TARGET FOR THE FUTURE
Page 57
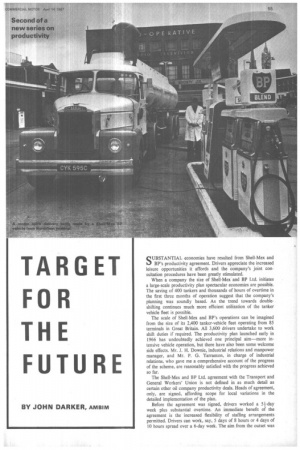
Page 58
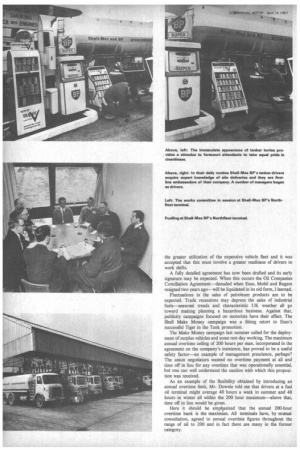
Page 59

Page 60

If you've noticed an error in this article please click here to report it so we can fix it.
BY JOHN DARKER, Ameim
SUBSTANTIAL economies have resulted from Shell-Mex and BP's productivity agreement. Drivers appreciate the increased leisure opportunities it affords and the company's joint consultation procedures have been greatly stimulated.
When a company the size of Shell-Mex and BP Ltd. initiates a large-scale productivity plan spectacular economies are possible. The saving of 400 tankers and thousands of hours of overtime in the first three months of operation suggest that the company's planning was soundly based. As the trend towards doubleshifting continues much more efficient utilization of the tanker vehicle fleet is possible.
The scale of Shell-Mex and BP's operations can be imagined from the size of its 2,400 tanker-vehicle fleet operating from 85 terminals in Great Britain. All 3,600 drivers undertake to work shift duties if required. The productivity plan launched early in 1966 has undoubtedly achieved one principal aim—more intensive vehicle operation, but there have also been some welcome side effects. Mr. J. H. Downie, industrial relations and manpower manager, and Mr. P. G. Yarranton, in charge of industrial relations, who gave me a comprehensive account of the progress of the scheme, are reasonably satisfied with the progress achieved so far.
The Shell-Mex and BP Ltd. agreement with the Transport and General Workers' Union is not defined in as much detail as certain other oil company productivity deals. Heads of agreement, only, are signed, affording scope for local variations in the detailed implementation of the plan.
Before the agreement was signed, drivers worked a 5-Hay week plus substantial overtime. An immediate benefit of the agreement is the increased flexibility of staffing arrangements permitted. Drivers can work, say, 5 days of 8 hours or 4 days of 10 hours spread over a 6-day week. The aim from the outset was the greater utilization of the expensive vehicle fleet and it was accepted that this must involve a greater readiness of drivers to work shifts.
A fully detailed agreement has now been drafted and its early signature may be expected. When this occurs the Oil Companies Conciliation Agreement—denuded when Esso, Mobil and Regent resigned two years ago—will be liquidated in its old form, I learned.
Fluctuations in the sales of petroleum products are to be expected. Trade recessions may depress the sales of industrial fuels—seasonal trends and characteristic UK weather all go toward making planning a hazardous business. Against that, publicity campaigns focused on motorists have their effect. The Shell Make Money campaign was a fitting retort to Esso's successful Tiger in the Tank promotion.
The Make Money campaign last summer called for the deployment of surplus vehicles and some rest-day working. The maximum annual overtime ceiling of 200 hours per man, incorporated in the agreement on the company's insistence, has proved to be a useful safety factor—an example of management prescience, perhaps? The union negotiators wanted no overtime payment at all and time off in lieu for any overtime that was operationally essential, but one can well understand the caution with which this proposition was received.
As an example of the flexibility obtained by introducing an annual overtime limit, Mr. Downie told me that drivers at a fuel oil terminal might average 40 hours a week in summer and 48 hours in winter all within the 200 hour maximum—above that, time off in lieu would be given.
Here it should be emphasized that the annual 200-hour overtime bank is the maximum. All terminals have, by mutual consultation, agreed to annual overtime figures throughout the range of nil to 200 and in fact there are many in the former category. Although Shell-Mex and BP is alive to the advantages of job interchanges between terminal and driving staff—each undertaking the other's duties in emergency—Mr. Downie thought that this aspect should not be overstressed. "We are rather leaner with the establishments of terminal operators so that in our case no marked economies would result" He continued: "The benefit we have received has come mainly from the greater vehicle utilization and from the improved standards of efficiency, based on the intensive method studies carried out. The need of drivers to 'jack up' their earnings by unnecessary overtime was abolished by the enhanced pay structure of the productivity agreement. Drivers return to depots earlier and become available for other work."
asked Mr. Downie if he had reason to think that any drivers were undertaking other driving jobs in their spare time. The risk of this appening in the transport industry which for generations has su ered from an over-long working week, is, I know, a real one. He told me he has no evidence at all of drivers "moon-lighting," although this might be happening to some extent. There is considerable evidence that drivers appreciate their increased leisure.
Mr. arranton agrees. The lives of many drivers, he believes, have b en transformed by increased leisure opportunities. One driver Ias said to him: "I can play golf daily and meet people I would pever have had the opportunity of meeting before the produc vity scheme started. I wouldn't change back to the old system çor all the tea in China." Exhibitions of hobbies of Shell-Mex and BP employees support the contention that leisure is now a big factor f r drivers.
In terms of average length of the working week, I learned that the 51 hours average for the company has been reduced to 42--and ven allowing for Sunday and rest day working at busy periods the overall average would not exceed 44 hours per week.
