. of liquid CO, weigh about 1 cwt. when full. There is also the very quick response and "pull-down-, but because liquid CO, has a calorific value or heat-absorption rate only half that of solid CO2-135 B.t.u. per lb. as against 268—almost twice as much is required to do the same amount of work.
To be competitive on price the cost must be half that of solid CO„ but this is not the actual case, so liquid CO, is in fact more expensive to run. There is no real danger to anyone entering the body of a vehicle refrigerated with liquid CO, as the automatically controlled versions have switches which cut out the system when the doors are opened and the manually-operated type can be switched off; immediately the doors are opened warm air enters at the top of the body and the cold CO, escapes. An improved liquid CO, system is being developed by DCL, but the type described above is the current one.
Liquid nitrogen
The latest refrigeration system to be introduced is liquid nitrogen and two companies market the equipment and raw material. British Oxygen Co. Ltd. use the trade name Polarstream, while Air Products Ltd. use Cryo-guard. The operation of a liquid nitrogen system is similar to that using liquid CO„ except that the material has to be carried in a special container, rather like a large Thermos jar, because the temperature of liquid nitrogen is -320°F. This is a permanent fixture in the body and has to be filled from an external storage tank.
Liquid nitrogen systems with up to four cylinders can be supplied, although for the majority of vehicles two will be the maximum needed. Both Polarstream and Cryo-guard cylinders are 5 ft. 5 in. high and 1 ft. 8 in. in diameter and weigh 230 lb.— they hold 375 lb. of liquid nitrogen. The nitrogen is sprayed into the body from an outlet at roof level and it immediately evaporates, absorbing heat from the interior. Operation is automatic, control being by a thermostat adjusted to the temperature needed.
A claim made for the system is that the high rate of expansion on evaporation forces the cold gas into the smallest crevices, so allowing the load to be packed close to the walls. With Polarstream, the control can be either electric or pressure operated, in the latter case from the storage vessel, and only pressure control is available with Cryo-guard. Because of the need for a storage vessel in the installation the cost is relatively high—for a singlevessel system the lowest installation cost would be about £575.
It is difficult to quote average costs for the operation of chemical refrigeration systems because the charge made for the raw material varies widely according to the amount used and the distance from the supply point to the vehicles' depot. But I have heard 4+d. per lb. quoted for Drikold, and British Oxygen states that, with 10 Polarstream units operated, the basic liquid nitrogen price could be around 3d. per lb. Using these figures, the cost of operating a liquid nitrogen system would only be about 10 per cent more than for a solid CO, system because the available cooling effect is 161 B.t.u. per lb. compared with 268 for solid C 0 2.
Liquid nitrogen gives similar advantages to liquid CO2—simple, maintenance-free operation, accurate control, quick pull-down and adaptability in that the temperature setting can be varied to suit the load carried. For example, a vehicle can carry frozen food one way and fresh meat on the return.
Body efficiency
Whatever type of refrigeration system is used in a vehicle the cost of operation depends very largely on the construction of the body into which it is fitted, its conductivity factor and thermal efficiency. There have been some very worthwhile advances in techniques used on refrigerated body-building over the past few years. Orthodox construction with inner and outer frameworks of timber or metal, joined by "ties" of low-conductivity material and having insulant between, are still demanded by some concerns. But there is a growing appreciation of the benefits to be obtained by using foamed plastics as a structural member and eliminating the "ties".
An early exponent of the art of making insulated bodies in this way was Mickleover Transport Ltd., which company developed and still uses a one-piece, moulded-plastics technique. In this, resin and glass reinforcement are laid up in a mould followed by slabs of the insulating medium then a final skin of reinforced plastics is laid on the inside. Mickleover uses polyurethane foam, which has the very good thermal conductivity value of 0.12-0.16 B.t.u./ in./ft.2/hr. compared with about 0.22-0.26 for polystyrene.
Because the thermal conductivity of polyurethane is about twothirds that of polystyrene, its use reduces the thickness of the insulation required in the body if the same performance is to be retained. If the same thickness of polyurethane is to be used the heat gain, and therefore the amount of refrigeration required, are reduced.
It is natural, therefore, that polyurethane has largely taken the place of polystyrene in the building of refrigerated bodies. And while this material is generally used in slabs, many companies now use a "spray-on" technique or a "foaming in situ" method. Application of polyurethane by spray was first demonstrated by AerographDeVilbiss Ltd. and with this method the foaming constituent and the resin are mixed at the gun and start "working" when they reach the panel being sprayed.
