Case Hardening Practices Part I
Page 50
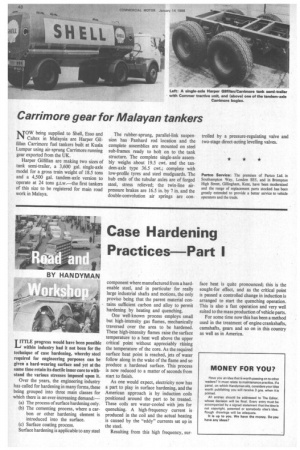
If you've noticed an error in this article please click here to report it so we can fix it.
IiiTTLE progress would have been possible within industry had it not been for the technique of case hardening, whereby steel required for engineering purposes can be given a hard-wearing surface and yet at the same time retain its ductile inner core to withstand the various stresses imposed upon it.
Over the years, the engineering industry has called for hardening in many forms, these being grouped into three main classes for which there is an ever-increasing demand:—
(a) The process of surface hardening only.
(h) The cementing process, where a car bon or other hardening element is introduced into the surface.
(c) Surface coating process.
Surface hardening is applicable to any steel component where manufactured from a hardenable steel, and in particular for really large industrial shafts and motions, the only proviso being that the parent material contains sufficient carbon and alloy to permit hardening by heating and quenching.
One well-known process employs small but high-intensity gas flames, mechanically traversed over the area to be hardened. These high-intensity flames raise the surface temperature to a heat well above the upper critical point without appreciably raising the temperature of the core. As the required surface heat point is reached, jets of water follow along in the wake of the flame and so produce a hardened surface. This process is now reduced to a matter of seconds from start to finish.
As one would expect, electricity now has a part to play in surface hardening. and the American approach is by induction coils positioned around the part to be treated. These coils are water-cooled with jets for quenching. A high-frequency current is produced in the coil and the actual heating is caused by the "eddy" currents set up in the steel.
Resulting from this high frequency, sur
face heat is quite pronounced; this is the sought-for effect, and as the critical point is passed a controlled change in induction is arranged to start the quenching operation. This is also a fast operation and very well suited to the mass production of vehicle parts.
For some time now this has been a method used in the treatment of engine crankshafts, camshafts, gears and so on in this country as well as in America.