Some Little-known
Page 45
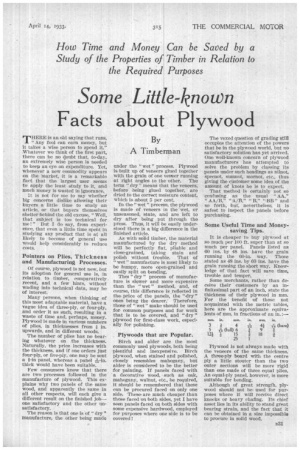
If you've noticed an error in this article please click here to report it so we can fix it.
Facts about Plywood
rr HERE is an old saying that runs, "Any fool can earn money, but it takes a wise person to spend it." Whatever we think of the first part, there can be no doubt that, to-day, an extremely wise person is needed to 'keep an eye on expenditure. Yet, whenever a new commodity appears on the market, it is a remarkable fact that the largest user seems to apply the least study to it, and much money is wasted in ignorance.
It is not for me to say whether big concerns dislike allowing their buyers a little time to study an article, or that buyers themselves shelter behind the old excuse, "Well, that subject is too technical for mel" But I do say, from experience, that even a little time spent in studying any product that is at all likely to become of general use would help considerably to reduce costs.
Pointers on Plies, Thickness and Manufacturing Processes.
Of course, plywood is not new, but Its adoption for general use is, in relation to timber, comparatively recent, and a few hints, without wading into technical data, may be of interest.
Many persons, when thinking of this most adaptable material, have a vague idea of three-ply, or four-ply, and order it as such, resulting in a waste of time and, perhaps, money. Plywood is made in various numbers of plies, in thicknesses from t in. upwards, and in different woods.
The number of plies has no bearing whatever on the thickness. Naturally, the price increases with the thickness, and if one orders just four-ply, or five-ply, one may be sent a fin panel, whereas a panel ige-in. thick would have been suitable.
Few consumers know that there are two processes followed in the manufacture of plywood. This explains why two panels of the same wood, and apparently the same in all other respects, will each give a different result on the finished job-one satisfactory and the other unsatisfactory.
The reason is that one is of " dry " manufacture, the other being made under the " wet " process. Plywood is built up of veneers glued together With the grain of one veneer running at right angles to the other. The term " dry " means that the veneers, before being glued together, are dried to the correct moisture content, which is about 5 per cent.
In the "wet "process, the plywood is made of veneers in the wet, or unseasoned, state, and are left to dry after being put through the press. Thus, it will be easily understood there is a big difference in the finished article.
As with solid timber, the material manufactured by the dry method will be perfectly flat, pliable and close-grained., taking stain and polish without trouble. That of " wet " manufacture is most likely to be bumpy, more open-grained and easily split on bending.
Theis " dry " process of manufacture is slower and more expensive than the " wet " method, and, of course, this difference is reflected in the, price of the panels, the "dry" ones being the dearer. Therefore, those of " wet " make should be used for common purposes and for work that is to be covered, and " dry " plywood for first-class work, especially for polishing.
Plywoods that are Popular.
Birch and alder are the most commonly used plywoods, both being plentiful and inexpensive. Birch plywood, when stained and polished, closely resembles mahogany, but alder is considered to be the better for painting. If panels laced with a decorative wood, such as oak, mahogany, walnut, etc., be required, It should be remembered that these can be procured faced on only one side. These-are much cheaper than those faced on both sides, yet I have seen panels laced on both sides with some expensive hardwood, employed for purposes where one side is to be covered! The vexed question of grading still occupies the attention of the powers that be in the plywood world, but no satisfactory solution has yet arrived. One well-known concern of plywood manufacturers has attempted to solve the problem by classing its panels under such headings as nilnot, specnot, sumnot, mornot, etc., thus giving the customer some idea of the amount of knots he is to expect.
That method is certainly not so confusing as the usual "AA," " AA/B," " A/B," "B," "BB" and so forth, but, nevertheless, it is safest to inspect the panels before purchasing.
Some Useful Time and Moneysaving Tips.
It is cheaper to buy plywood at so much per 100 ft. super than at so much per panel. Panels listed as 60 ins. by 48 ins, have the grain running the 60-in. way. Those stated as 48 ins. by 60 ins, have the grain running the short way. Knowledge of that fact will save time, trouble and temper.
Some merchants, rather than deceive their customers by an infinitesimal part o an inch, state the thickness of their plywood in ram. For the benefit of those not acquainted with the metric tables, here are the approximate equivalents of mm in fractions of an in. :—
mm. in. mm. in. mrn. in.
3 4 4 14r(bare) 5 (full)6 9
121 15 g 18 / Plywood is not always made with the veneers of the same thickness. A three-ply board with the centre ply a little stouter than the two outer sections will be more rigid than one made of three equal plies. An equal-ply panel, however, is more suitable for bending.
Although of great strength, plywood should not be used for purposes where it will receive direct knocks or heavy chafing. Its chief asset lies in its ability to stand great bearing strain, and the fact' that it can be obtained in a size impossible to procure in solid wood.