The Origins of Oil-engine Noise
Page 57
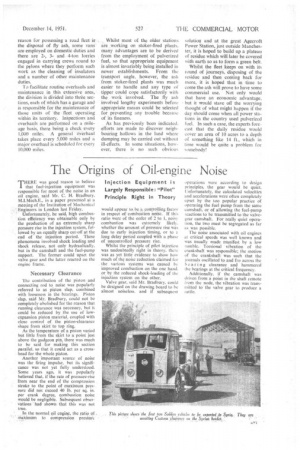
If you've noticed an error in this article please click here to report it so we can fix it.
Injection Equipment is Largely Responsible: "Pilot" Principle Right in Theory
THERE was good reason to believe I that was equipment was responsible for most of the noise in an oil engine, said Mr. C. H. Bradbury, M.I.Mech.E., in a paper presented at a meeting of the Institution of Mechanical Engineers in London last Friday. Unfortunately, he said, high combustion efficiency was obtainable only by the production of an extremely sharp pressure rise in the injection system, fol. lowed by an equally sharp cut-off at the end of the injection period. These phenomena involved shock loading and shock release, not only hydraulically, but in the camshaft and the fuel-pump support. The former could upset the valve gear and the latter reacted on the engine frame.
Necessary Clearance
The contribution of the piston and connecting rod to noise was popularly referred to as piston slap, combined with looseness in the bearings. Piston 'slap, said Mr. Bradbury, could not be completely abolished for the reason that running clearance was necessary, but it could be reduced by the use of lowexpansion piston material, coupled with close control of the piston-clearance shape from skirt to top ring.
As the temperature of a piston varied but little from the skirt to a point just above the gudgeon pin, there was much to be said for making this section parallel, so that it could act as a crosshead for the whole piston.
Another important source of noise was the firing impulse, but its significance was not yet fully understood. Some years ago, it was popularly believed that, if the rate of pressure-rise from near the end of the compression stroke to the point of maximum pressure did not exceed 40 lb. per sq. in. per crank degree, combustion noise would be negligible. Subsequent observations ' had shown. that this was not true.
r In the normal .oil engine, the ratio of
Makfintim to compression preSilic.. _ . .
would appear tr..) be .a coatrolling factor in respect of combustion noise. If this ratio were of the order of 2 to I, noisy combustion was extremely likely. whether the amount of pressure rise was due to early injection timing, or to :1 long delay period coupled With a phase of uncontrolled pressure rise.
Whilst the principle of pilot injection was undoubtedly right in theory, there was as yet little evidence to show how much of the noise reduction claimed for the various systems was caused by improved combustion on the one hand. or by the reduced shock-loading of the injection system on the other.
Valve gear, said Mr. Bradbury, could be designed on the di-awing board to he alinost noiseless, and if subsequent operations were according to design principles, the gear would be quiet. Unfortunately, the calculated velocities and accelerations werenften completely upset by the too popular practice of operating the fuel pump from the same camshaft, or of allowing the fuel-pump reactions to be transmitted to the valvegear camshaft. For really quiet operation, the two must be segregated as far as was possible.
The noise associated with oil engines at critical speeds was well known and was usually made manifest by a low rumble.Torsional vibration of the crankshaft was responsible; the motion of the crankshaft was such that the journals oscillated to and fro across the bearing clearance and hammered the bearings at the critical frequency.
Additionally, if the camshaft was driven from a point in the shaft remote from the node, the vibration was transmitted to the valve gear to produce a rattle.