OF INTEREST TO REPAIRERS.
Page 29
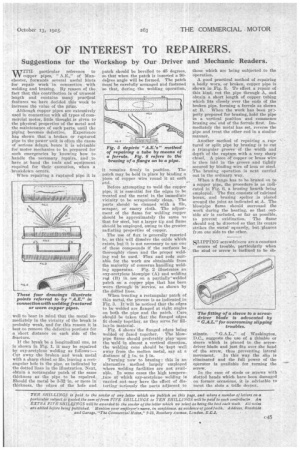
If you've noticed an error in this article please click here to report it so we can fix it.
Suggestions for the Workshop by Our Driver and Mechanic Readers.
WITH particular reference to copper pipes, • " A.E.," of Manchester, forwards several useful hints for repair work in connection with welding and brazing. By reason of the. fact that this contribution is of unusual length and contains many practical features we have decided this week to increase the value of the prize.
Although copper pipes are extensively used in connection with all types of commercial motor, little thought is given to the physical properties of the metal and the maintenance of such parts, until the piping becomes defective. Experience has shown that a broken or ruptured pipe in the power' unit is often the cause of serious delays, hence it is advisable for motor Mechanics to be prepared for such emergencies by knowing how to handle the necessary repairs, aid to have at hand the tools and equipment required for • their execution, when. a • breakdown occurs.
When repairing a ruptured pipe it is well to bear in mind that the metal immediately in the vicinity of the break is probably weak, and for this reason it is best to remove the defective portions for a short distance on each side of the fracture.
If the break be a longitudinal one, as is shown in Fig. I. it may be repaired by oxy-acetylene welding as follows :-Gut away the broken and weak metal with a sharp chisel or file, leaving a rectangular hole in the pipe, as indicated by the dotted lines in the illustration. Next, obtain a rectangular patch of the same thickness as the pipe to be repaired., should the metal be 3-32 in. or more in thickness, the edges of the hole and
patch should be bevelled to 45 degrees, so that when the patch is inserted a fi0dekree angle will be formed. The patch must he carefully arranged and fastened RO that, during the welding operation, it remains firmly in position. The patch may be held in place by binding a piece of copper wire round it at each end.
Before attempting to weld the copper pipe, it is essential for the edges to be treated and the metal in the immediate vicinity to be scrupulously clean: The parts should be cleaned with a file, scraper, or emery cloth. The adjustment of the flame for welding copper. should be approXimately the same Is that for steel, but a larger tip and flame should be employed, owing to the greater radiating properties of copper. .
The use of Jinx is generally resorted to, as this will dissolve the oxide which exists, but it is not necessary to use one of these compounds if the surfaces be thoroughly clean and the proper welding rod be used. Flux and rods suitable for the work are obtainable from the majority of concerns handling weld ing apparatus. Fig. 2 illustrates an oxy-acetylene blowpipe (A) and welding rad (B) in rise on a partially welded patch on a copper pipe, that has been worn through in service, as shown by the dOtted When treating a rectangular patch of thin metal, the process is as indicated. in Fig. 3. It will be noticed that the edges to be welded are flanged at right angles on both the pipe and the patch. Care should be taken that the flanged edges fit closely together, as they serve for filling-in material.
Fig. 4 shows the flanged edges being welded or fused together. The blowpipe flame should preferably play 'upon the Weld in almost a vertical direction, the Welding cone should be kept well away from the molten metal, say at a distance of in, to 3 in.
Turning now to brazing : this is an alternative method largely employed where welding facilities are not available. In some eases the high temperaJune at which oxy-acetylenewelding is carried out may have the effect of distorting seriously the parts adjacent to those which are being subjected to the operation.
A good practical method of repairing a badly worn, or broken, copper pipe is shown in Fig. 5. To effect a repair of this kind, cut the pipe through A, and obtain a short length of copper tubing which fits closely over the ends of the broken pipe, forming a ferrule as shown at B. When the work has been perly prepared for brazing, hold the pipe in a vertical position and commence brazing one end of the ferrule first. Immediately the metal has set, reverse the pipe and treat the other end in a similar manner.
Another 'method of repairing a ruptured or split pipe by brazing is to cut a triangular groove Of the width and depth of the rupture with a very sharp chisel. A piece of copper or brass wire is then laid in the groove and tightly secured by binding wire of iron or steel. The brazing operation is next carried out in the ordinary way.
When a flange has to be brazed on to a copper pipe, the procedure is as
mdibtcd in Fig. 6, a brazing hearth being employed. The flux consists of calcined borax, and brazing spelter is plated around the joint as indicated at A. The blowpipe flame should surround the work during the heating, so that outside air is excluded,. se fur as possible, to prevent oxidization. The flame should not be directed so that its centre strikes the metalsquarely, but glances from one side to the other.
stinate. , " G.A.L.," of Washington, D.C., suggests the use of a thimble or sleeve Which is pinned to the screwdriver blade and just fits over the head of the screw, thus preventing lateral
movement. In this way the slip is eliminated and the full power of the operator is available for turning the screw.
In the case a studs or screws with slotted beads which have been damaged on •former occasions, it is . advisable to recut the slots a trifle deeper.