Seddon Atkinson: where quality counts
Page 49
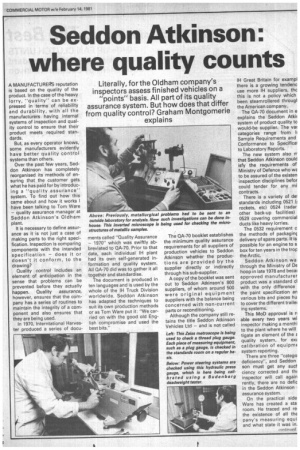
Page 50
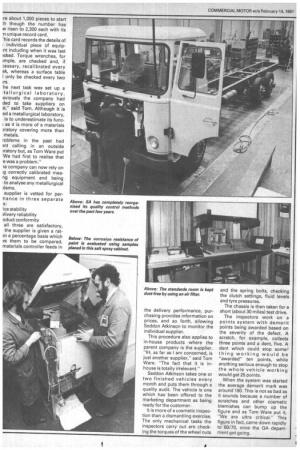
If you've noticed an error in this article please click here to report it so we can fix it.
Literally, for the Oldham company's inspectors assess finished vehicles on a "points" basis. All part of its quality assurance system. But how does that differ from quality control? Graham Montgornerie explains
A MANUFACTURER‘S reputation is based on the quality of the product. In the case of the heavy lorry, "quality" ca n be expressed in terms of reliability and durability, with all the manufacturers having internal systems of inspection and quality control to ensure that their product meets required standards.
But, as every operator knows, some manufacturers evidently have better quality control systems than others.
Over the past few years, Seddon Atkinson has completely reorganised its methods of ensuring that the customer gets what he has paid for by introducing a "quality assurance" system. To find out how this came about and how it works I have been talking to Tom Ware — quality assurance manager at Seddon Atkinson's Oldham plant.
It is necessary to define assurance as it is not just a case of making parts to the right specification. Inspection is comparing components with the intended specification — does it or doesn't it conform, to the drawing?
Quality control includes an element of anticipation in the sense that problems can be prevented before they actually happen. Quality assurance, however, ensures that the company has a series of routines to maintain the integrity of a component and also ensures that they are being used.
In 1970, Interntational Harvester produced a series of docu
ments called "Quality Assurance — 1970" which was swiftly abbreviated to QA-70. Prior to that date, each individual IH plant had its own self-generated information and quality system. All QA-70 did was to gather it all together and standardise.
The document is produced in ten languages and is used by the whole of the IH Truck Division worldwide. Seddon Atkinson has adapted the techniques to suit its own production methods or as Tom Ware put it: "We carried on with the good old English compromise and used the best bits." The QA-70 booklet establishes the minimum quality assurance requirements for all suppliers of production vehicles to Seddon Atkinson whether the productions are provided by the supplier directly or indirectly through his sub-supplier.
A copy of the booklet was sent out to Seddon Atkinson's 800 suppliers, of whom around 500 were original equipment suppliers with the balance being concerned with non-current parts or reconditioning.
Although the company still retains the title Seddon Atkinson Vehicles Ltd — and is not called
IH Great Britain for exampl there is a growing tendenc use more IH suppliers, thc this is not a policy which been steamrollered througl the American company.
The QA-70 document in e explains the Seddon Atkir system of product quality to would-be supplier. The var categories range from Ii Sample Requirements and Conformance to Specifical to Laboratory Reports.
The new system also rr that Seddon Atkinson could isfy the requirements of Ministry of Defence who wz to be assured of the existen inspection disciplines befor could tender for any mi contracts.
There is a variety of del standards including 0521 {I rockets, etc) 0524 (radar other back-up facilities) 0529 covering commercial ducts like heavy lorries.
The 0532 requirement c the methods of packaginc delivery of spare parts. It is possible for an engine to s box for ten years in the trop the Arctic.
Seddon Atkinson w a through the Ministry of Dc hoop in late 1978 and becal approved manufacturer product was a standard cl with the only difference the paint specification an various bits and pieces hu to cover the different trailei ing systems.
This MoD approval is n able every two years wi inspector making a monthl to the plant where he will tigate an element of the E quality system, for e>“ calibration of equipmE system reporting.
There are three "catego deficiency", and Seddon son must get any suck ciency corrected and thE inspector will call again rently, there are no defic in the Seddon Atkinson assurance system.
On the practical side Ware has created a sta room. He traced and re the existence of all the pany's measuring equi and what state it was in, re about 1,000 pieces to start
h though the number has N risen to 2,300 each with its :n unique record card.
his card records the details of individual piece of equipnt including when it was last )cked. Torque wrenches, for imple, are checked and, if 3essary, recalibrated every ek, whereas a surface table I only be checked every two he next task was set up a tallurgical laboratory. eviously the company had led to take suppliers on A," said Tom. Although it is ed a metallurgical laboratory, is to underestimate its func i as it is more of a materials )ratory covering more than metals.
roblems in the past had )nt calling in an outside gatory but, as Tom Ware put 'We had first to realise that e was a problem."
le company can now rely on ig correctly calibrated meang equipment and being to analyse any metallurgical )lerns.
supplier is vetted for pernance in three separate s: ice stability .livery reliability oduct conformity all three are satisfactory, the supplier is given a rat)n a percentage basis which vs them to be compared. materials controller feeds in the delivery performance, purchasing provides information on prices, and so forth, allowing Seddon Atkinson to monitor the individual supplier.
This procedure also applies to in-house products where the parent company is the supplier. "IH, as far as I am concerned, is just another supplier," said Tom Ware. "The fact that it is inhouse is totally irrelevant."
Seddon Atkinson takes one or two finished vehicles every month and puts them through a quality audit. The vehicle is one which has been offered to the marketing department as being ready for the customer.
It is more of a cosmetic inspection than a dismantling exercise. The only mechanical tasks the inspectors carry out are checking the torques of the wheel nuts and the spring bolts, checking the clutch settings, fluid levels and tyre pressures.
The chassis is then taken for a short (about 30 miles) test drive.
The inspectors work on a points system with demerit points being awarded based on the severity of the defect. A scratch, for example, collects three points and a dent, five. A dent which could stop some thing working would be "awarded" ten points, while anything serious enough to stop the whole vehicle working would get 25 points.
When the system was started the average demerit mark was around 180. This is not as bad as it sounds because a number of scratches and other cosmetic blemishes can bump up the figure and as Tom Ware put it, "We are ultra critical." This figure in fact, came down rapidly to 60/70, once the QA department got going.