Usually the material is applied to the body before the outer panel is fixed, rather than the reverse, and after the polyurethane has set (proud of the framework) the excess is cleaned off. This can be wasteful of material and a method of foaming in situ has been used by some companies where the material—plastics and foaming agent —is poured from a container into the space between the inner and outer walls. A problem which arises through pouring polyurethane is that there can be "bridging" around protruding parts within the frame. This, of course, is not apparent to the operative. So, to make sure the material gets everywhere it should, injection of the polyurethane into the body wall through a dispensing gun and extension lance is becoming popular.
Foamed in place
With in situ foaming methods considerable pressure is exerted on the walls and they have to be restrained in some way.if they are to be stopped from bulging. The. latest method of applying polyurethane is called "froth foaming", which overcomes this. It also gives a far greater "rise" than pouring.
At the last Refrigeration Fair, Pfizer Ltd. showed for the first time its Urafoam froth-foam system. With this most of the expansion takes place before the material enters the space to be filled. Almost complete fluidity is maintained during the expansion and, as well as allowing rises of up to 15ft. (as against 12in. for pouring), improved adhesion to the surfaces is said to result. Much less pressure is exerted on the walls and a feature claimed for the special formulation is that voids around irregularities are virtually eliminated. Expanded or foamed polystyrene and polyurethane are not the only insulation media used for refrigerated vehicle bodies. Bonallack Mann Egerton Refrigerated Vehicles Ltd. uses an expanded p.v.c. called Plasticell on one type of refrigerated body produced by the company. This is of frameless constrtiction having the name Monocore, and the expanded p.v.c. insulant is sandwiched between inner and outer skins of light alloy sheets—they are attached by impact adhesive. Panels for the sides, floor, ends and roof are made separately and built up into a body using special corner sections, again by bonding.
Efficiencies of the order of 79 per cent are claimed, with little degradation after long service, but the thermal conductivity factor of expanded p.v.c. is not so good as polyurethane 0.2 as against 0.12/0.16. The strength, however, is better and initial difficulties experienced in adequate bonding are said to be overcome now.
Robert B. Massey and Co. Ltd. build a lot of refrigerated bodies and generally use spray application or injection of the insulant. An advanced method of orthodox construction used by the company has an internal metal framework with an inner skin fixed to it; the insulant is applied to this and is followed by an outside skin of reinforced plastics. Massey also produces all-plastics container-type bodies and, like other units of the same type, these usually incorporate a sheet of ply in the floor to take care of impact loadings. Polyurethane is strong enough to carry normal, distributed loads but if extra strength is required in the floor a plastics lattice can be incorporated.
Avoiding deterioration
An important feature of all plastics-insulated bodies is that ingress of water into the insulant, with its considerable effect on the insulating properties, is prevented. This is not such a problem with expanded p.v.c. (which will not hold water) but to prevent this happening with orthodox-construction bodies, efficient vapour sealing is required.
J. H. Sparshatt and Sons Ltd. have developed a technique where the insulant is in effect enclosed in a polythene bag. This provides an impervious barrier on all surfaces of the insulant and the situation is further improved when used by Sparshatts in conjunction with in situ foaming by injection—here there is a good degree of natural sealing, as the outer skin of the polyurethane is undisturbed. Sparshatts have produced a frameless form of body for many years in which the panels are stressed and form the strength member of the body, and with the introduction of in situ foaming the strength and rigidity have been further improved.
One-piece insulated plastics bodies are also produced by Duramin Ltd., who make up the sides, floor and so on separately and then assemble them in a folded-angle frame which covers all corners. An interesting new method of producing the walls is employed by the Duramin Company and this uses glass-fibre-reinforced plastics skins with a polyurethane central core. But instead of these being put together in the usual manner, an automatic vacuum forming process is used.
The glass-fibre mats with the core in between are laid in a traytype mould and covered by an alloy lid and plastics sheet which comes against a seal around the edges of the mould. Vacuum is created at the ends of the mould and resin is fed in from the sides. The resin is drawn through the glass fibre, providing a much more uniform impregnation of the glass and faces of the polyurethane than is possible with hand lay-up techniques. Also, the top cover is drawn on to the top mat, so producing a smooth surface on both sides of the moulding. To complete a body the sides, roof, floor and ends are bonded with special adhesive and the outer capping angles fitted.
Except in special cases, and where large numbers of bodies are ordered, methods where the separate components are produced in adjustable jigs score on cost over techniques for producing allplastics insulated bodies in a one-piece mould. It is likely, for this reason, that future trends will favour the adjustable-jig method.
Certainly all-plastics refrigerated bodies are growing in popularity and this trend should continue. For the very low-temperature work that is now more common, all-plastics construction outdates all others, as, apart from improved performance and greater efficiency, there is the considerable advantage of continuity of performance. A good sign is that more operators are now realizing the false economy which "buying cheap" can prove.