Front-ol
Page 94
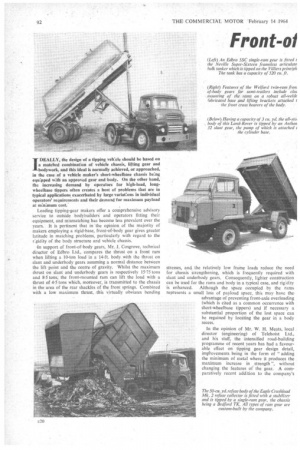
Page 95

Page 96
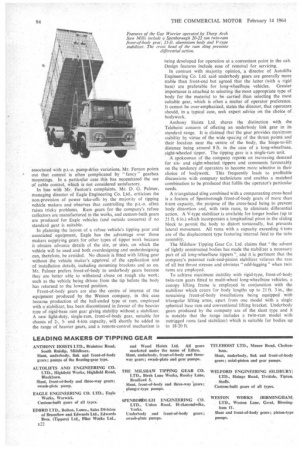
If you've noticed an error in this article please click here to report it so we can fix it.
oody in the Forefront
By P. A. C. Brockington,
A.M.I. MECH. E.
IDEALLY, the design of a tipping veh!cle should be based on a matched combination of vehicle chassis, lifting gear and bodywork, and this ideal is normally ochieved, or approached, in the case of a vehicle maker's short-wheelbase chassis be:ng equ:pped w:th an approved gear and body. On the other hand, the increasing demand by operators for high-load, longwheelbase tippers often creates a host of problems that are in typical applications exacerbated by large variat:ons in individual operators' requirements and their demand for maximum payload
at m:n:mum cost.. ,
Leading tipping-gear makers offer a comprehensive advisory service to outside bodybuilders and operators fitting their equipment, and mismatching has become less prevalent over the years. It is pertinent that in the opinion of the majority of makers employing a rigid-base, front-of-body gear gives greater latitude in matching problems, particularly with regard to the r:gidity of the body structure and vehicle chassis.
-In support of front-of-body gears, Mr, I. Cosgrove, technical director of Edbro Ltd., compares the thrust on a front ram when lifting a 10-ton load in a 14-ft. body, with the thrust on
• slant and underbody gears assuming a normal distance between the lift point and the centre of gravity. Whilst the maximum
• thrust on slant and underbody gears is respectively 15-75 tons and 8.5 tons, the front-mounted ram can lift the load with a thrust of 4.5 tons which, moreover, is transmitted to the chassis in the area of the rear shackles of the front springs. Combined with a low maximum thrust, this virtually obviates bending stresses, and, the relatively low frame loads reduce the need for chassis strengthening, which is frequently required with slant and underbody gears. Consequently, lighter construction can be used for the rams and body in a typical case, and rigidity is enhanced. Although the space occupied by the rams represents a small loss of payload space, this may have the advantage of preventing front-axle overloading (which is cited as a common occurrence with short-wheelbase tippers) and if necessary a substantial proportion of the lost space can be regained by locating the gear in a body recess.
In the opinion of Mr. W. H. Meats, local director (engineering) of Telehoist Ltd., and his staff, the intensified road-building programme of recent years has had a favourable effect on tipping gear design detail, impl-overnents being in the form of "adding
• the minimum of metal where it produces the maximum increase in strength ", without changing the features of the gear. A comparatively recent addition to the company's
standard range, front-of-body gears (of the rigid type) art normally recommended for long-wheelbase chassis, in preference to direct-thrust underbody gears on the score of improved rigid:ty and matching latitude, particularly if the vehicle is to be used on arduous site work. Stabilizers are an optional fitting and are not considered necessary for any but the toughest site conditions.
Underbody gears have the notable advantage, it is emphasized, that their location in the chassis can, as a rule, be varied to obtain a specified angle of tip, whereas this does not apply to front-of-body gears. To cover normal requirements, the range of the latter type must be extended accordingly.
Slant or vertical underbody gears are recommended for vehicles with wheelbases up to 138 in. and the front-of-body type for tippers with a longer wheelbase. The concern's Telelever double-acting link-type of gear is claimed to possess " selfcontained " rigidity in that it virtually operates independently of the body structure, and because it makes minimum demands on the chassis it is specially suitable for heavy-duty applications.
Electrically driven pumps are available with outputs up to 1.738 g.p.m. for operators who can conveniently plug in the power pack to a mains supply on the site or at the depot. notably for operation of tipping semi-trailers. :n compliance with suggestions made by H.M. Factory nspectorate regarding safety measures, the company's propand-socket automatic-engagement type of body support is now offered as an extra. A buzzer type of warning device is being developed which operates whenever the body is raised.
In common with the majority of makers, one of Telehoist's biggest headaches is caused by the variation of pitch-circle diameter and tooth form of the driving wheel for power take-offs, which adds considerably to overall costs. Unfavourable comparisons are made with the normal practice of American manufacturers of standardizing wheel diameter and form.
