This system leaves little to chance
Page 64
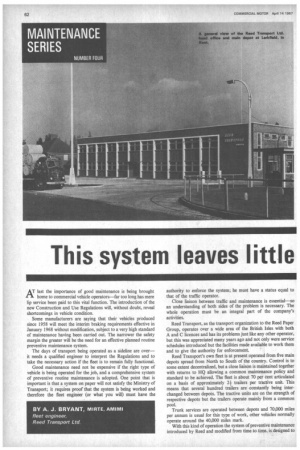
Page 65
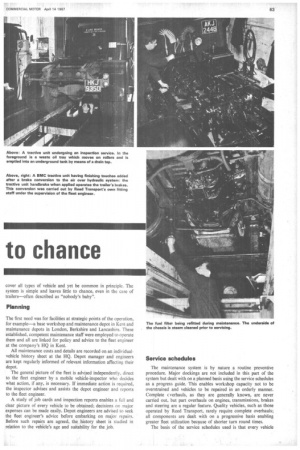
Page 66
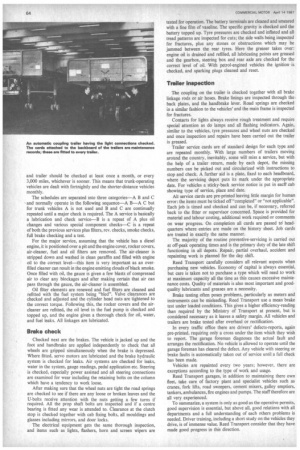
If you've noticed an error in this article please click here to report it so we can fix it.
Ar last the importance of good maintenance is being brought home to commercial vehicle operators—far too long has mere lip service been paid to this vital function. The introduction of the new Construction and Use Regulations will, without doubt, reveal shortcomings in vehicle condition.
Some manufacturers are saying that their vehicles produced since 1958 will meet the interim braking requirements effective in January 1968 without modification, subject to a very high standard of maintenance having been carried out. The narrower the safety margin the greater will be the need for an effective planned routine preventive maintenance system.
The days of transport being operated as a sideline are over— it needs a qualified engineer to interpret the Regulations and to take the necessary action if the fleet is to remain fully functional.
Good maintenance need not be expensive if the right type of vehicle is being operated for the job, and a comprehensive system of preventive routine maintenance is adopted. One point that is important is that a system on paper will not satisfy the Ministry of Transport; it requires proof that the system is being worked and therefore the fleet engineer (or what you will) must have the authority to enforce the system; he must have a status equal to that of the traffic operator.
Close liaison between traffic and maintenance is essential—so an understanding of both sides of the problem is necessary. The whole operation must be an integral part of the company's activities.
Reed Transport, as the transport organization to the Reed Paper Group, operates over a wide area of the British Isles with both A and C licences and has its problems just like any other operator, but this was appreciated many years ago and not only were service schedules introduced but the facilities made available to work them and to give the authority for enforcement.
Reed Transport's own fleet is at present operated from five main depots spread from North to South of the country. Control is to some extent decentralized, but a close liaison is maintained together with returns to HQ allowing a common maintenance policy and standard to be achieved. The fleet is about 70 per cent articulated on a basis of approximately 2+ trailers per tractive unit. This means that several hundred trailers are constantly being interchanged between depots. The tractive units are on the strength of respective depots but the trailers operate mainly from a common pool.
Trunk services are operated between depots and 70,000 miles per annum is usual for this type of work, other vehicles normally operate around the 40,000 miles mark.
With this kind of operation the system of preventive maintenance introduced by Reed and modified from time to time, is designed to cover all types of vehicle and yet be common in principle. The system is simple and leaves little to chance, even in the case of trailers—often described as "nobody's baby".
Planning
The first need was for facilities at strategic points of the operation, for example—a base workshop and maintenance depot in Kent and maintenance depots in London, Berkshire and Lancashire. These established, competent maintenance staff were employed to operate them and all are linked for policy and advice to the fleet engineer at the company's HQ in Kent.
All maintenance costs and details are recorded on an individualvehicle history sheet at the HQ. Depot manager and engineers are kept regularly informed of relevant information affecting their depot.
The general picture of the fleet is advised independently, direct to the fleet engineer by a mobile vehicle-inspector who decides what action, if any, is necessary. If immediate action is required, the inspector advises and assists the depot engineer and reports to the fleet engineer.
A study of job cards and inspection reports enables a full and clear picture of every vehicle to be obtained; decisions on major expenses can be made easily. Depot engineers are advised to seek the fleet engineer's advice before embarking on major repairs. Before such repairs are agreed, the history sheet is studied in relation to the vehicle's age and suitability for the job. The maintenance system is by nature a routine preventive procedure. Major dockings are not included in this part of the system but dealt with on a planned basis using the service schedules as a progress guide. This enables workshop capacity not to be overstrained and vehicles to be repaired in an orderly manner. Complete c verhauls, as they are generally known, are never carried out, but part overhauls on engines, transmissions, brakes and steering are a regular feature. Quality vehicles, such as those operated by Reed Transport, rarely require complete overhauls; all components are dealt with on a progressive basis enabling greater fleet utilization because of shorter turn round times.
The basis of the service schedules used is that every vehicle and trailer should be checked at least once a month, or every 3,000 miles, whichever is sooner. This means that trunk-operating vehicles are dealt with fortnightly and the shorter-distance vehicles monthly.