The roductivity plan, I was told, has had some effect on maintenance employees, though steps taken in earlier years have not left mu h scope for spectacular improvements here. Strict demarcation lin s between various categories of maintenance staffs are not a prob em—they were reduced some time ago. But in the past
year there have been further studies of ways to improve productivity and efficiency at the Fulham repair centre, particularly designed to help in the measurement of productivity improvements, not easily identifiable in this branch of engineering.
Higher pay for maintenance staff, more in line with competitive industries, has helped labour recruitment. Shell-Mex and BP run one of the best schemes for vehicle mechanics—and frankly regard their efforts here as in part a contribution to the trade.
I asked Mr. Downie if the company is conscious that the efficiencies achieved after the productivity agreement was implemented could and should have been achieved years ago. He said he did not think so. The industry had been controlled by the Petroleum Board until 1951 and in the decade 1950 to 1960 there had been a vast growth of trade—a situation not conducive to any marked reduction in the overtime worked. There has been a gradual determination to control overtime more strictly, a tendency that has grown with increasingly competitive conditions in the industry.
I was particularly pleased to hear from Mr. Downie and Mr. Yarranton that the long-established works committees of the company have been given a new lease of life by the productivity agreement. The committees have been actively involved in the discussions leading up to the target work weeks defined for each terminal. Shell-Mex and BP Ltd has its own work study specialists and they play a key part in the formulation of standards of performance—in addition constant regard is given to the need to revise standards to take account of changes in conditions.
Control systems are in hand to measure the performance of each terminal and soon this will be extended to the work of each driver. The terminal managers, of course, know the individual circumstances of all drivers under their control; men regularly well below the average performance standard may have compensating merits, but the position clearly needs to be watched.
Instancing the interest of the works committees in the productivity agreement, Mr. Downie told me of one committee who have jointly signed a notice to the staff setting out key points in making their own terminal fully efficient. "The traditional three Ts—Tea, Towels and Toilets—is not so much in evidence at works committee discussions today; they have their teeth in practical steps to promote more efficient working." Mr. Yarranton told me of a request from the staff of a terminal for a personal talk from, "one of the company team who negotiated the productivity scheme". He talked at length to a meeting attended by practically all the employees and it was very obvious that he had enjoyed the animated discussion that ensued.
The vast ramifications of the company's interests—in distributing the products of Shell International and BP Petroleum Ltd.—make it difficult for works committee discussions to extend to wider questions of policy and organization but Mr. Yarranton stressed that "Know Your Company" meetings are held periodically and these provide an opportunity for staff of all grades to learn of wider aspects and ask as many pertinent questions—as they wish.
Promotion and training opportunities are available to any employee with the right keenness and the ability to profit from them. Mr. Yarranton affirmed his own strongly held view that the company should be interested in any single employee of any level with a desire to know more about the wider operations of so complex a group. "Employees have every right to ask questions and get adequate answers, and, indeed, encouragement in obtaining qualifications whereby they can help themselves and their company to the limit of their abilities."
Despite the size of the Shell-Mex and BP organization, terminal establishments are relatively small—a large terminal would employ about 300 people and the average terminal no more than 150. The performance of each terminal is recorded graphically at head office but comparative results are not recorded in competitive "league table" form. Mr. Yarranton explained that the work of the terminals varies so much that any attempt to assess comparative efficiencies in simple tabular form would be unfair; some assessment of• managerial performance is, of course, undertaken, but this is a different matter.
Suggestion schemes in transport organizations are notregrettably—generally successful in this country and Shell-Mex and BP does not think they are practicable in its transport operations. "With 85 terminals", Mr. Yarranton suggested, "it would be very difficult to prove that a particular suggestion put forward by an individual driver or plant operator was unique. Almost certainly, someone else would have thought of it and it might well be found to have been applied." The better approach is for ideas to be investigated promptly at the terminals and adopted forthwith if they are practicable.
A very useful idea in operation at the company's terminals is the provision of "mini-libraries"—small collections of text books, current company publications (particularly those touching on relationships with dealers and contractors) and technical journals such as COMMERCIAL MOTOR. Drivers and other employees may consult or borrow particular literature on request.
It would be unfair to suggest that industrial training in Shell-Mex and BP has expanded as a result of the productivity agreement. The company has been known for many years as a leader in the field of training. The recently announced training board for the Petroleum Industry, due to commence operations this spring, will no doubt be grateful for much of the experience built up over the years by the compahy.
This said, it is true to say that the productivity agreement provisions have had an impact on the training programme. Category 1 drivers, for example, must be able to drive all types of vehicles. "On-the-job" training for operatives, part of whose duties involves driving when necessary, is increasing; some courses may involve the release of staff for half or full days during working hours over a period of as much as four ,months. The constant pressure, as with all training programmes, is to ensure that all staff employed at terminals are qualified for the greatest possible range of duties.
In the first three months following the signing of the productivity agreement no less than 540 Class 2 drivers have received additional training to bring them up to Class 1 standard. Some of the driver training has been provided by the company's senior driving staff; quite a number of drivers have been on commercial vehicle drivers courses arranged by the British School of Motoring. Of the 540 drivers trained, only 20 failed to make the Class 1 grade. Static plant operators, too, who require to be able to move vehicles within terminal boundaries have also been trained to conform to the more flexible staffing requirements of the agreement.
The foregoing, I suggest, holds much promise for the future of the excitingly competitive petroleum distribution industry. Many of the attitudes generated by the careful preparation of productivity agreements on the scale of Shell-Mex and BP's are capable of wider application in the commercial road transport field. The drastic curtailment of the traditionally high overtime and the greater opportunities provided by increased leisure opportunities, coupled with substantial savings in operating costs, would have been regarded as utopian in the extreme a year or two ago. Their effect on road transport operations generally cannot be ignored.