3enchwise: Lathe sense (26)
Page 35
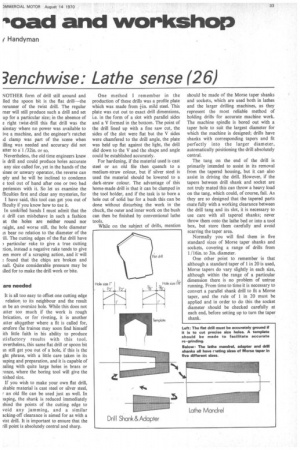
If you've noticed an error in this article please click here to report it so we can fix it.
MOTHER form of drill still around and lied the spoon bit is the flat drill—the rummer of the twist drill. The regular rner will still produce such a drill and set up for a particular size; in the absence of e right twist-drill this flat drill was the ainstay where no power was available to
lye a machine, and the engineer's ratchet•d clamp was part of the scene when illing was needed and accuracy did not atter to a-1 /32in. or so.
Nevertheless, the old time engineers knew is drill and could produce holes accurate any size called for, yet in the hands of the dnee or unwary operator, the reverse can ply and he will be inclined to condemn e tool out of hand after one or two bad periences with it. So let us examine the fficulties first and clear any mysteries, for I have said, this tool can get you out of fficulty if you know how to nse it.
In unskilled hands I must admit that the a drill can misbehave in such a fashion at the holes are neither round nor raight, and worse still, the hole diameter n bear no relation to the diameter of the ill. The cutting edges of the flat drill have
particular rake to give a true cutting tion, instead a negative rake tends to give em more of .a scraping action, and it' will found that the chips are broken and aall. Quite considerable pressure may be died for to make the drill work or bite.
are needed
It is all too easy to offset one cutting edge relation. to its neighbour and the result in be an oversize hole. While this does not atter too much if the work is rough brication, or for riveting, it is another atter altqgether where a fit is called for, ierefore (he trainee may soon find himself ith little faith in his ability to produce ttisfactory results with this tool. evertheless, this same flat drill ot spoon bit in still get you out of a hole, if this is the ght phrase, with a little care taken in its taping and preparation, and it is capable of miling with quite large holes in brass or ,onze, where the boring tool will give the aished size.
If you wish to make your own flat drill, iitable material is cast steel or silver steel, r an old file can be used just as well. In loping, the shank is reduced immediately Dhind the points of the cutting edge to void any jamming, and a similar acking-off clearance is aimed for as with a vist drill. It is important to ensure that the rill point is absolutely central and sharp_
One method I remember in the production of these drills was a profile plate which was made from 3m, mild steel. This plate was cut out to exact drill dimensions, i.e. in the form of a slot with parallel sides and a V formed in the bottom. The point of the drill lined up with a fine saw cut, the sides of the slot were flat but the V sides were chamfered to the drill angle, the plate was held up flat against the light, the drill slid down to the V and the shape and angle could be established accurately.
For hardening, if the material used is cast steel or an old file then quench to a medium-straw colour, but if silver steel is used the material should be lowered to a dark-straw colour. The advantage or this home-made drill is that it can be clamped in the tool holder, and if the task is to bore a hole out of solid bar for a bush this can be done without disturbing the work in the chuck, the outer and inner work on the bush can then be finished by conventional lathe tools.
While on the subject of drills, mention should be made of the Morse taper shanks and sockets, which are used both in lathes and the larger drilling machines, as they represent the most reliable method of holding drills for accurate machine work. The machine spindle is bored out with a taper hole to suit the largest diameter for which the machine is designed; drills have shanks with corresponding tapers and fit perfectly into the larger diameter, automatically positioning the drill absolutely central.
The tang on the end of the drill is primarily intended to assist in its removal from the tapered housing, but it can also assist in driving the drill. However, if the tapers between drill shank and socket are not truly mated this can throw a heavy load on the tang, which could, of course, fail. As they are so designed that the tapered parts .mate fully with a working clearance between the drill tang and its slot, it is necessary to use care with all tapered shanks; never throw them onto the lathe bed or into a tool box, but store them carefully and avoid scarring the taper area.
Normally you will find them in five standard sizes of Morse taper shanks and sockets, covering a range of drills from 1 /16in. to 3in. diameter.
One other point to remember is that although a standard taper of 1 in 20 is used, Morse tapers do vary slightly in each size, although within the range of a particular dimension there is no problem of untrue running. From time to time it is necessary to convert a parallel shank drill to fit a Morse taper, and the rule of 1 in 20 must be applied and in order to do this the socket diameter should be checked carefully at each end, before setting up to turn the taper shank.