The schedules are separated into three categories—A B and C and normally operate in the following sequence—A B—A C but for trunk vehicles A is not used and B and C are continually repeated until a major check is required. The A service is basically a lubrication and check service—B is a repeat of A plus oil changes and various special component checks—C is a repeat of both the previous services plus filters, rev, checks, smoke checks, full brake checking and a test.
For the major service, assuming that the vehicle has a diesel engine, it is positioned over a pit and the engine cover, rocker covers, air-cleaner, fuel and oil filters are removed. The air-cleaner is stripped down and washed in clean paraffin and filled with engine oil to the correct level—this item is very important as an overfilled cleaner can result in the engine emitting clouds of black smoke. Once filled with oil, the gauze is given a few blasts of compressed air to clear any blockages and after making certain that air can pass through the gauze, the air-cleaner is assembled.
Oil filter elements are renewed and fuel filters are cleaned and refitted with the fuel system being "bled". Valve clearances are checked and adjusted and the cylinder head nuts are tightened to the correct torque. Following this, the rocker covers and the aircleaner are refitted, the oil level in the fuel pump is checked and topped up, and the engine given a thorough check for oil, water, and fuel leaks. All linkages are lubricated.
Brake check
Checked next are the brakes. The vehicle is jacked up and the foot and handbrake are applied independently to check that all wheels are gripped simultaneously when the brake is depressed. Where fitted, servo motors are lubricated and the brake hydraulic system is checked for leaks. Air systems are checked for leaks, water in the system, gauge readings, pedal application etc. Steering is checked, especially power assisted and all steering connections are examined for wear including the retaining bolts on the column which have a tendency to work loose.
After making sure that the wheel nuts are tight the road springs are checked to see if there are any loose or broken leaves and the U-bolts receive attention with the nuts getting a few turns if required. All the prop shaft bolts are inspected and if a centre bearing is fitted any wear is attended to. Clearance at the clutch stop is checked together with cab fixing bolts, all mouldings and glasses including mirrors, and door locks.
The electrical equipment gets the same thorough inspection, and items such as lights, flashers, horn and screen wipers are tested for operation. The battery terminals are cleaned and smeared with a fine film of vaseline. The specific gravity is checked and the battery topped up. Tyre pressures are checked and inflated and all tread patterns are inspected for cuts; the side walls being inspected for fractures, plus any stones or obstructions which may be jammed between the rear tyres. Here the greaser takes over: engine oil is drained and refilled, all lubricating points are greased and the gearbox, steering box and rear axle are checked for the correct level of oil. With petrol-engined vehicles the ignition is checked, and sparking plugs cleaned and reset.
Trailer inspection The coupling on the trailer is checked together with all brake linkage rods or air hoses. Brake linings are inspected through the,. back plates, and the handbrake lever. Road springs are checked in a similar fashion to the vehicles' and the main frame is inspected for fractures.
Contacts for lights always receive rough treatment and require special attention as do lamps and all flashing indicators. Again, similar to the vehicles, tyre pressures and wheel nuts are checked and once inspection and repairs have been carried out the trailer is greased.
Trailer service cards are of standard design for each type and are repeated monthly. With large numbers of trailers moving around the country, inevitably, some will miss a service, but with the help of a trailer return, made by each depot, the missing numbers can be picked out and circularized with instructions to stop and check. A further aid is a plate, fixed to each headboard, where the servicing depot puts its mark under the appropriate date. For vehicles a sticky-back service notice is put in cacti" cab showing type of service, place and date.
All service cards are pre-printed leaving little margin for human error: the items must be ticked off "completed" or "not applicable". Each job is timed and checked and can be, if necessary, referred back to the fitter or supervisor concerned. Space is provided for material and labour costing, additional work required or comments on wear progress. On completion all cards are passed td headquarters where entries are made on the history sheet. Job cards are treated in exactly the same manner.
The majority of the routine preventive-servicing is carried out at off-peak operating times and is the primary duty of the late shift functioning in all depots. Repair, partial overhaul, accident and repainting work is planned for the day shift.
Reed Transport carefully considers all relevant aspects when purchasing new vehicles. Economy of capital is always essential, but care is taken not to purchase a type which will need to work at maximum capacity all the time as this causes excessive maintenance costs. Quality of materials is also most important and goodquality lubricants and greases are a necessity.
Brake testing often poses problems, particularly as meters and instruments can be misleading. Reed Transport use a mean brake test under loaded conditions. This gives a higher efficiency-reading than required by the Ministry of Transport at present, but is considered necessary as it leaves a safety margin. All vehicles and trailers are brake tested after overhaul or rectification.
In every traffic office there are drivers' defects-reports, again pre-printed, requiring only a cross under the item which they wish to report. The garage foreman diagnoses the actual fault and arranges the rectification. No vehicle is allowed to operate until the garage foreman has cleared the defect. Any vehicle with steering or brake faults is automatically taken out of service until a full check has been made.
Vehicles are repainted every two years; however, there are exceptions according to the type of work and usage.
Reed Transport garages, in addition to maintaining there own fleet, take care of factory plant and specialist vehicles such as cranes, fork lifts, road sweepers, cement mixers, gulley emptiers, tankers, ambulances, fire engines and pumps. The staff therefore are all very experienced.
To summarize, a system is only as good as the operative permits, good supervision is essential, but above all, good relations with all departments and a full understanding of each others problems is needed. Driver training, including a short study on the vehicles they drive, is of immense value. Reed Transport consider that they have made good progress in this direction.