Whilst concentrating on twin front-of-body gears with up to l'our extensions for maximum-load semi-trailers, built in the workshops, Welford Engineering produces gears of all types for its own use and for outside concerns, notably for installations requiring non-standard equipment. A director of the company, Mr. L. A. Fenton, reports an increasing demand for tipping artics, mainly for long-distance deliveries, and points out that a lightweight portable hydraulic power pack, based on a small petrol engine, has a big potential for applications to trailers as it would eliminate dependence of tipping-gear operation on a p.t.-o.-driven pump. Any tractive unit with a suitable coupling :ould, therefore, be employed to haul the trailer, and the pack could be demountably attached to a bracket under the trailer. The ease with which it could be carried in the boot of a car would offer obvious advantages in some applications.
Principles followed by Welford technicians to promote stability include wide spacing of the hinges and close mounting of twin-ram gears, the latter practice being advantageous with regard to uniform ram action. In the case of side tippers the underbody rams are located in line with the hinges to reduce frame stressing to a minimum.
In addition to complaining of the costly difficulties associated with p.t.-o. pump-drive variations, Mr. Fenton points out that control is often complicated by " fancy " gearbox mountings. In a particular case this has necessitated the use of cable control, which is not considered satisfactory.
In line with Mr. Fenton's complaints, Mr. D. G. Palmer, managing director of Eagle Engineering Co. Ltd., criticizes the non-provision of power take-offs by the majority of tipping vehicle makers and observes that controlling the p.t.-o. often raises tricky problems. Ram gears for the company's refuse collectors are manufactured in the works, and custom-built gears are produced for Eagle vehicles (and outside concerns) if no standard gear is suitable.
In planning the layout of a refuse vehicle's tipping gear and associated equipment, Eagle has the advantage over those makers supplying gears for other types of tipper work because it obtains advance details of the site, or sites, on which the vehicle will be used and both overdesigning and underdesigning can, therefore, be avoided. No chassis is fitted with lifting gear without the vehicle maker's approval of the application and of installation details, including mounting brackets and so on. Mr. Palmer prefers front-of-body to underbody gears because they are better able to withstand abuse on rough site work; such as the vehicle being driven from the tip before the body has returned to the lowered position.
Front-of-body gears are also the centre of interest of the equipment produced by the Weston company, in this case because production of the ball-ended type ot ram, employed with a stabilizer, has been discontinued in favour of the heavier type of rigid-base ram gear giving stability without a stabilizer. A new light-duty, single-ram, front-of-body gear, suitable for chassis of 2-, 3and 4-ton capacity, will shortly be added to the range of heavier gears, and a remote-control mechanism is being developed for operation at a convenient point in the cab. Design features include ease of removal for servicing.
In contrast with Majority opinion, a director of Autolifts Engineering Co. Ltd. said underbody gears are generally more stable than front-end but agreed that the latter (with a rigid base) are preferable for long-wheelbase vehicles. Greater importance is attached to selecting the most appropriate type of body for the material to be carried than selecting the most suitable gear, which is often a matter of operator preference. It cannot be over-emphasized, states the director, that operators should, in a typical case, seek expert advice on the choice of bodywork.
Anthony Hoists Ltd. shares the distinction with the Telehoist concern of offering an underbody link gear in its standard range. It is claimed that the gear provides maximum stability by virtue of the wide spacing of the thrust points and their locatio.n near the centre of the body, the hinge-to-lift distance being around 8 ft. in the case of a long-wheelbase, eight-wheeled tipper. The tipping gear is a single-ram unit.
A spokesman of the company repons an increasing demand for sixand eight-wheeled tippers and comments favourably on the tendency of operators to become more selective in their choice of bodywork. This frequently leads to profitable discussions with company technicians and enables a matched combination to be produced that fulfils the operator's particulat needs.
A triangulated sling combined with a compensating cross-head is a feature of Spenborough front-of-body gears of more than 6-ton capacity, the purpose of the cross-head being to prevent body distortion and, with twinrams, to eliminate differential action. A V-type stabilizer is available for longer bodies (up to 21 ft. 6 in.) which incorporates a longitudinal pivot in the sliding block to permit the body to distort torsionally, but prevents lateral movement. All rams with a capacity exceeding 6 tons are of the displacement type featuring internal feed to the tube assembly.
The Milshaw Tipping Gear Co. Ltd. claims that "the advent of lightly constructed bodies has made the stabilizer a necessary part of all long-wheelbase tippers ", and it is pertinent that the company's patented rack-and-pinion stabilizer relieves the ram of all but thrust stresses and obviates " odd-legging" when twin rams are employed.
To achieve maximum stability with rigid-type, front-of-body twin-ram gears fitted to multi-wheel long-wheelbase vehicles, a canopy lifting frame is employed in conjunction with the stabilizer which caters for body lengths up to 21 ft. 3 in., the remaining front-of-body installations being equipped with triangular lifting arms, apart from one model with a single spherical base ram and conventional lifting bracket Underbody gears produced by the company are of the slant type and it is notable that the range includes a twin-ram model with outrigged rams (and stabilizer) which is suitable for bodies up to 18-20 ft