From the by Graham Montgomeric I_VM - 0) Lqjl it 0 100( 0 I
Page 26
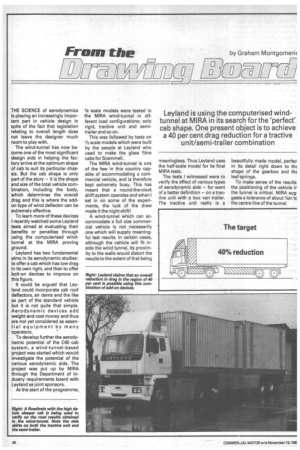
Page 27
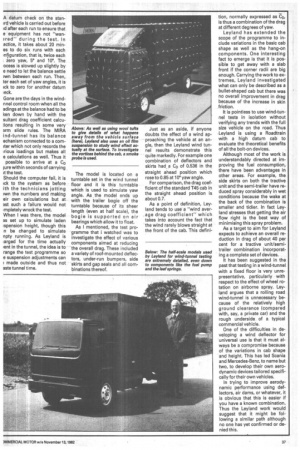
If you've noticed an error in this article please click here to report it so we can fix it.
Leyland is using the computerised windtunnel at MIRA in its search for the 'perfect' cab shape. One present object is to achieve a 40 per cent drag reduction for a tractive unit/semi-trailer combination
THE SCIENCE of aerodynamics is playing an increasingly important part in vehicle design in spite of the fact that legislation relating to overall length does not leave the designer much room to play with.
The wind-tunnel has now become one of the most significant design aids in helping the factory arrive at the optimum shape of cab to suit its particular chassis. But the cab shape is only part of the story — it is the shape and size of the total vehicle combination, including the body, which determines the overall drag and this is where the addon type of wind deflector can be extremely effective.
To learn more of these devices I recently watched some Leyland tests aimed at evaluating their benefits or penalties through using the computerised windtunnel at the MIRA proving ground.
Leyland has two fundamental aims in its aerodynamic studies: to offer a cab which has low drag in its own right, and then to offer bolt-on devices to improve on this figure.
It could be argued that Leyland could incorporate cab roof deflectors, air dams and the like as part of the standard vehicle but it is not quite that simple. Aerodynamic devices add weight and cost money and thus are not yet considered as essential equipment by many operators.
To develop further the aerodynamic potential of the C40 cab system, a wind-tunnel-based project was started which would investigate the potential of the various aerodynamic aids. The project was put up by MIRA through the Department of Industry requirements board with Leyland as joint sponsors.
At the start of the programme, Vs scale models were tested in the MIRA wind-tunnel in different load configurations; solo rigid, tractive unit and semitrailer and so on.
This was followed by tests on 1/2 scale models which were built by the people at Leyland who used to make the glass fibre cabs for Scammell.
The MIRA wind-tunnel is one of the few in this country capable of accommodating a commercial vehicle, and is therefore kept extremely busy. This has meant that a round-the-clock shift system operates and when I sat in on some of the experiments, the luck of the draw made it the night shift!
A wind-tunnel which can accommodate a full size commercial vehicle is not necessarily one which will supply meaningful test results. In certain cases, although the vehicle will fit inside the wind tunnel, its proximity to the walls would distort the results to the extent of that being meaningless. Thus Leyland uses the half-scale model for its final MIRA tests.
The tests I witnessed were to verify the effect of various types of aerodynamic aids — for want of a better definition — on a tractive unit with a box van trailer. The tractive unit really is a
beautifully made model, perfecl in its detail right down to thE shape of the gearbox and the leaf springs.
To make sense of the results, the positioning of the vehicle in the tunnel is critical. MIRA suggests a tolerance of about 1/4in tc the centre line of the tunnel.
A datum check on the Stanrd vehicle is carried out before id after each run to ensure that a equipment has not "wan)red" during the test. In actice, it takes about' 20 mines to do six runs with each infigu ration, that is, twice each zero yaw, 5° and 10°. The ocess is slowed up slightly by e need to let the balance settle )wn between each run. Then, ter each set of yaw angles, it is ick to zero for another datum eck.
Gone are the days in the windnnel control room when all the sdings at the balance had to be ken down by hand with the suitant drag coefficient calcuions resulting in some very arm slide rules. The MIRA ind-tunnel has its balance echanism connected to a comiter which not only records the Irious loadings but makes all e calculations as well. Thus it possible to arrive at a CD pure within seconds of carrying it the test.
Should the computer fail, it is ick to the system as before ith the technicians jotting )wn the numbers and making eir own calculations but at. ast such a failure would not ■ mpletely wreck the test.
When I was there, the model as set up to simulate laden Ispension height, though this n be changed to simulate npty running. As Leyland is larged for the time actually ent in the tunnel, the idea is to range the test programme so e suspension adjustments can made outside and thus not aste tunnel time. The model is located on a turntable set in the wind tunnel floor and it is this turntable which is used to simulate yaw angle. As the model ends up with the trailer bogie off the turntable because of its sheer length (even at half scale), the bogie is supported on air bearings which allow it to float.
As I mentioned, the test programme that i watched was to investigate the effect of various components aimed at reducing the overall drag. These included a variety of roof-mounted deflectors, under-run bumpers, side skirts and gap seals and all combinations thereof. Just as an aside, if anyone doubts the effect of a wind approaching the vehicle at an angle, then the Leyland wind tunnel results demonstrate this quite markedly. For example one combination of deflectors and skirts had_a CD of 0.536 in the straight ahead position which rose to 0.85 at 10° yaw angle.
For comparison, the drag coefficient of the standard T45 cab in the straight ahead position is about 0.7.
As a point of definition, Ley land tends to use a "wind average drag coefficient" which takes into account the fact that the wind rarely blows straight at the front of the cab. This defini tion, normally expressed as to, is thus a combination of the drag at different degrees of yaw.
Leyland has extended the scope of the programme to include variations in the basic cab shape as well as the hang-on components. One interesting fact to emerge is that it is possible to get away with a slab front if the corner radii are big enough. Carrying the work to extremes, Leyland investigated what can only be described as a bullet-shaped cab but there was no overall improvement in drag because of the increase in skin friction.
It is pointless to use wind-tunnel tests in isolation without verifying any trends with the full size vehicle on the road. Thus Leyland is using a Roadtrain with a high datum cab to evaluate the theoretical benefits of all the bolt-on devices.
Although most of the work is understandably directed at improving the fuel consumption, there have been advantages in other areas. For example, the side skirts on both the tractive unit and the semi-trailer have reduced spray considerably in wet conditions because the wake at the back of the combination is smaller and tidier. In fact Leyland stresses that getting the air flow right is the best way of minimising this spray problem.
As a target to aim for Leyland expects to achieve an overall reduction in drag of about 40 per cent for a tractive unit/semitrailer combination incorporating a complete set of devices.
It has been suggested in the past that testing in a wind-tunnel with a fixed floor is very unrepresentative, particularly with respect to the effect of wheel rotation on airborne spray. Leyland argues that a rolling road wind-tunnel is unnecessary because of the relatively high ground clearance (compared with, say, a private car) and the rough underside of a typical commercial vehicle.
One of the difficulties in developing a wind deflector for universal use is that it must always be a compromise because of the variations in cab shape and height. This has led Scania and Mercedes-Benz, to name but two, to develop their own aerodynamic devices tailored specifically for their own vehicles.
In trying to improve aerodynamic performance using deflectors, air dams, or whatever, it is obvious that this is easier if you have a known combination. Thus the Leyland work would suggest that it might be following a similar path although no one has yet confirmed or denied this.